Welcome to the TOD blog
Latest blog posts
Event guides, bucket-list adventure guides, gear advice, guides to the best places plus tips and advice on wellbeing and more.
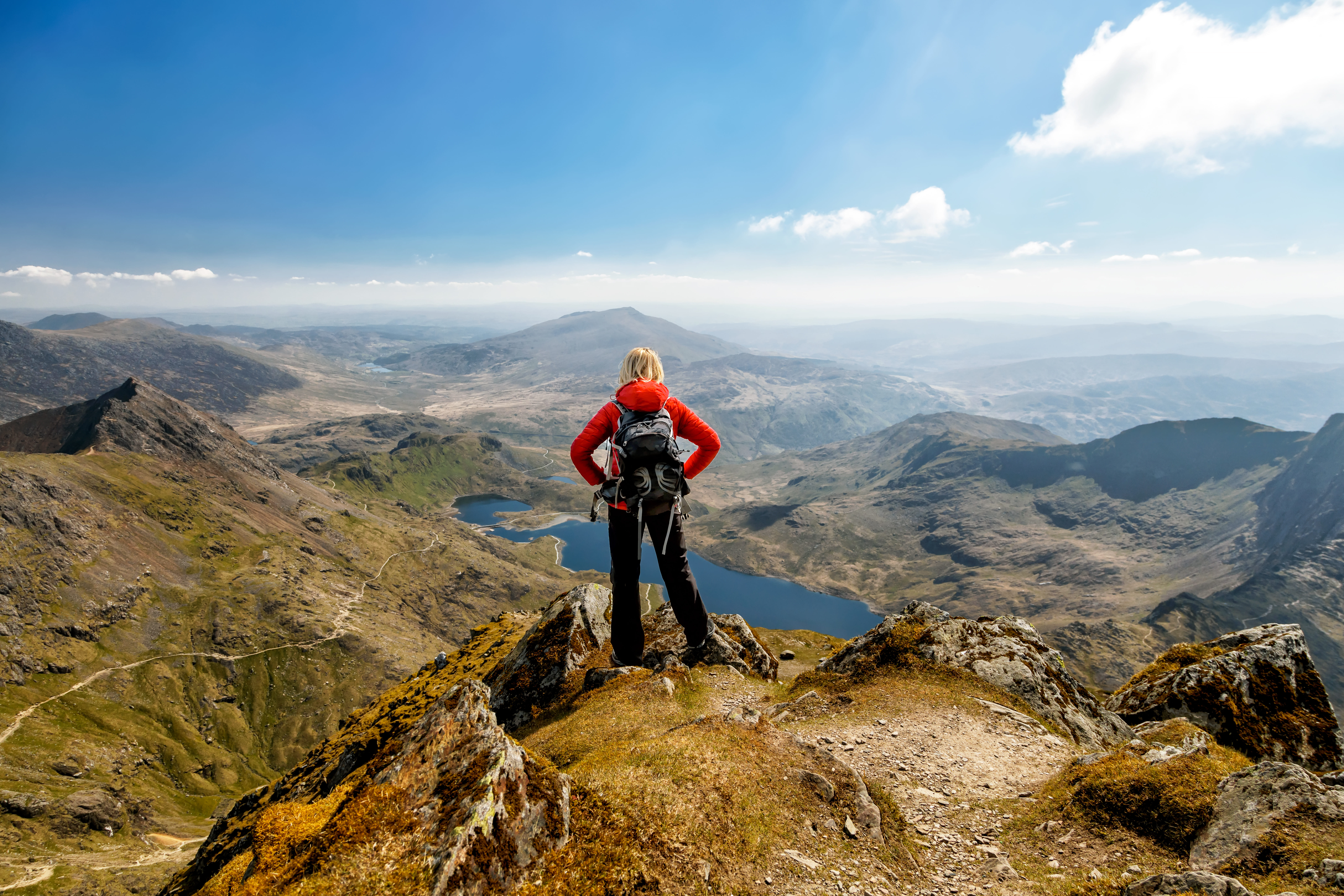
- 15 mins read
Your Guide to Conquering Snowdonia's Best Outdoors Events
Single event or triple challenge? Unleash your adventurous spirit in a legendary landscape.
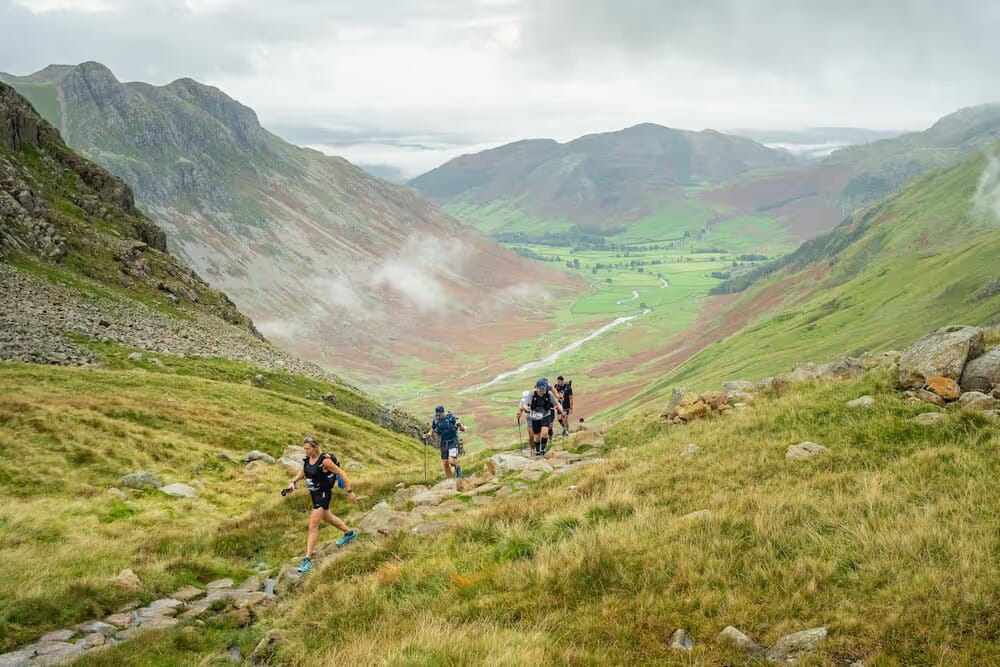
- 10 mins read
Race 101: the 13 Valleys Ultra
Introducing the 13 Valleys Ultra plus the event's shorter distance options, helping you to push your limits and get involved!
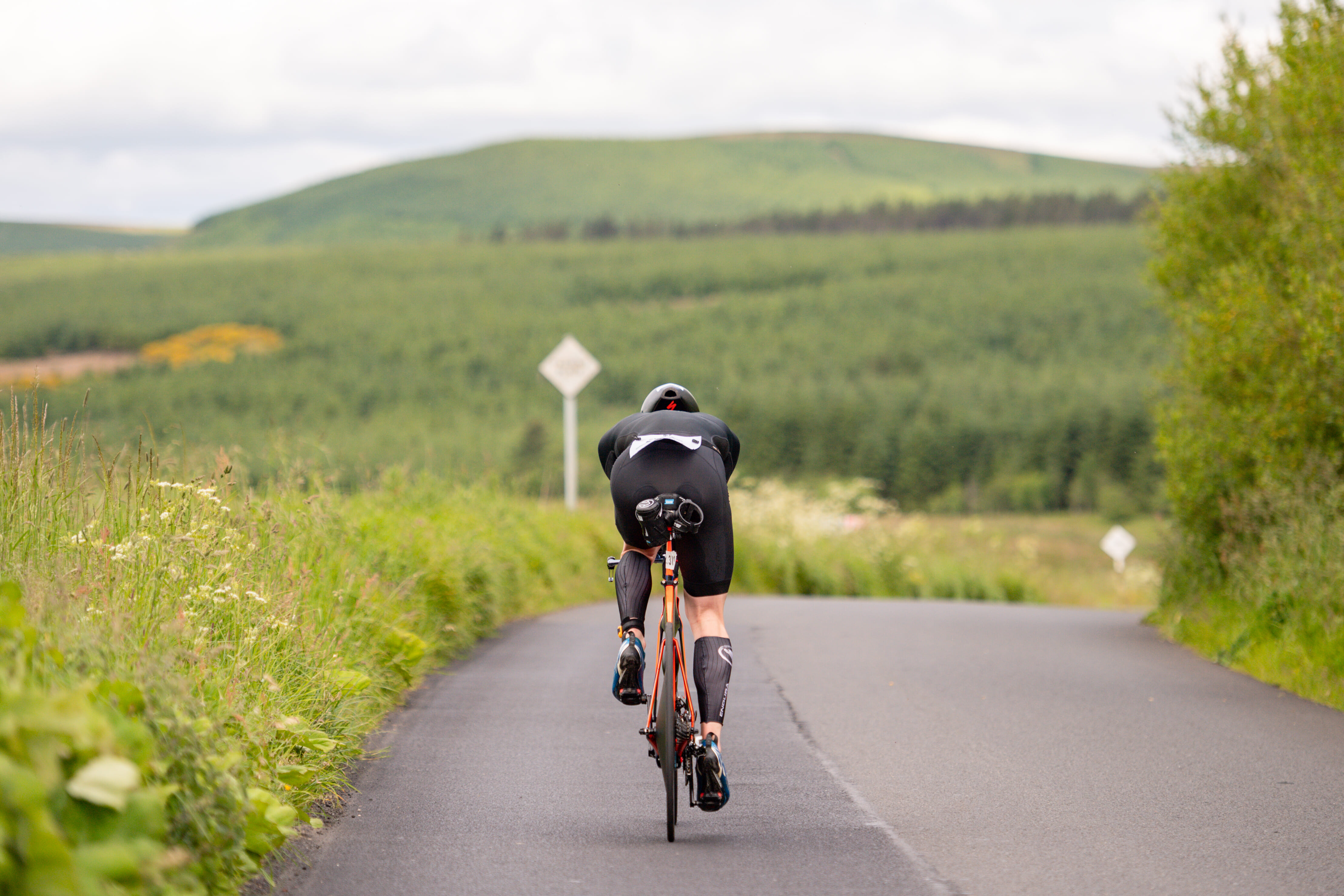
- 10 mins read
The best triathlons in the UK
From beginner races to ultra challenges, swim-bike-runs are the UK's favourite multi-sport events - these are the triathlons that you need to have on your radar.
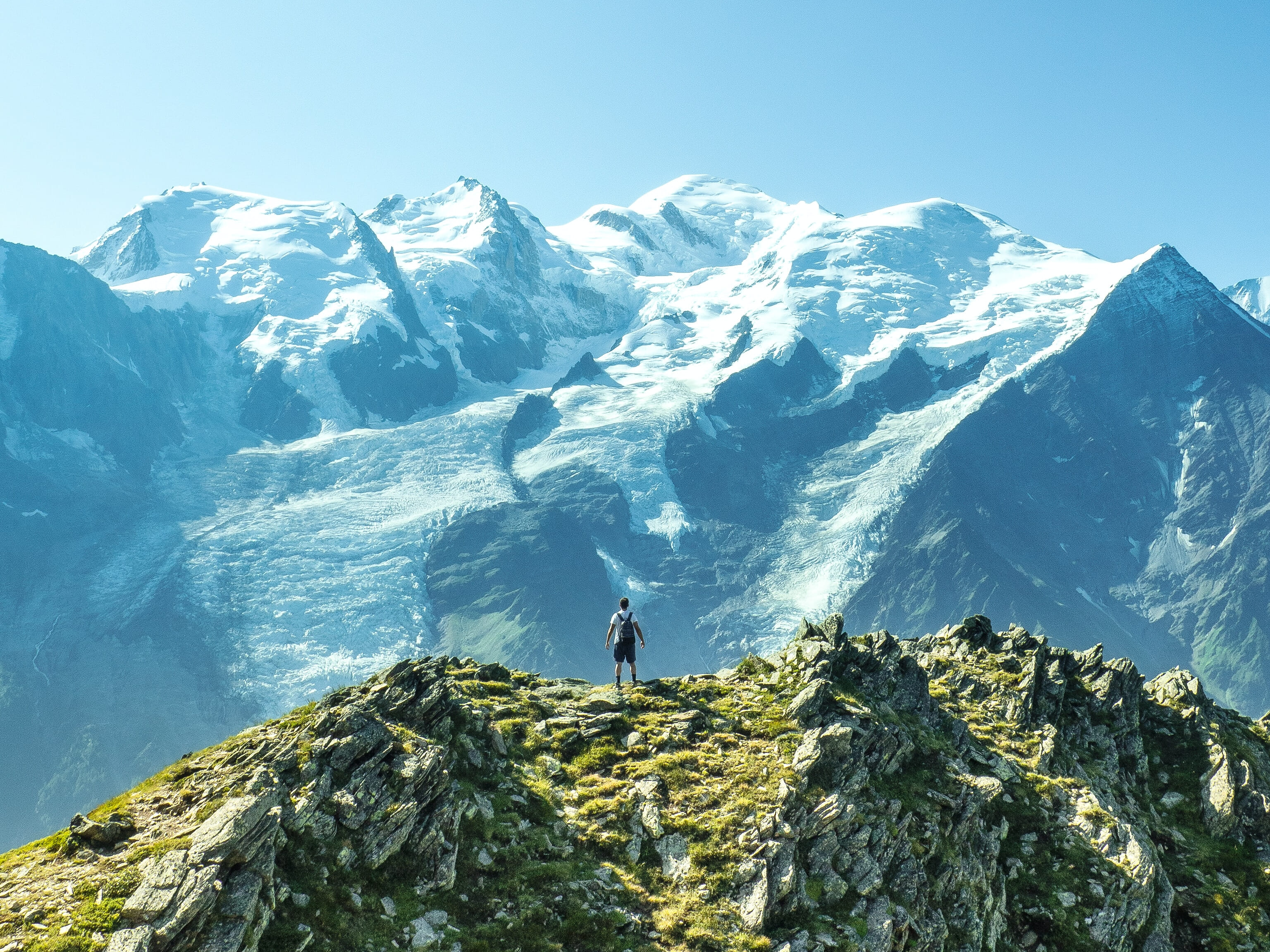
- 10 mins read
Unforgettable adventures to book this summer
Summer holiday season is upon us and we're rounding up the best overseas adventures that you can book onto right now!
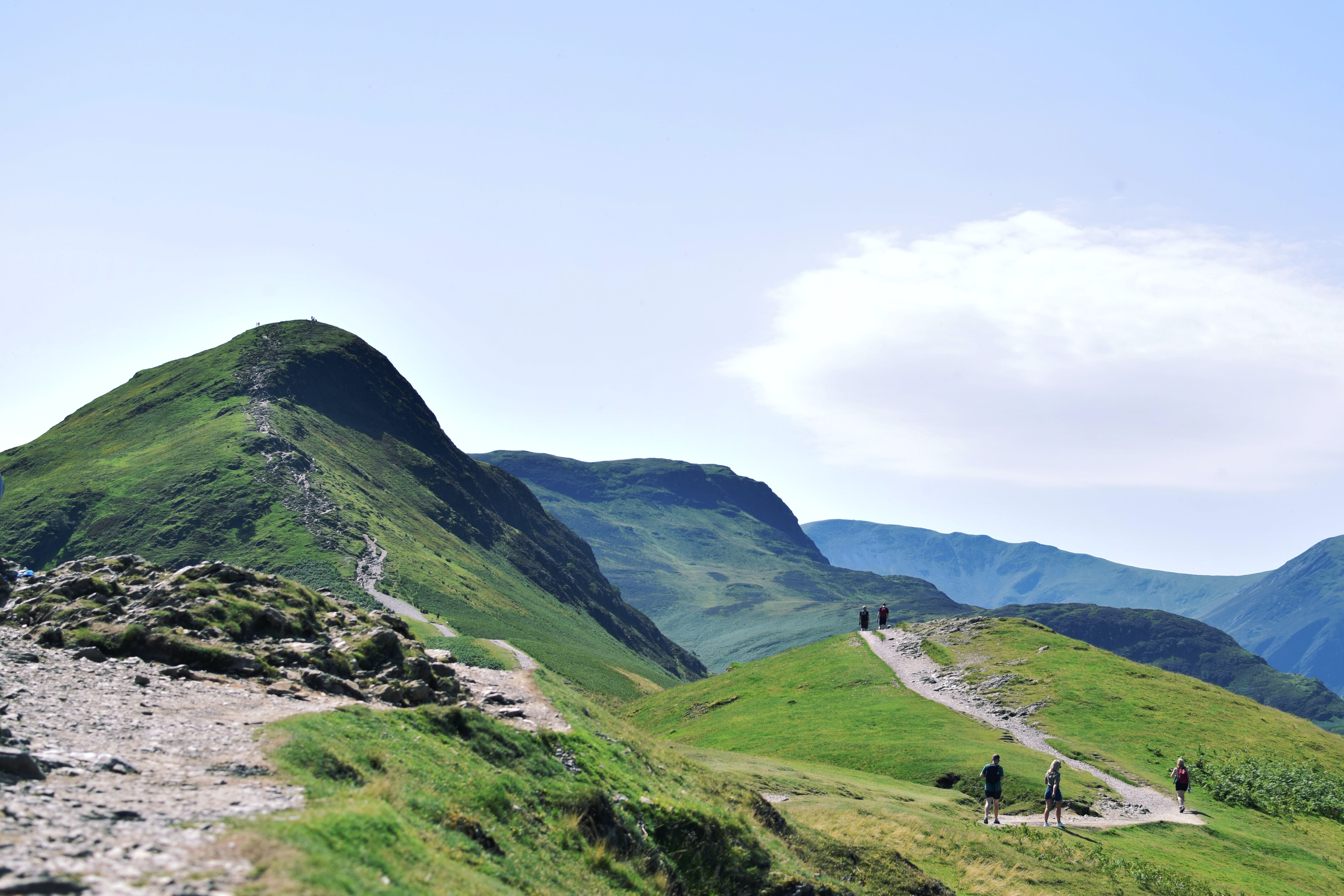
- 10 mins read
The best events in every UK National Park
The UK's National Parks provide incredible outdoor playgrounds - these are the runs, bike rides and swims to help you make the most of these epic spaces.
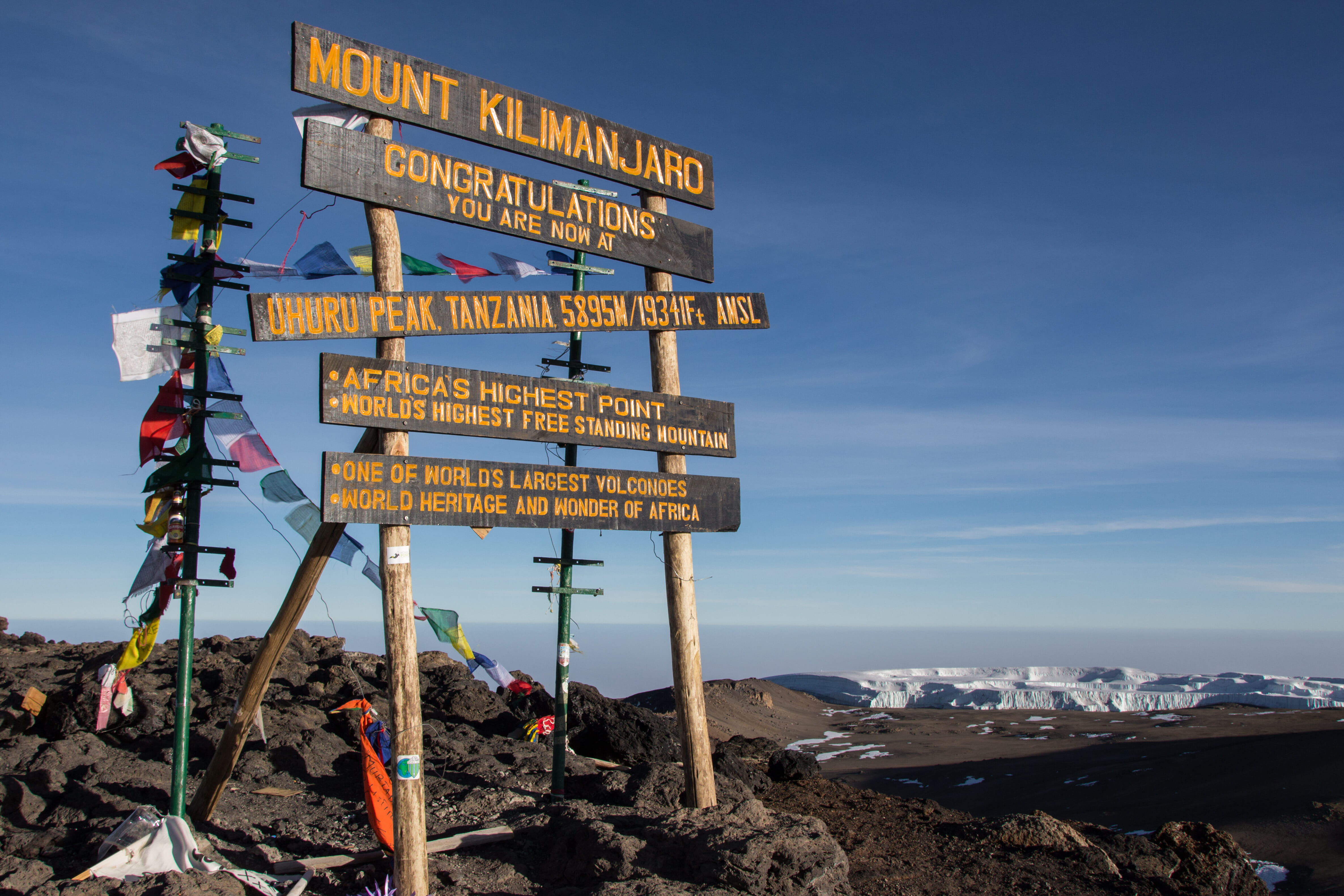
- 5 mins read
What is the best route to climb Kilimanjaro?
The route you pick for your Kilimanjaro trek will help to determine the experience that you enjoy, from comfortable dorms to wild camping!
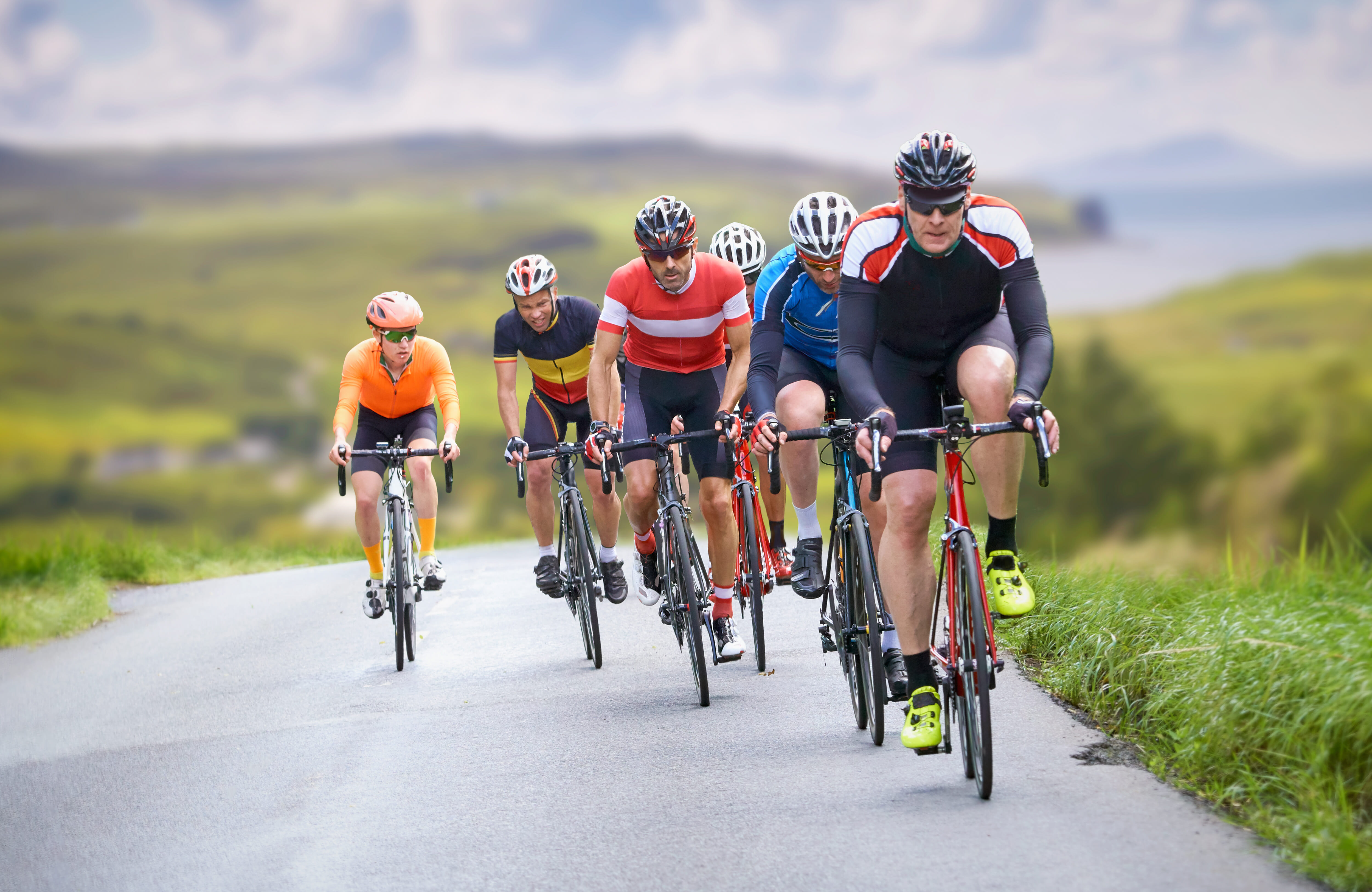
- 5 mins read
Best cycling events in the UK
Inspired by the Tour de France? You don't need to ride the Alpe d'Huez to enjoy an epic peloton experience - these British bike rides are the real deal.
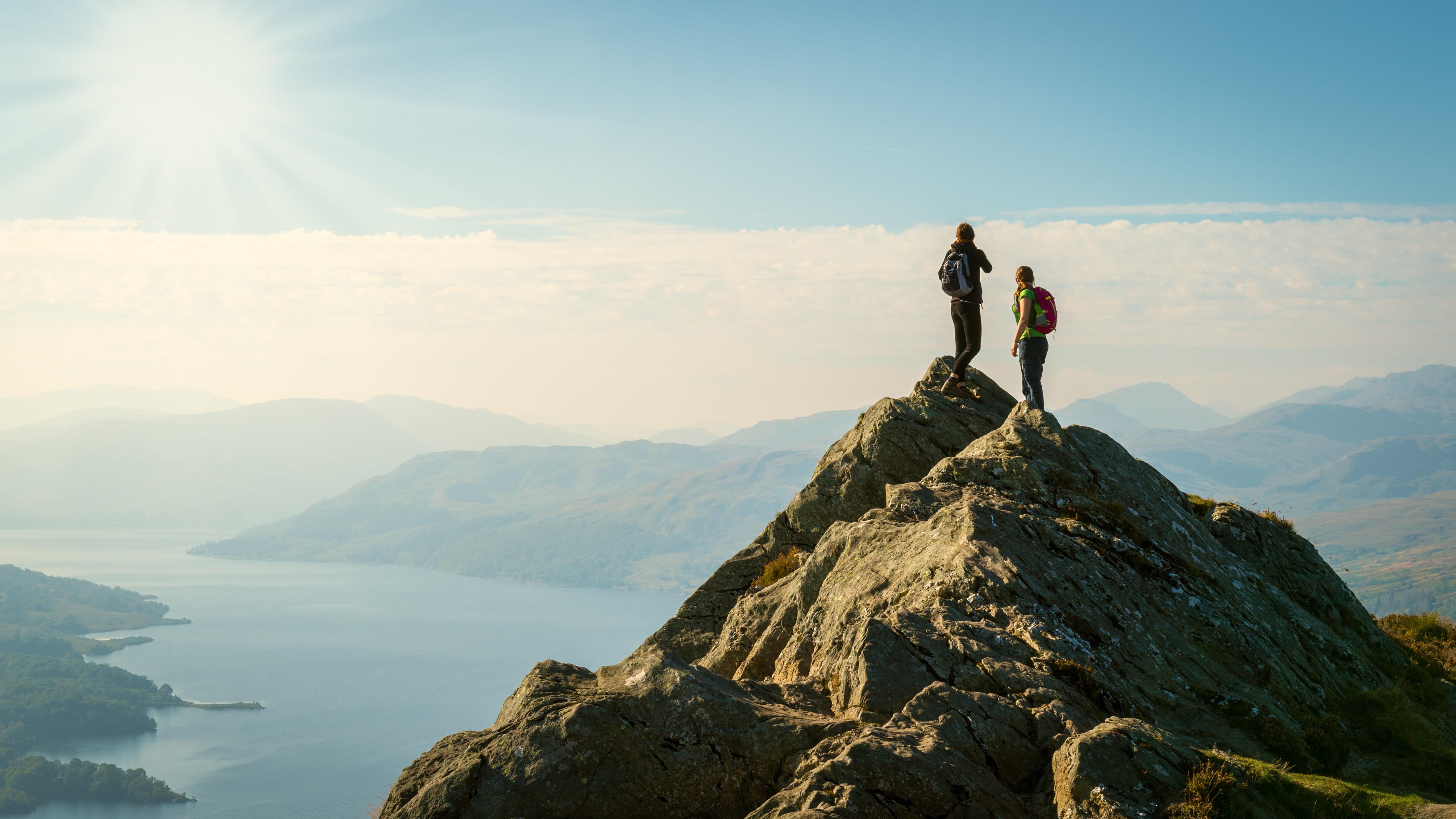
- 5 mins read
4 epic hikes to challenge yourself in spring and summer
Make the most of the sunshine with these hikes atop the mountains and coastlines of the UK, all supporting fantastic charity causes.
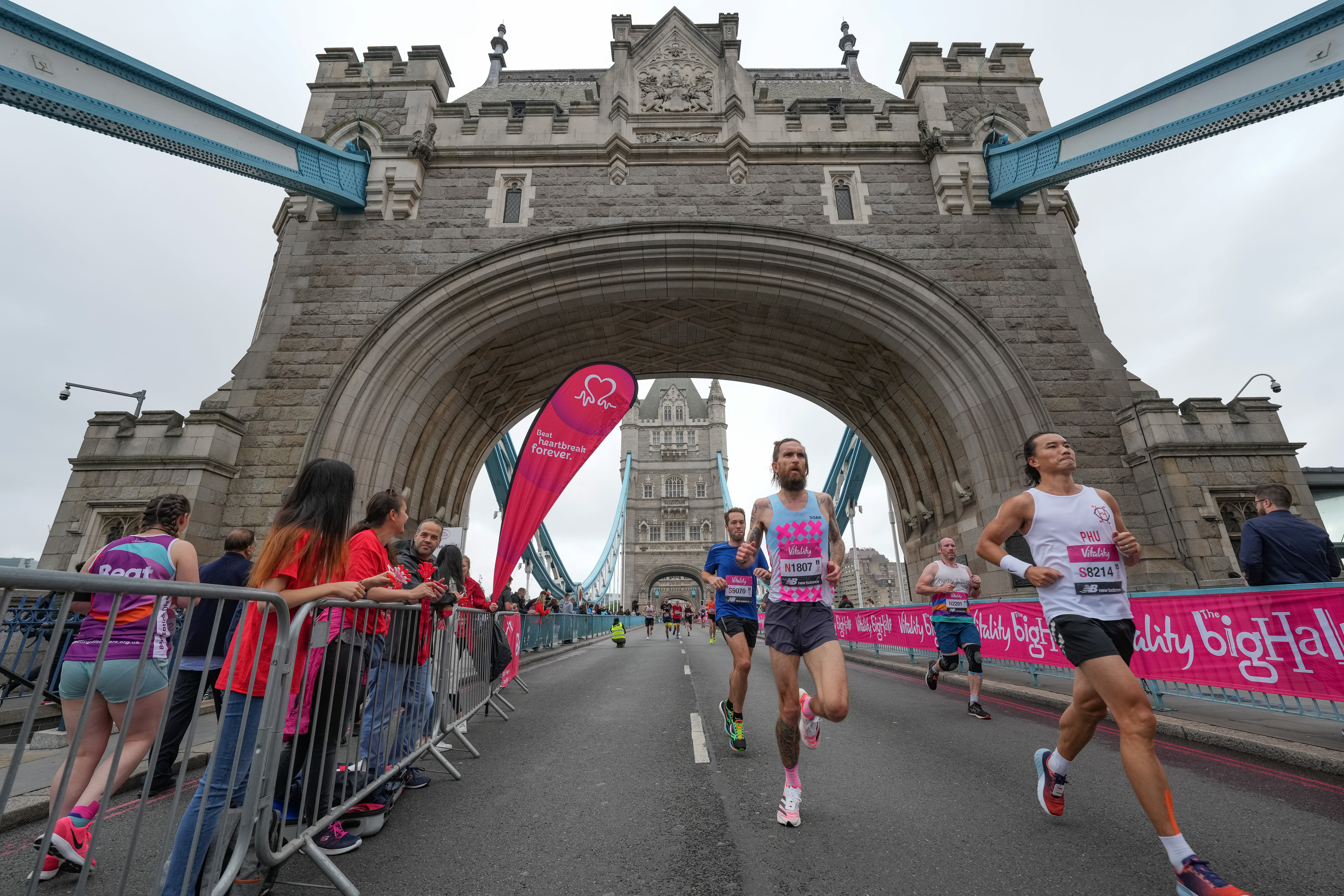
- 10 mins read
Aim for a new half marathon PB
Looking for a new challenge? Taking on your fastest ever half marathon could be exactly the motivation you need to get out there and be more active outdoors!
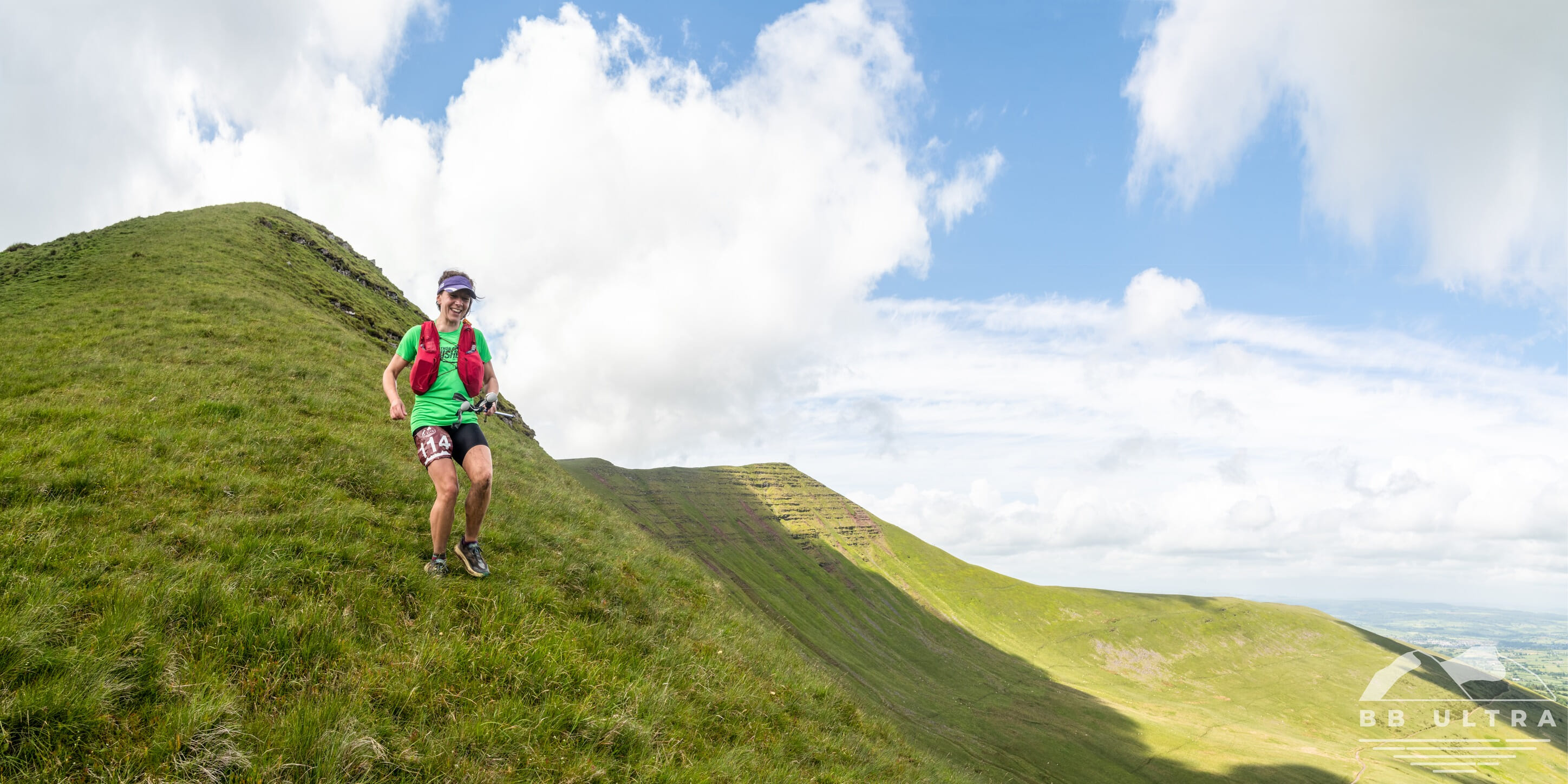
- 10 mins read
The best runs that you've never heard of
To celebrate Global Running Day, we're rounding the best unsung marathons, half marathons and more in the UK!
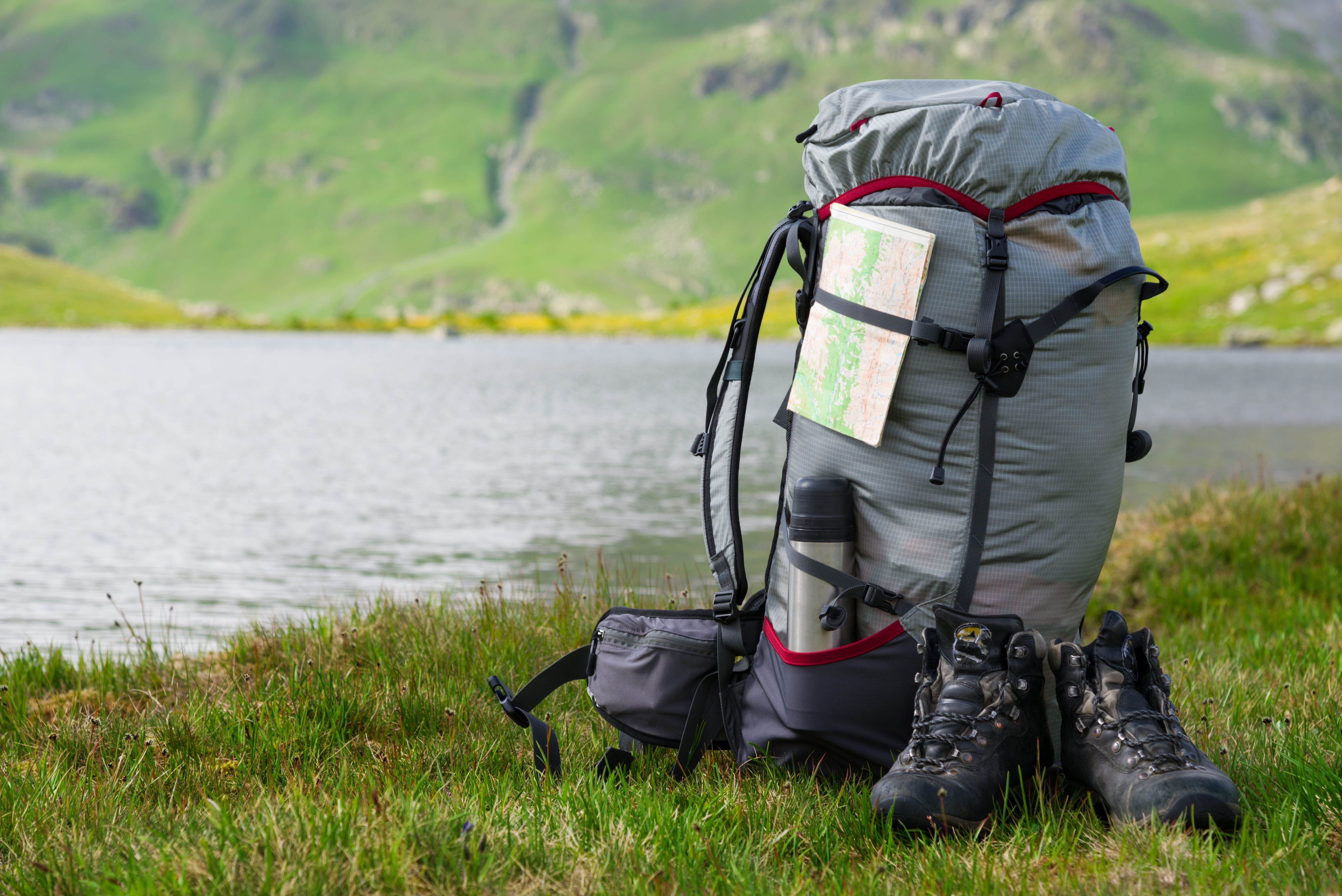
- 10 mins read
8 essentials you need in your hiking bag
Whether you're heading into the great outdoors for a few hours or a few days, these are the essentials you need to guarantee staying safe and having the best experience.
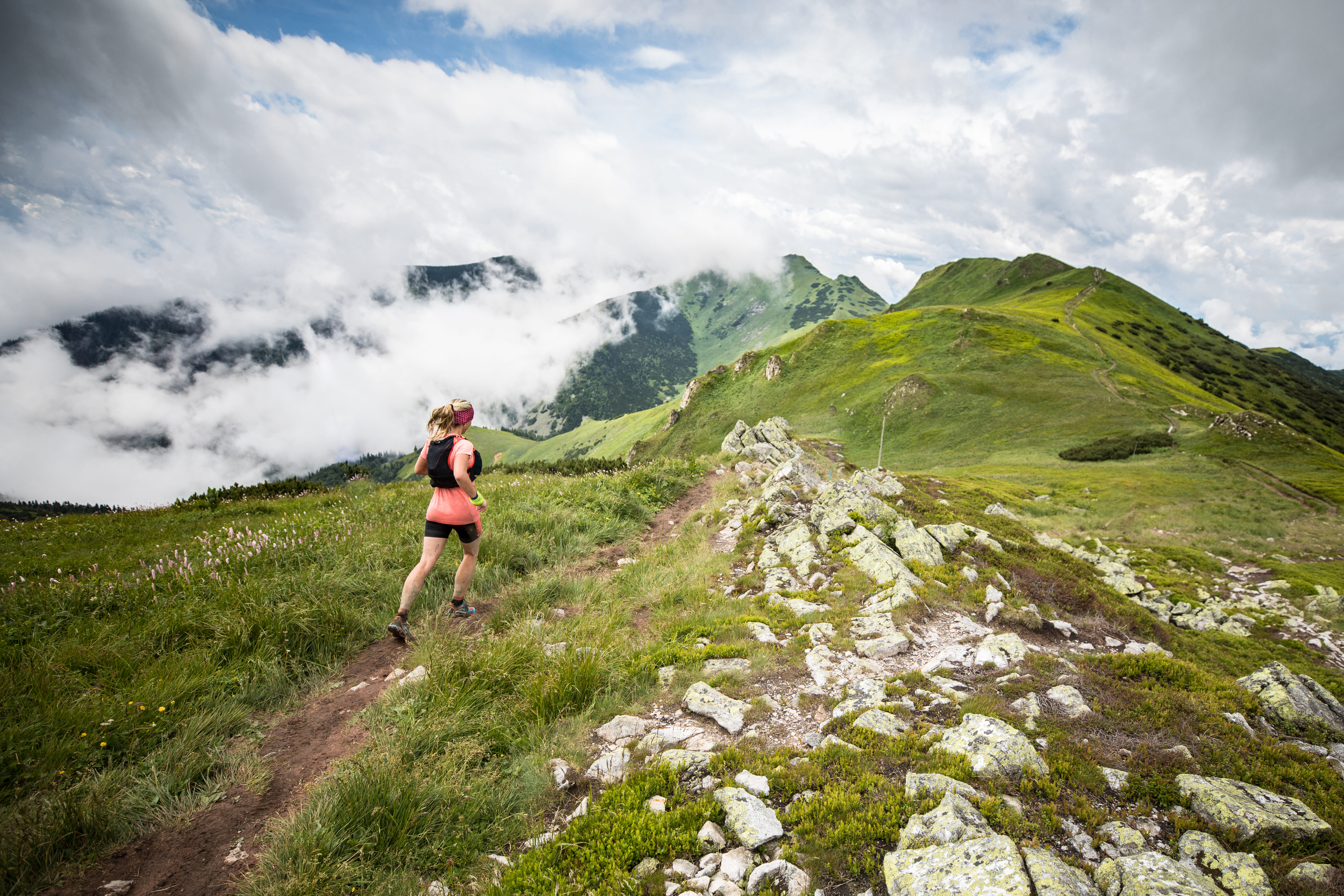
- 10 mins read
The best trail runs this summer
Head off-road and into a world of epic trail running this summer, exploring the mountains, forests and coastlines of the UK.
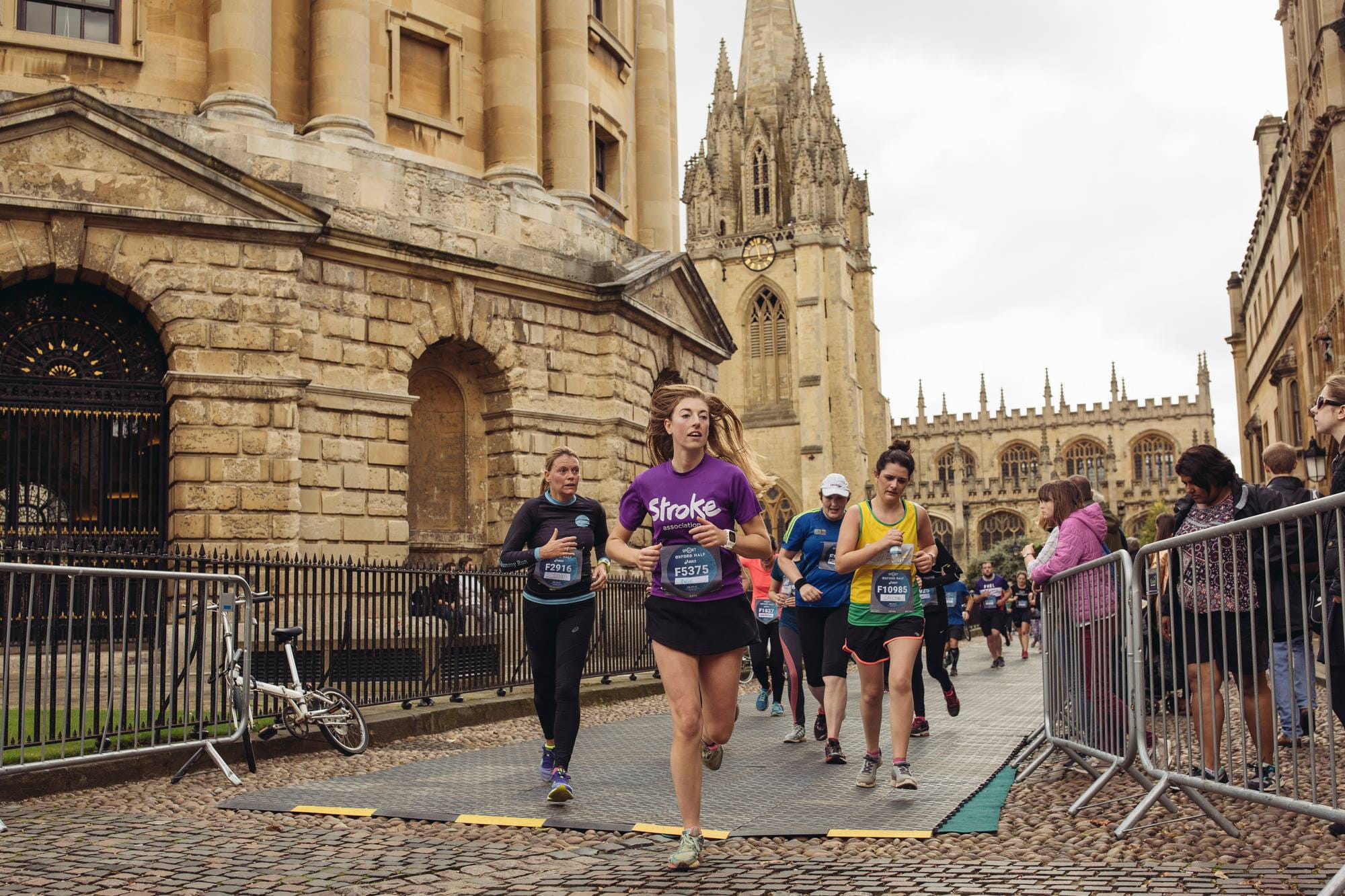
- 5 mins read
Best autumn half marathons
Enjoy the sensational atmospheres and fast courses at these half marathon races, from the world's biggest half to the UK's fastest half marathon.
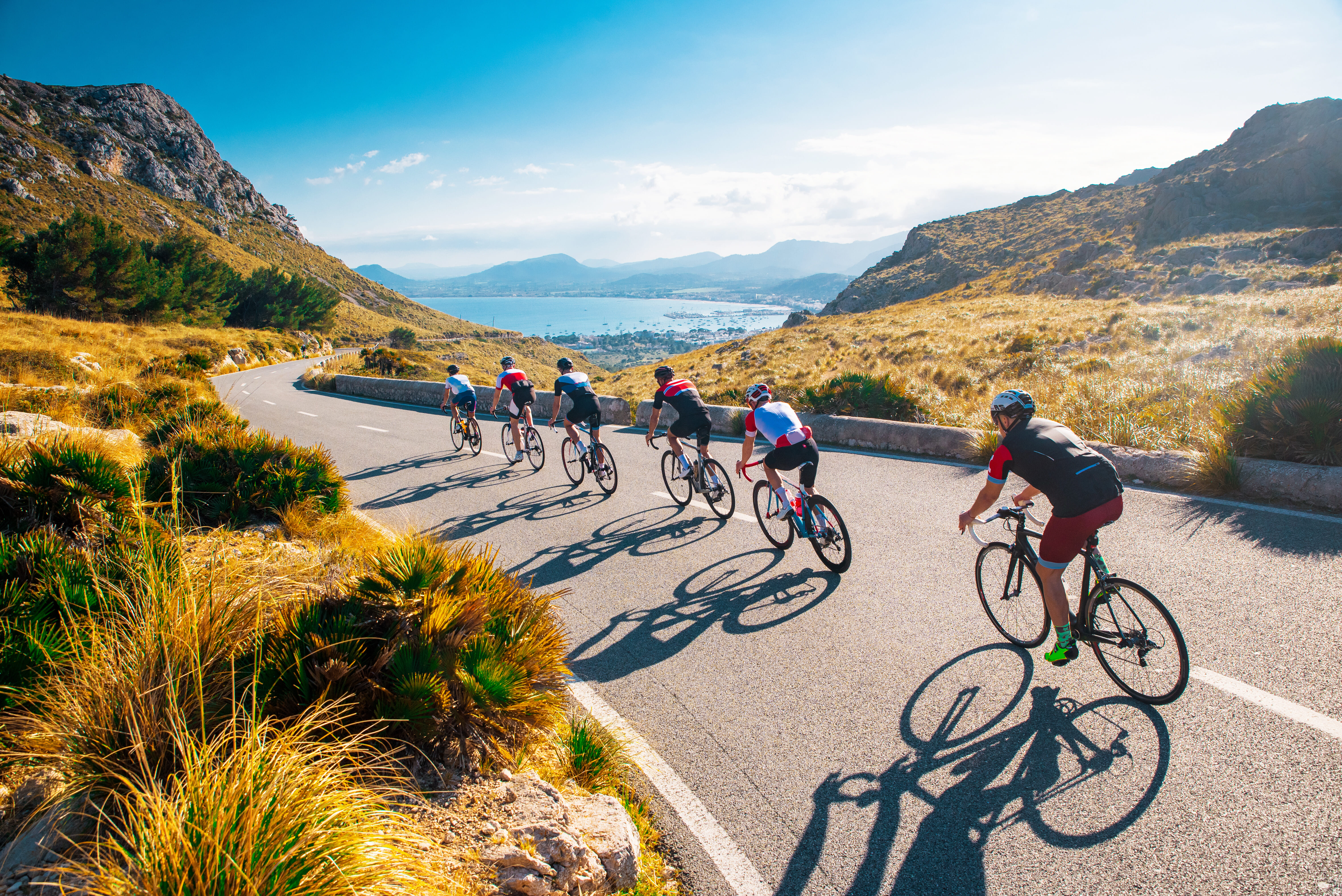
- 5 mins read
Top 5 adventure races in the UK
Epic adventure activities, crammed into a race through wild landscapes - what's not to love?
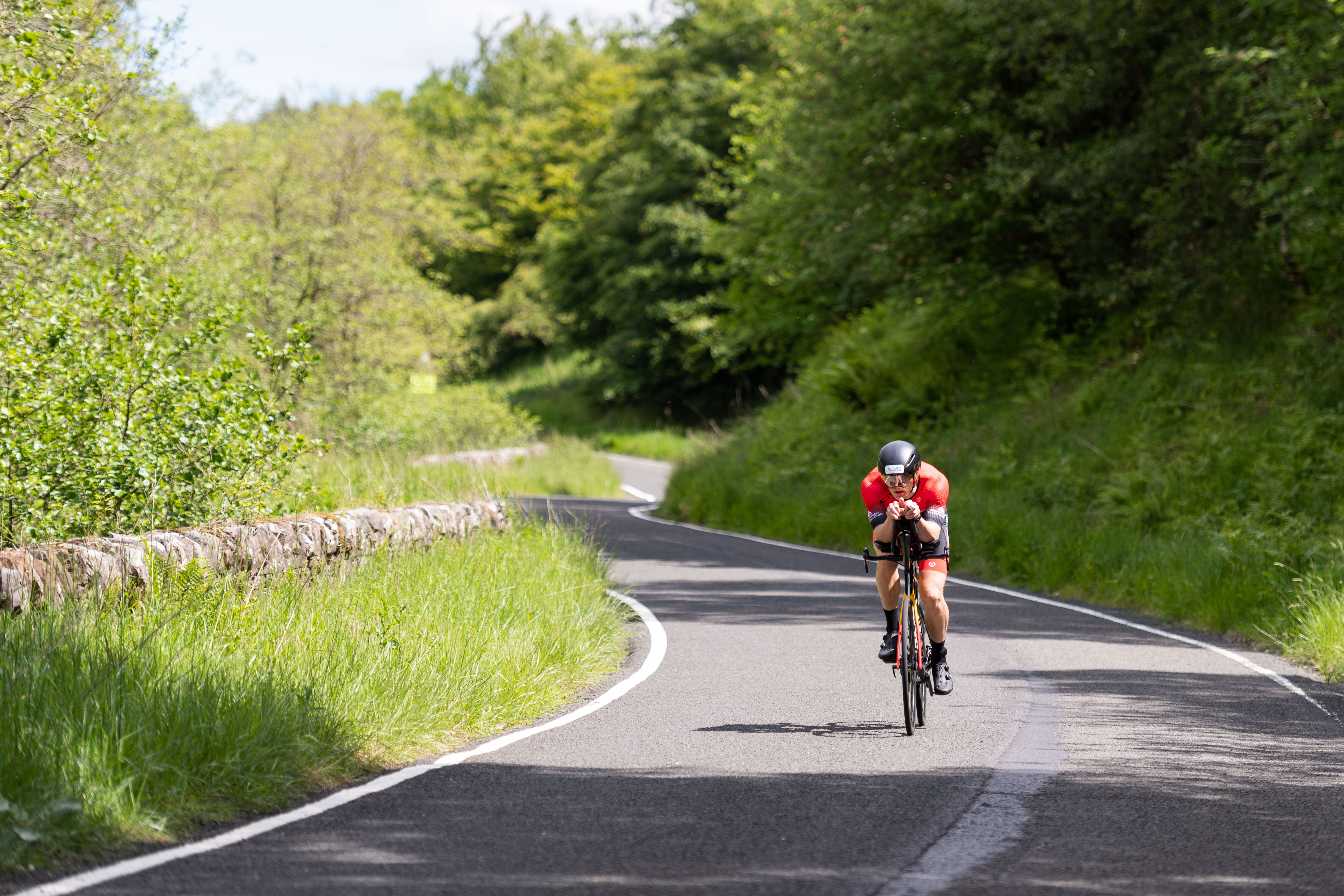
- 15 mins read
7 things we learned from a half Ironman
Humbling and exhilarating in equal measures, a half Ironman triathlon is an unforgettable experience - following these hard-learned tips will make sure that's for all the right reasons.
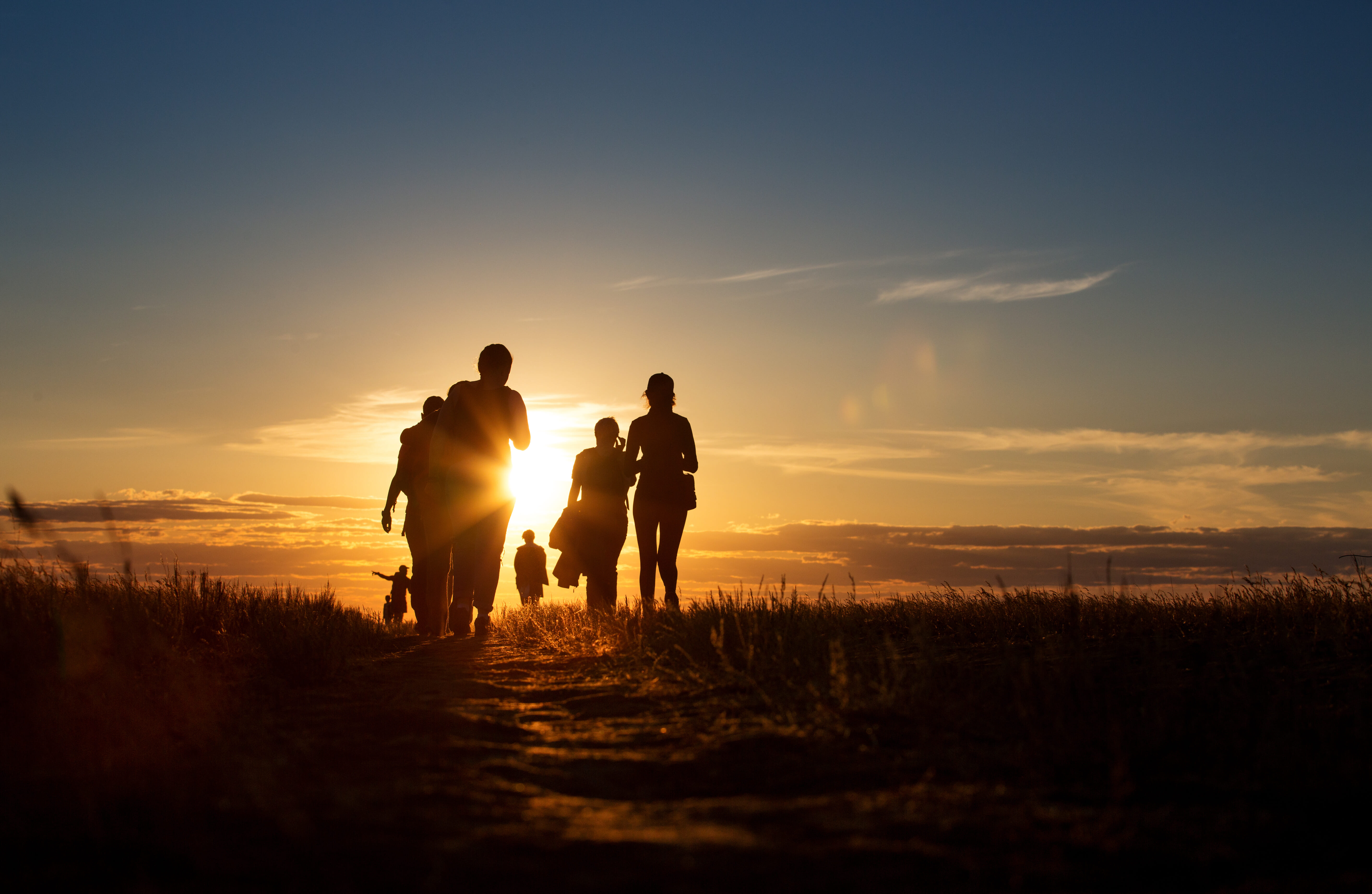
- 12 mins read
5 ways being active outdoors together can help your team's mental health
This is why an active outdoors challenge is the tonic your team needs to banish workplace anxiety and build a more cohesive culture.
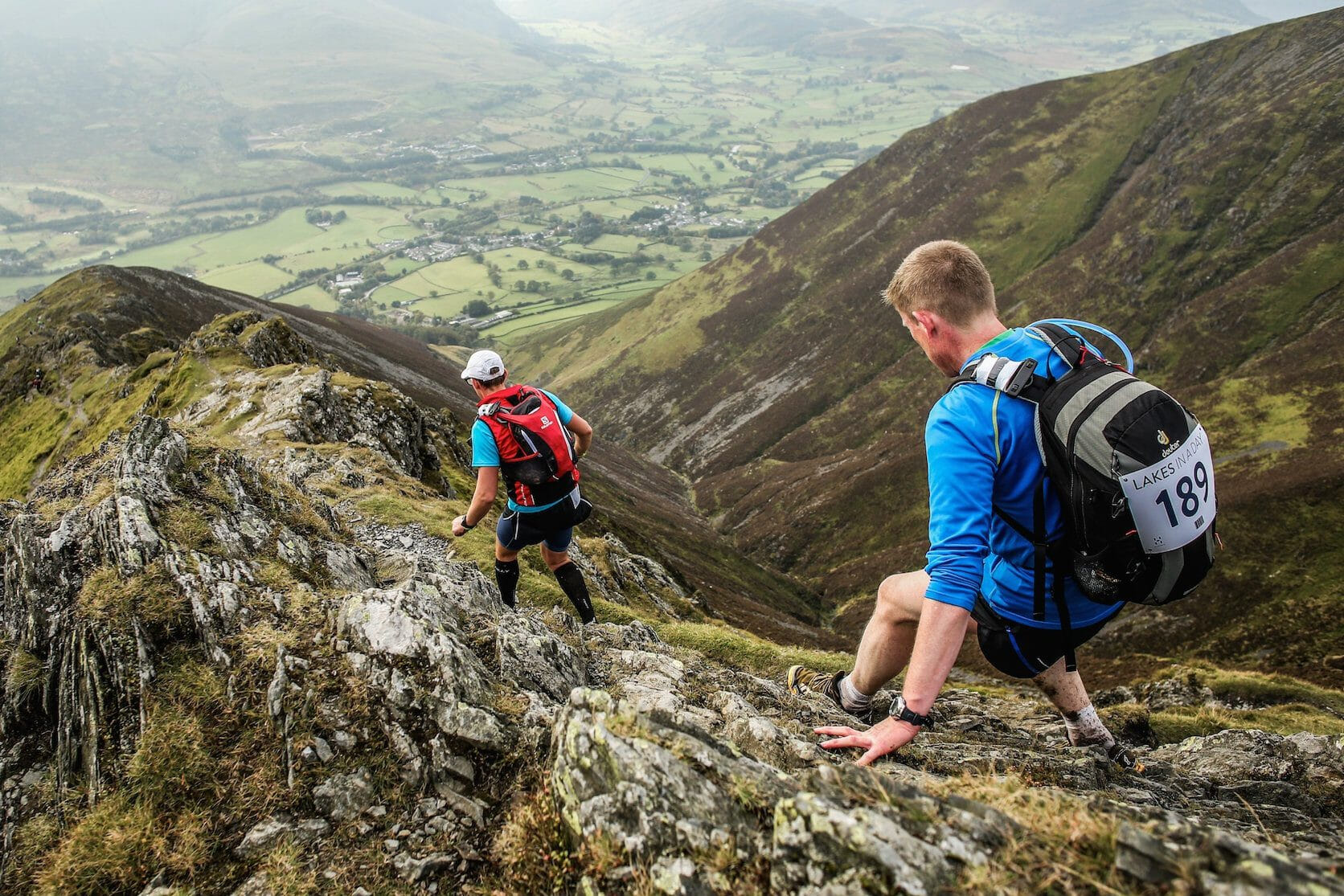
- 8 mins read
10 best ultra marathons in the UK
Take on an epic endurance challenge with one of the most popular ultra runs in the UK, from traditional fell runs to the UTMB World Series!
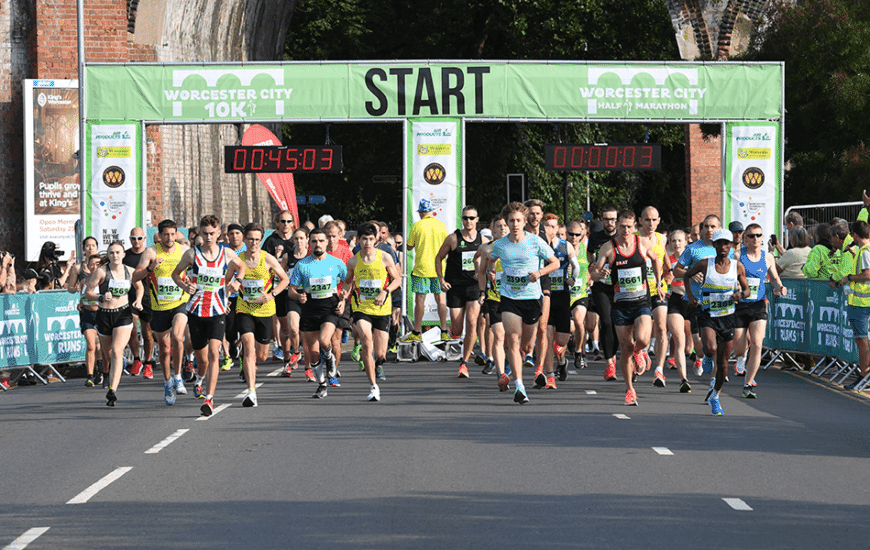
- 10 mins read
What is the best 10K near me?
6.2-miles is the perfect distance for beginner runners and experienced athletes alike, with hundreds of runs around the UK - find the best 10K in your local region right here.
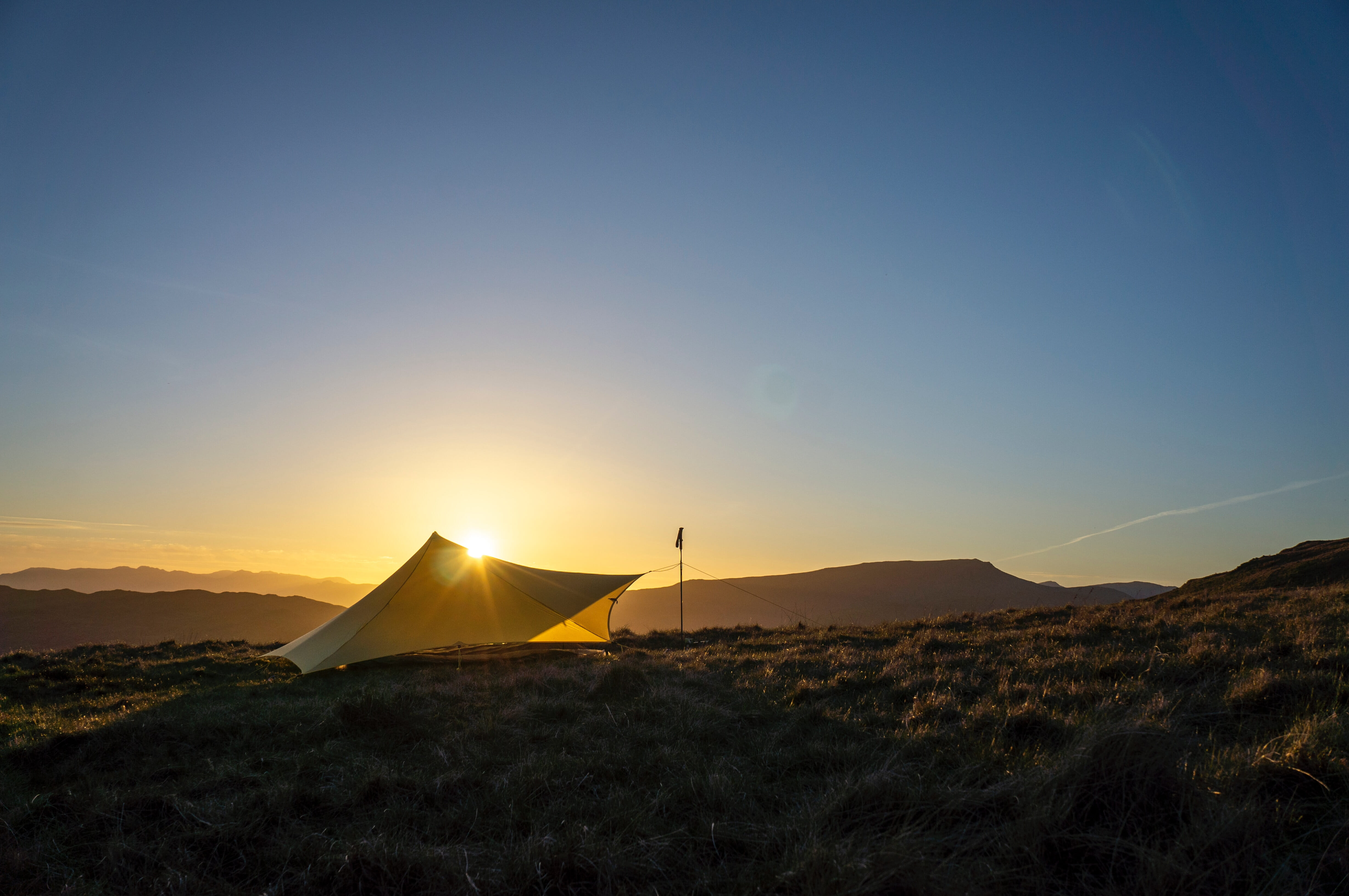
- 5 mins read
5 everyday adventures to spend more time outdoors
These micro doses of outdoor adventure are enough to sustain your wanderlust between bigger trips to the great outdoors!
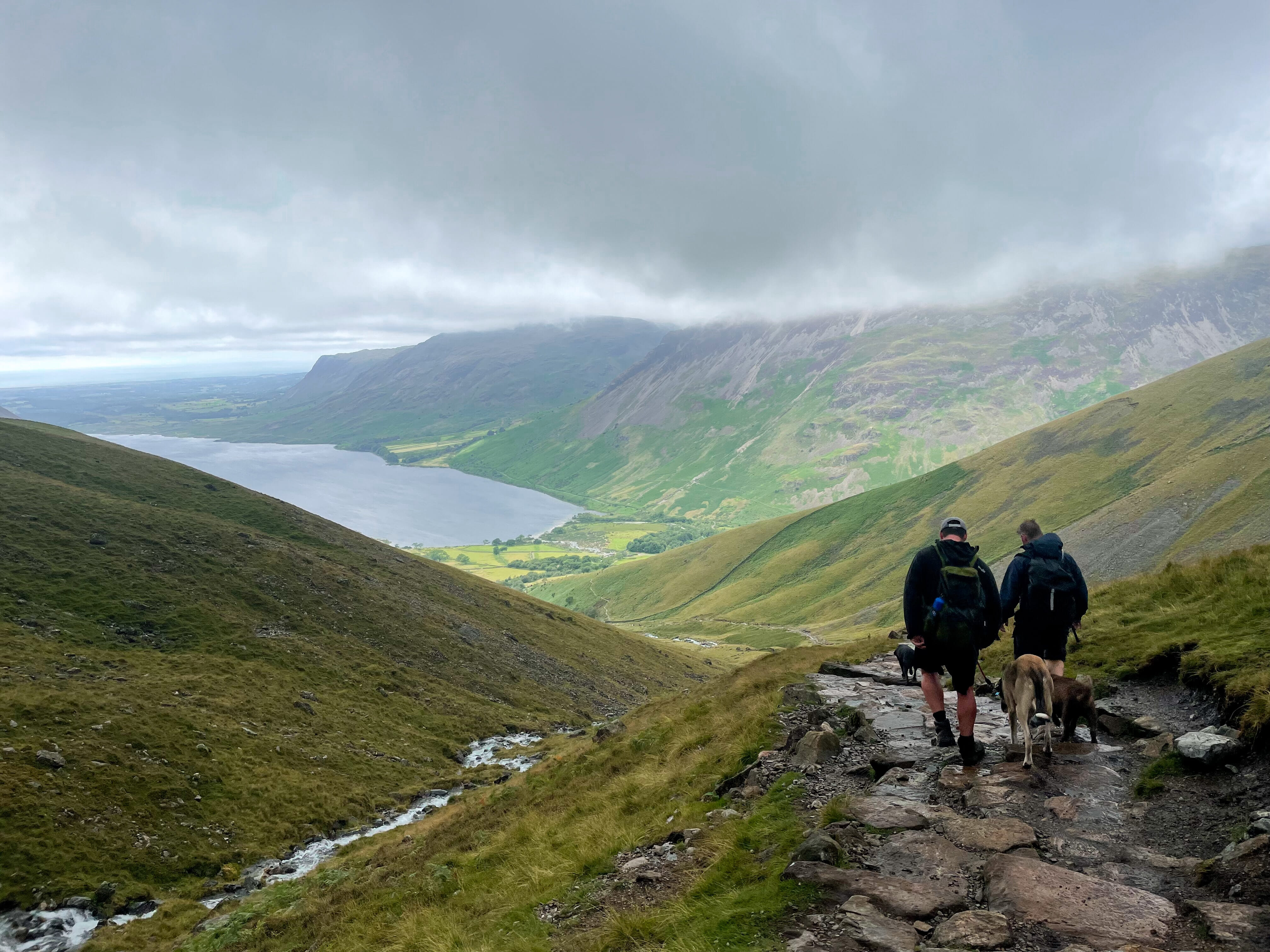
- 15 mins read
Your guide to the National Three Peaks Challenge
Take on this iconic challenge in 2023 and make unforgettable memories on the UK's highest mountains!
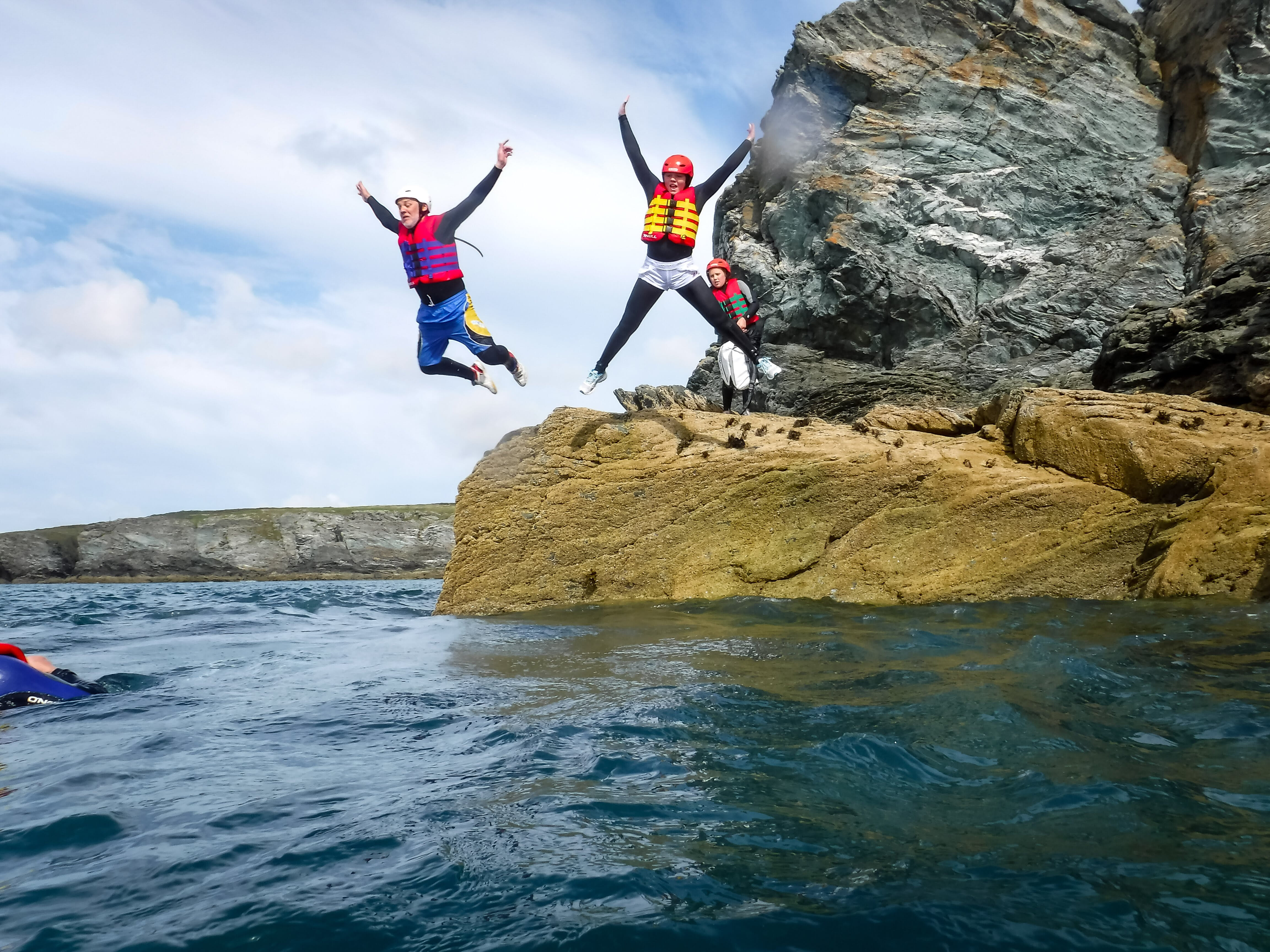
- 5 mins read
3 family adventures this summer
Get the whole family active outdoors with these epic adventures, ranging from mountain hikes to week-long activity holidays!

- 5 mins read
10 best autumn marathons
Looking for a fresh challenge this year? Sign up to an end-of-season marathon to focus your training through the summer and finish the year on a high!
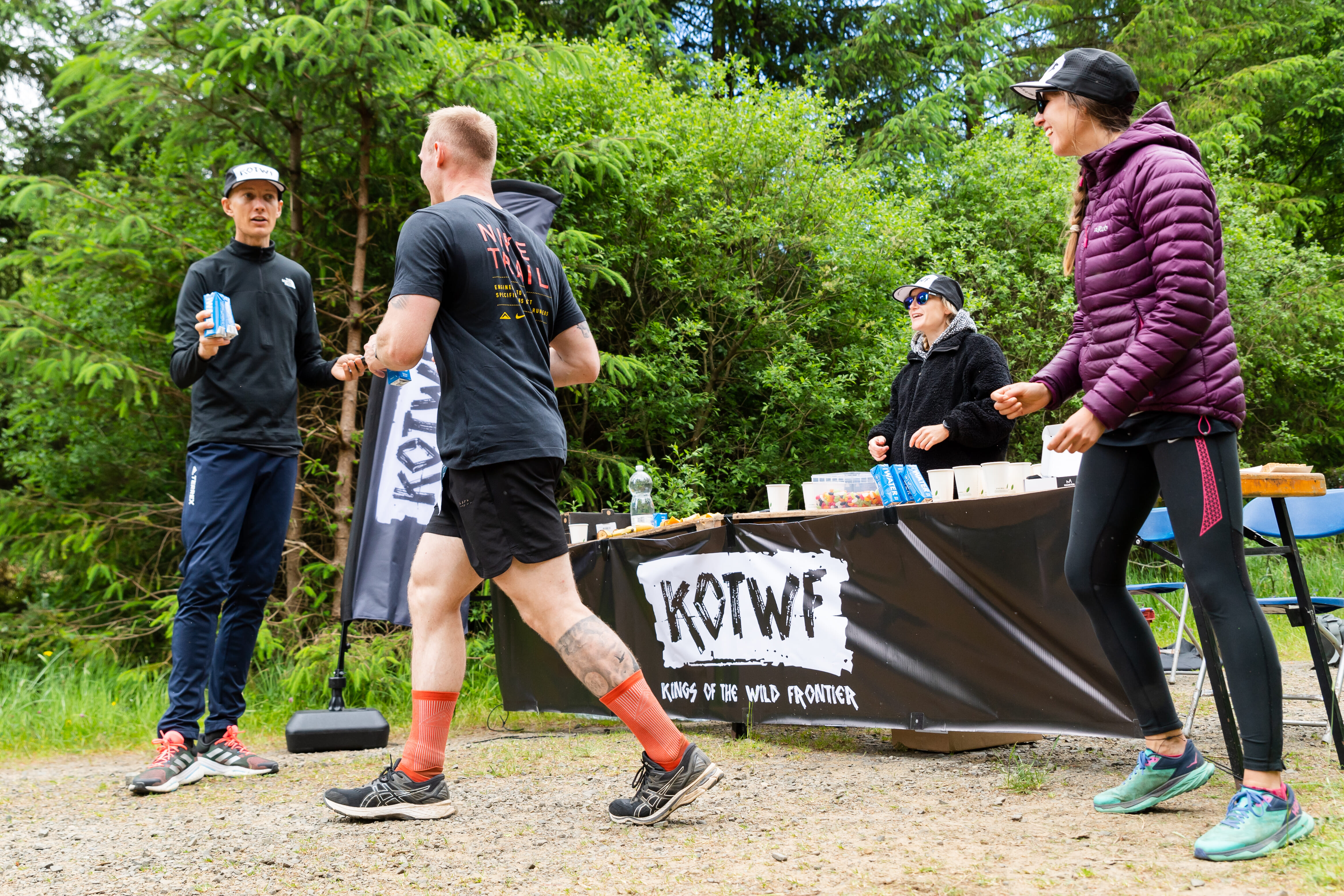
- 15 mins read
5 ways for events to be more sustainable
Wooden medals, virtual medals and no medals at all - what does an eco-friendly event look like?
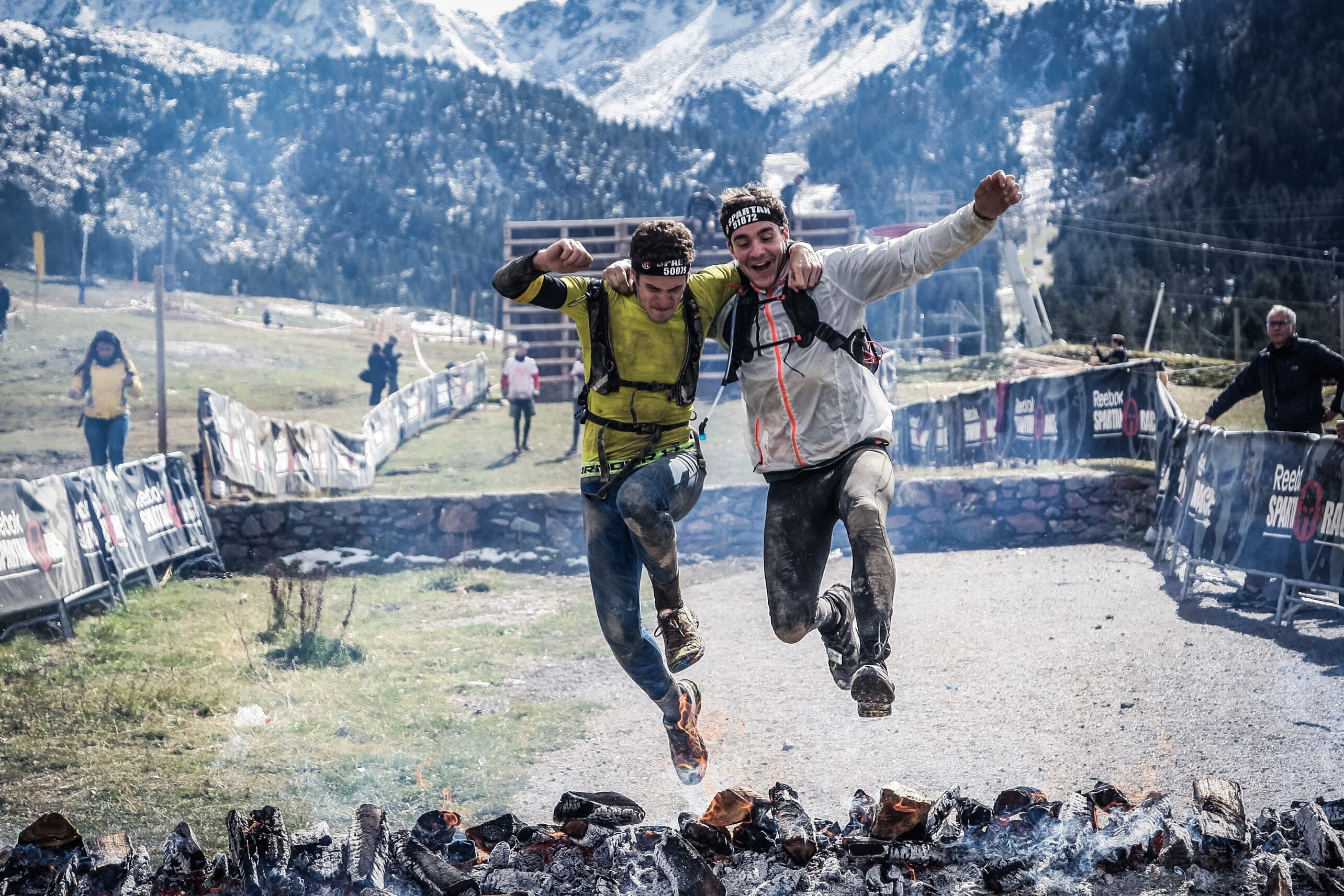
- 5 mins read
3 tips for training for an obstacle race
How do you prepare for a race designed to be unpredictable and, frankly, chaotic? By keeping your training varied and avoiding injury like the plague!
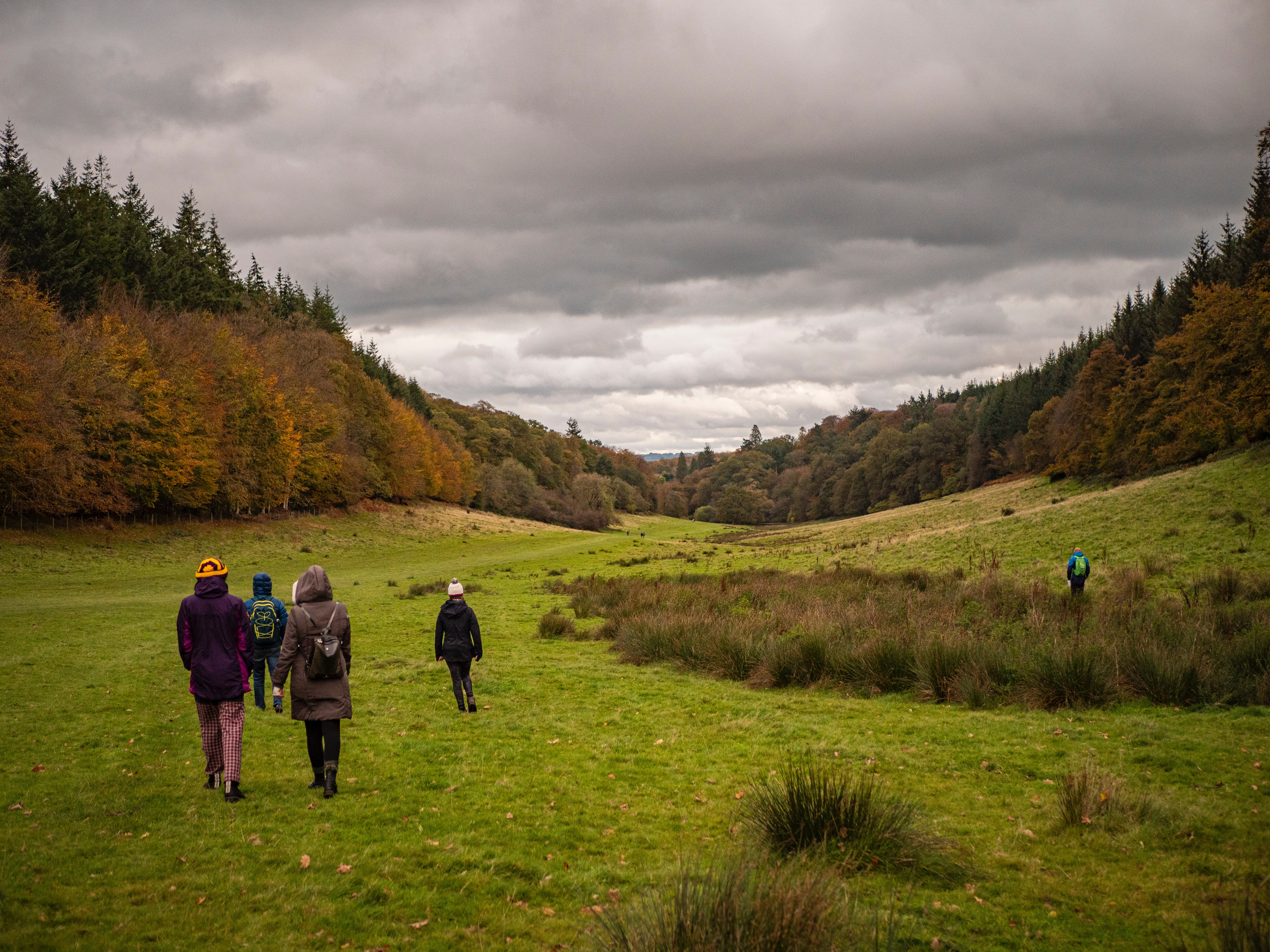
- 5 mins read
3 ways to spend more time outdoors
Need some extra motivation to get lace up those boots and get out there? It happens to all of us - but overcoming that inertia and spending time outdoors is the best possible decision you can make!
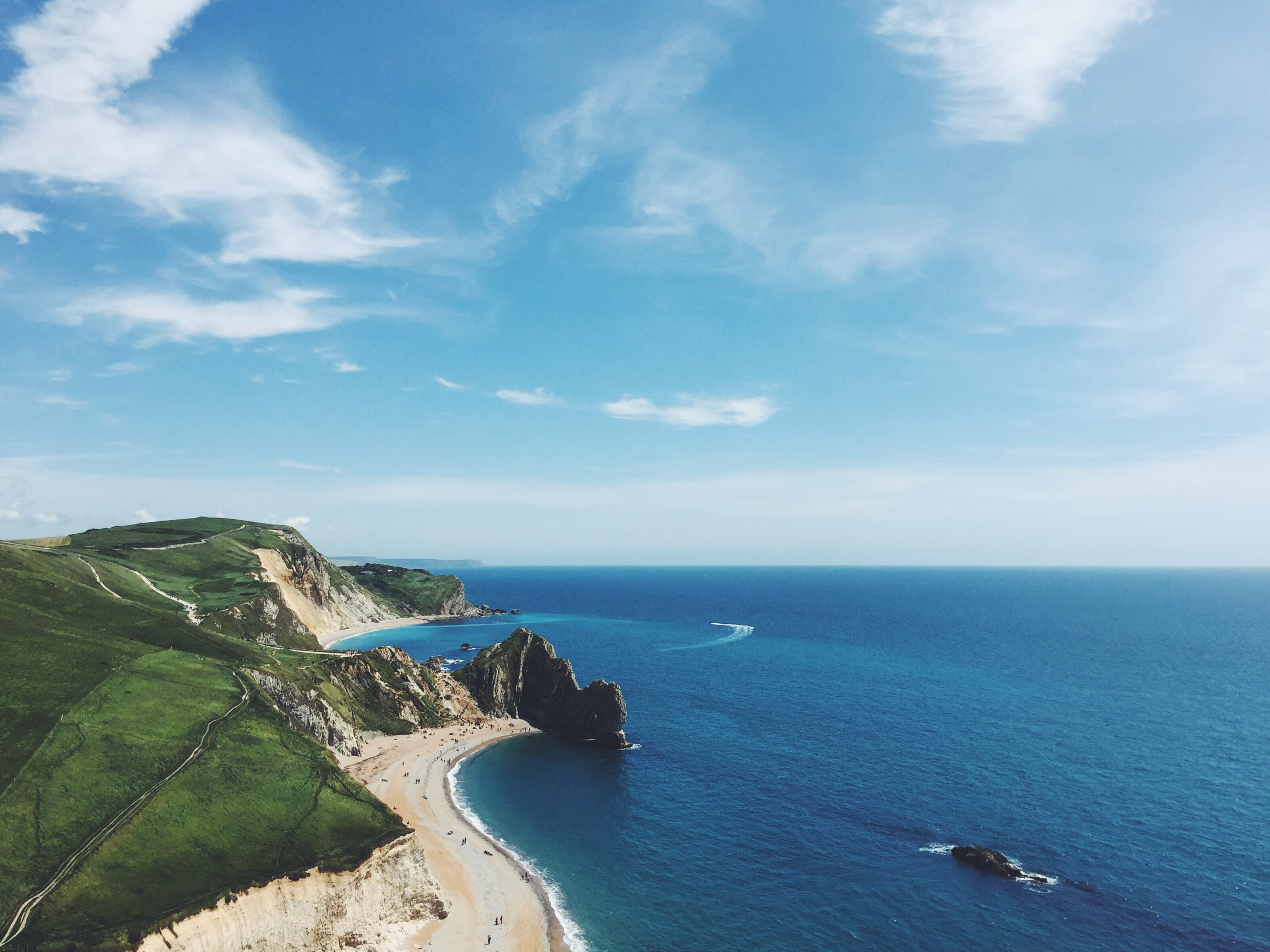
- 8 mins read
7 incredible coastal walks in the UK
Discover some of the best coastal walks in the UK, from the wild shores of Arran to the rolling hills of the South Downs.

- 5 mins read
4 reasons why the Hackney Half is one of London's most popular events
Fusing fast running with an electric atmosphere, the Hackney Half celebrates the very best of East London.
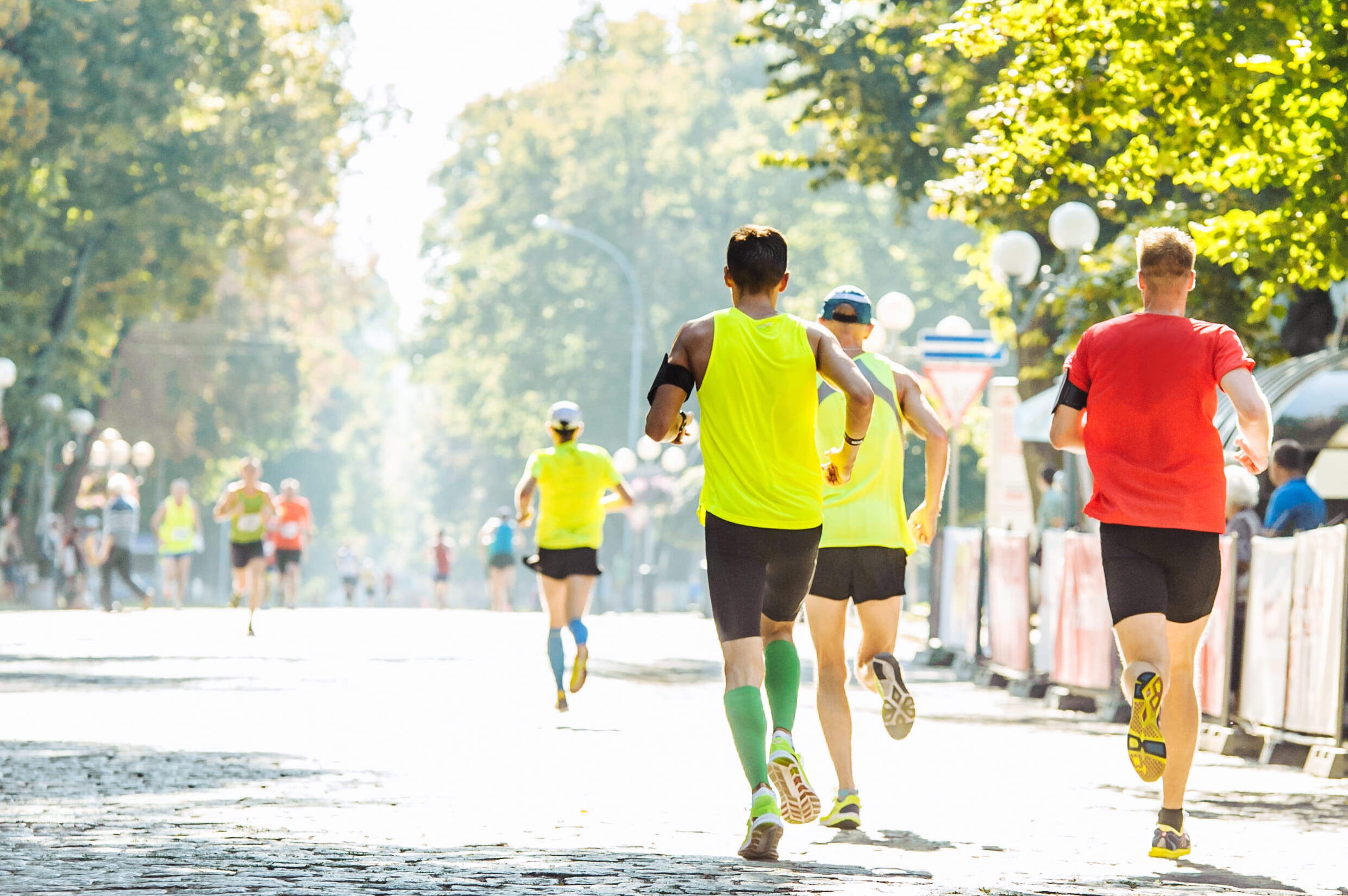
- 12 mins read
What is the best marathon for running a PB?
Chasing a fast marathon time is as much about picking the right course as training hard! Check out our selection of the fastest and flattest marathons in the UK.
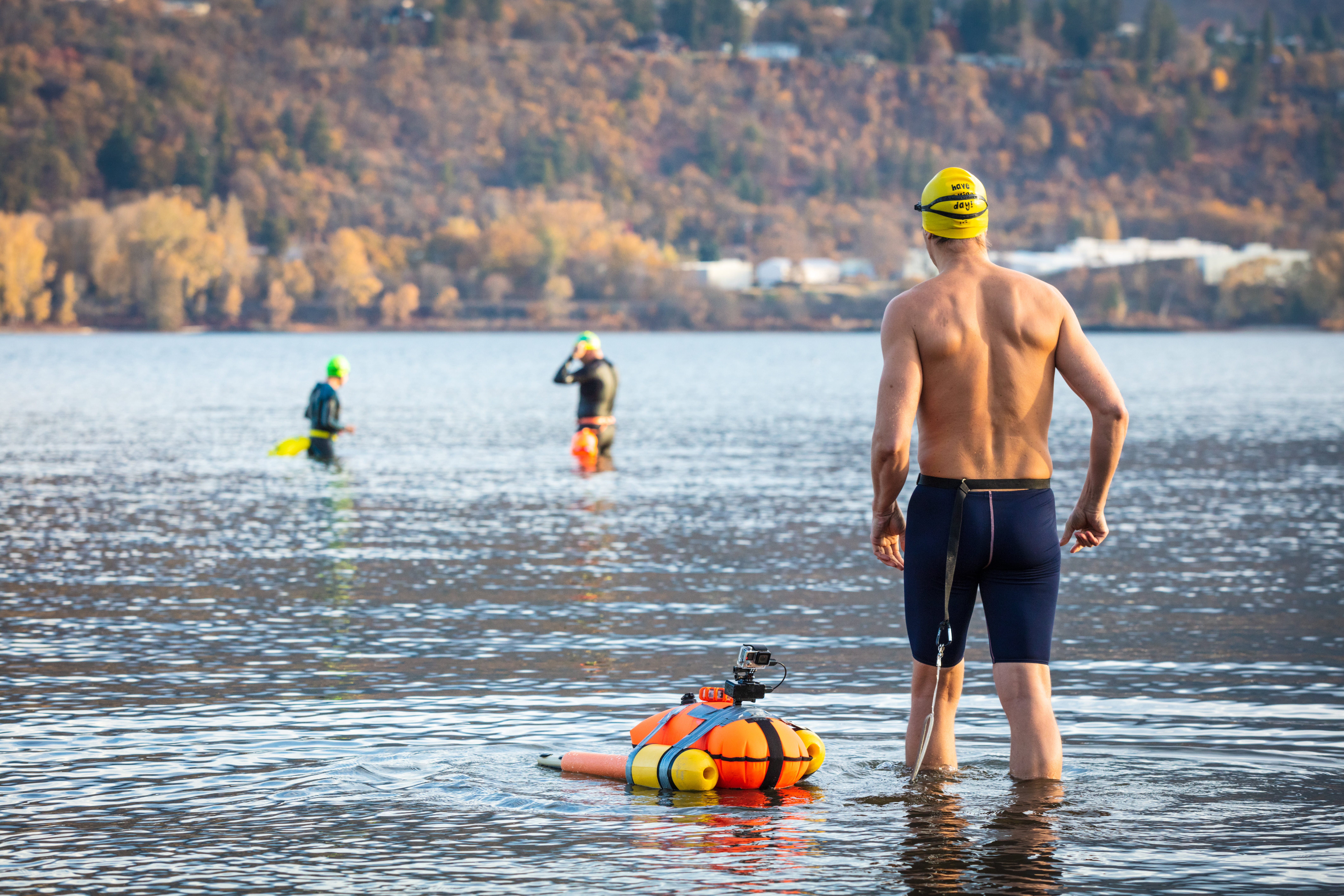
- 10 mins read
3 reasons to start open water swimming
From cold water therapy to time spent in the great outdoors, open water swimming is your express ticket to feeling happier and healthier this year.
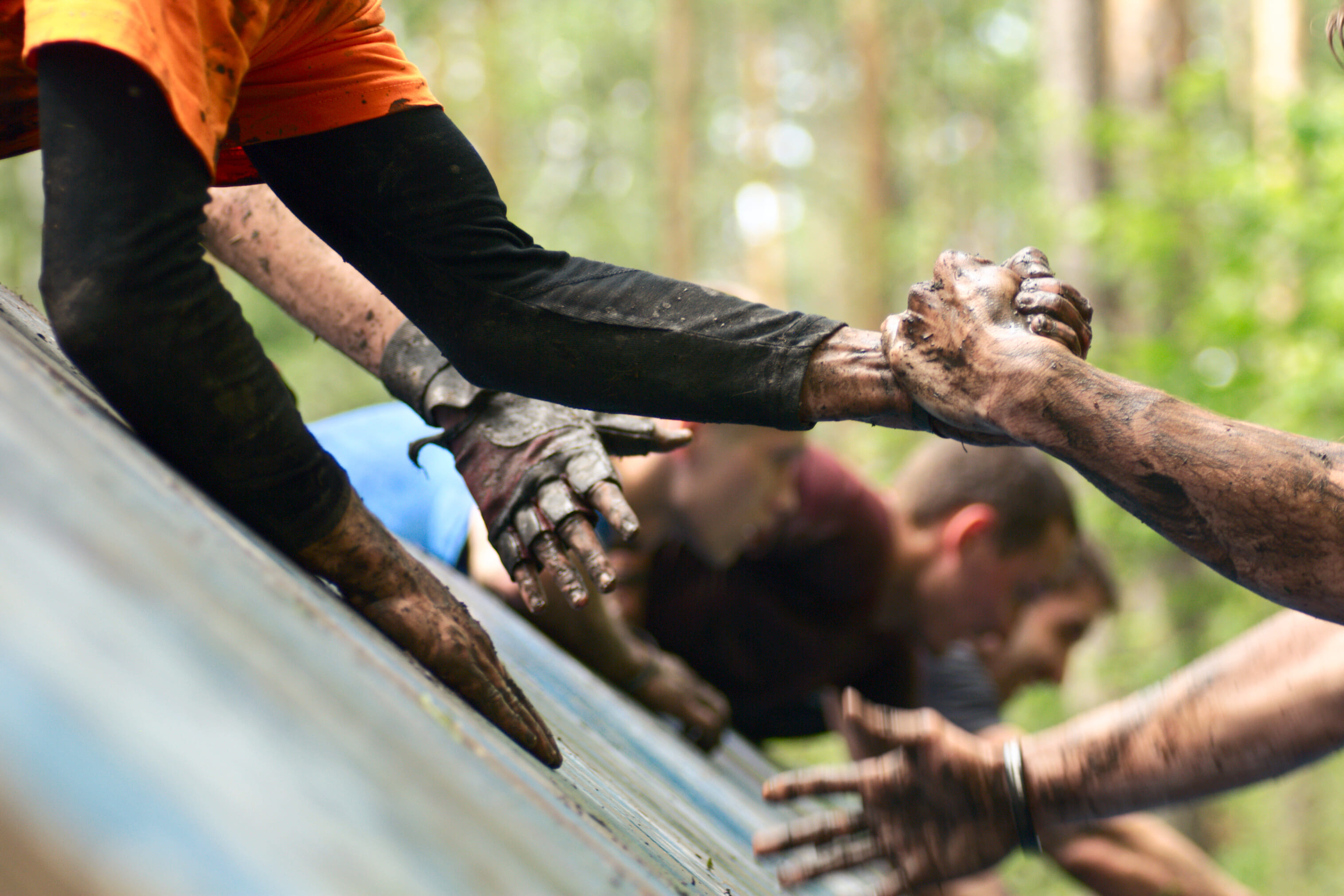
- 5 mins read
3 reasons to run an obstacle course race for charity
Elevate your race day experience by raising money for a great cause, connecting with other people and enjoying a discounted entry fee!
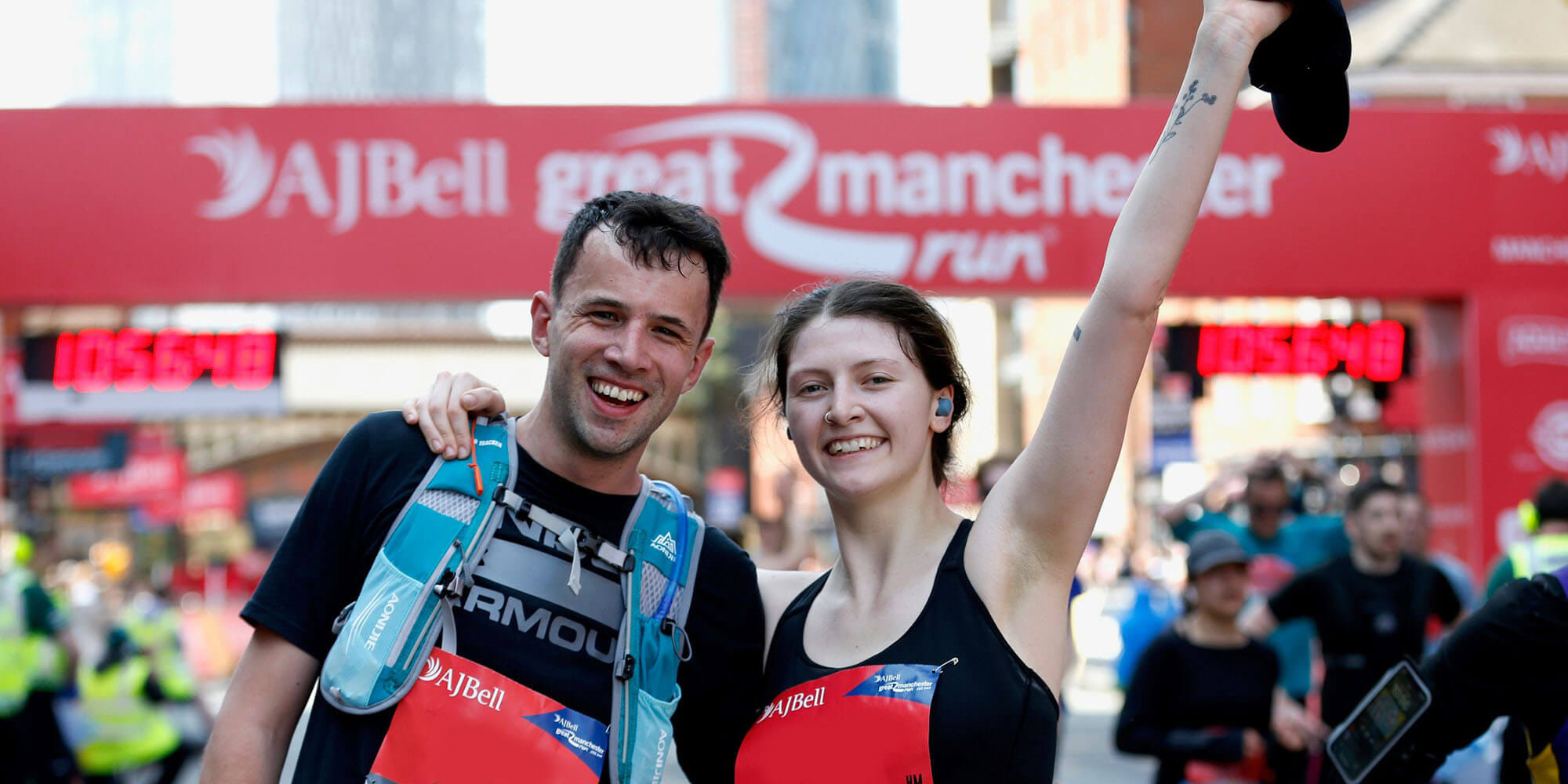
- 10 mins read
Why is the Great Manchester Run the biggest 10K in Europe?
With thousands of runners taking part each year, this headline race is Manchester's original and greatest running event - here's why you should be there in 2024!
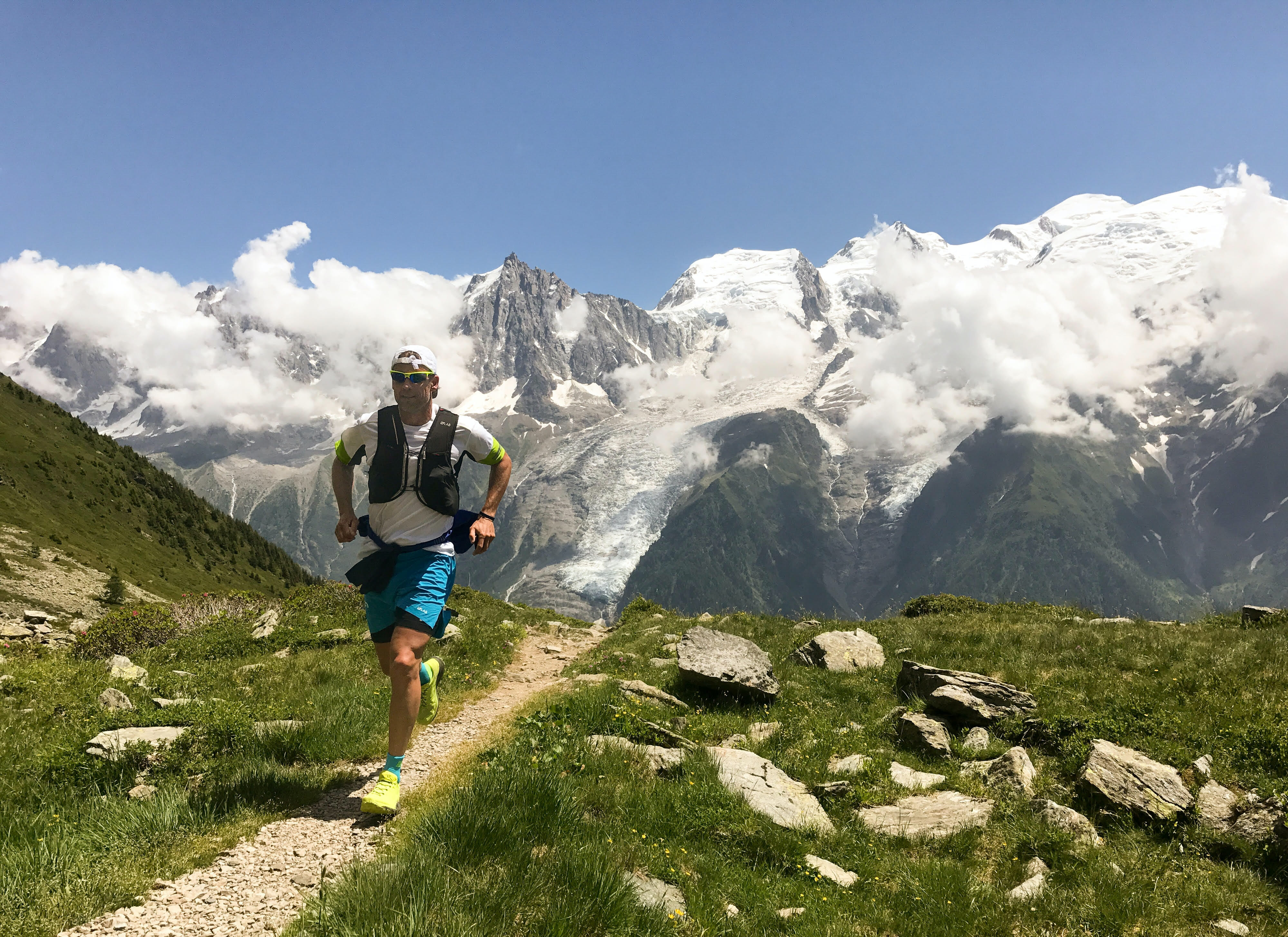
- 5 mins read
5 things you need to know before your first ultra
Ultra marathons are some of the greatest tests of endurance on the planet and yield unforgettable experiences - if you're well prepared.
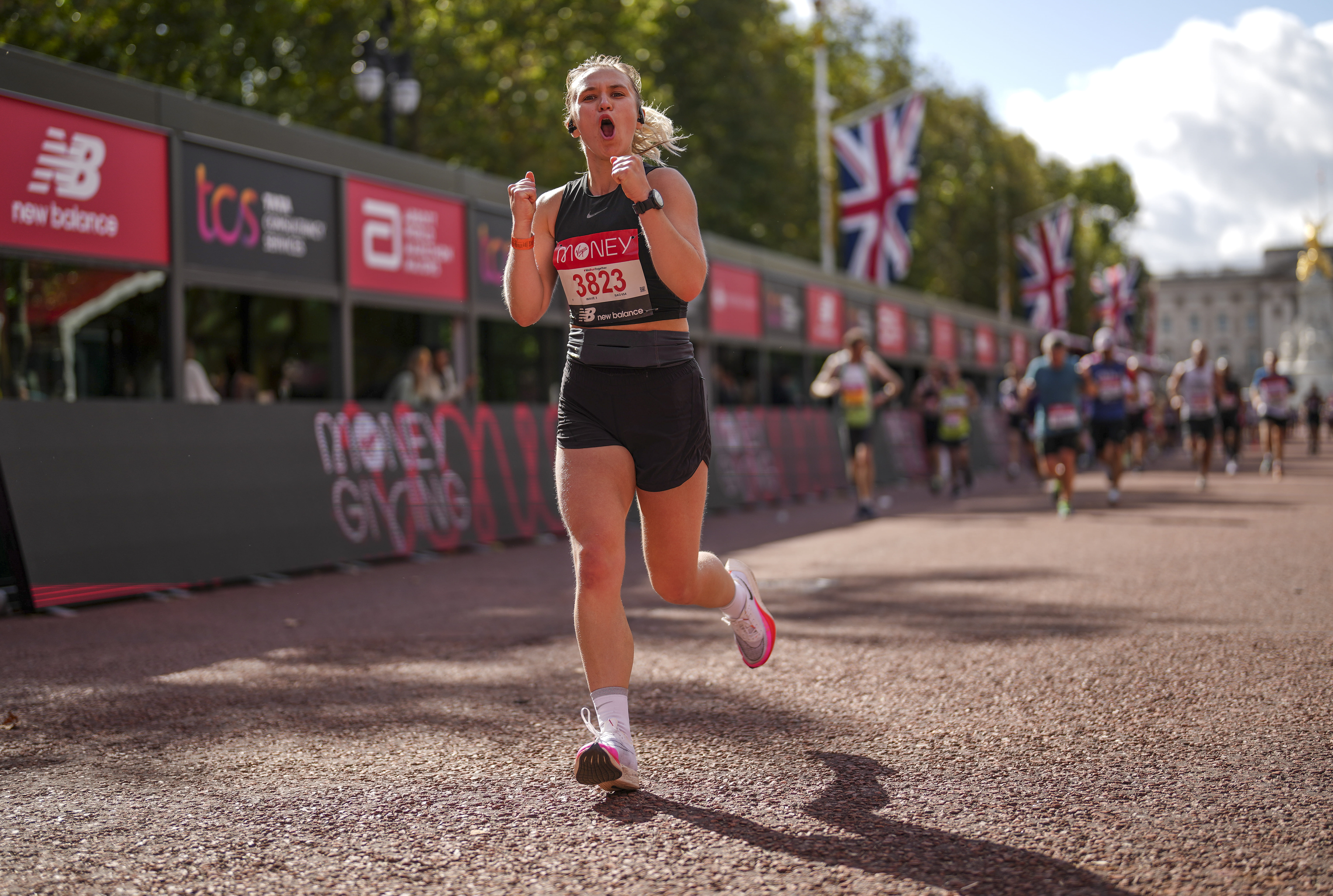
- 5 mins read
Run a marathon for charity
Whether it's your first or fifth marathon, entering a 26.2-mile race on behalf of a charity will elevate your experience! Here's how to get started.
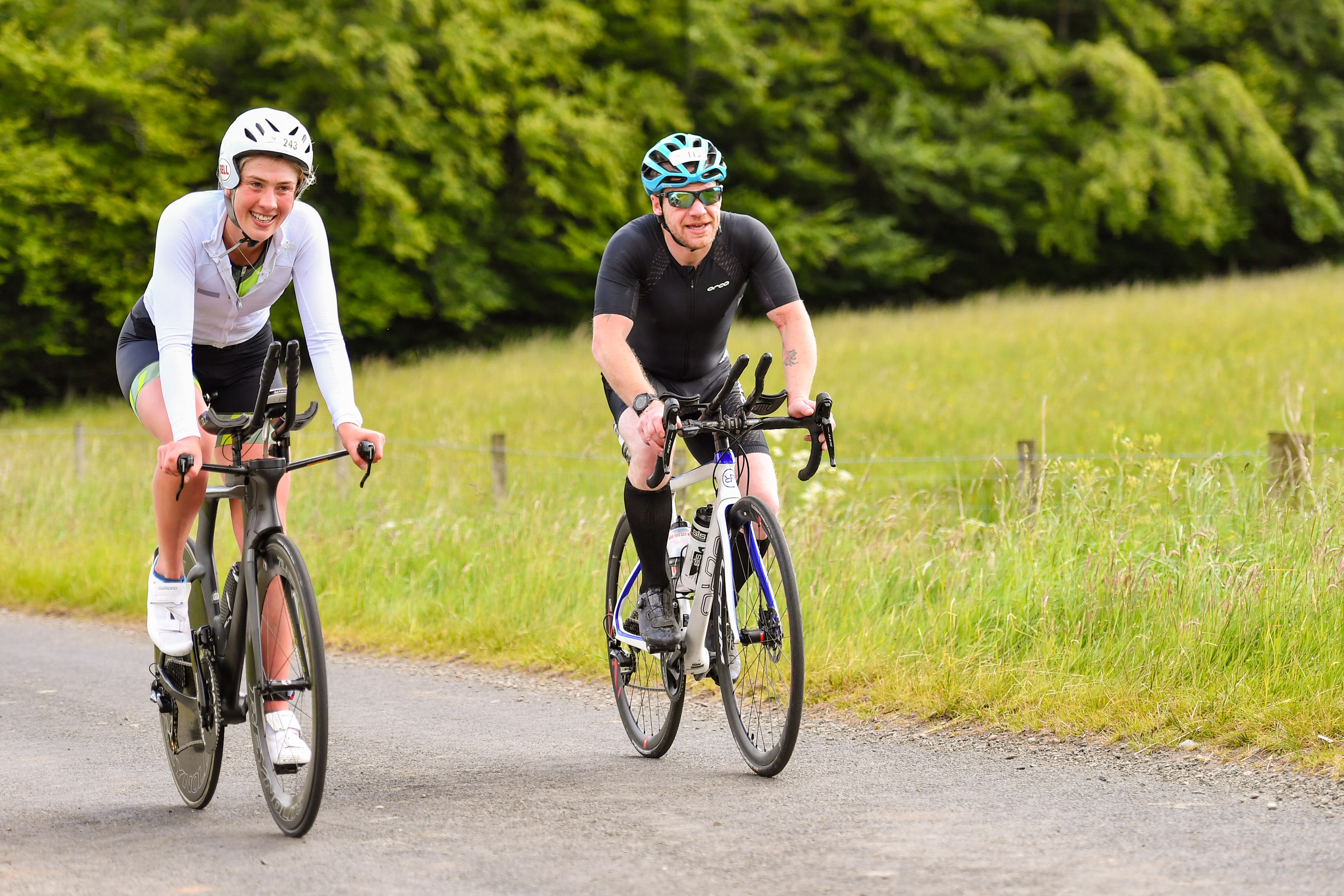
- 10 mins read
Enter your first triathlon
This dynamic multi-sport will test your speed and stamina, providing an incredible experience along the way! We've got everything you need for your first swim-bike-run right here.
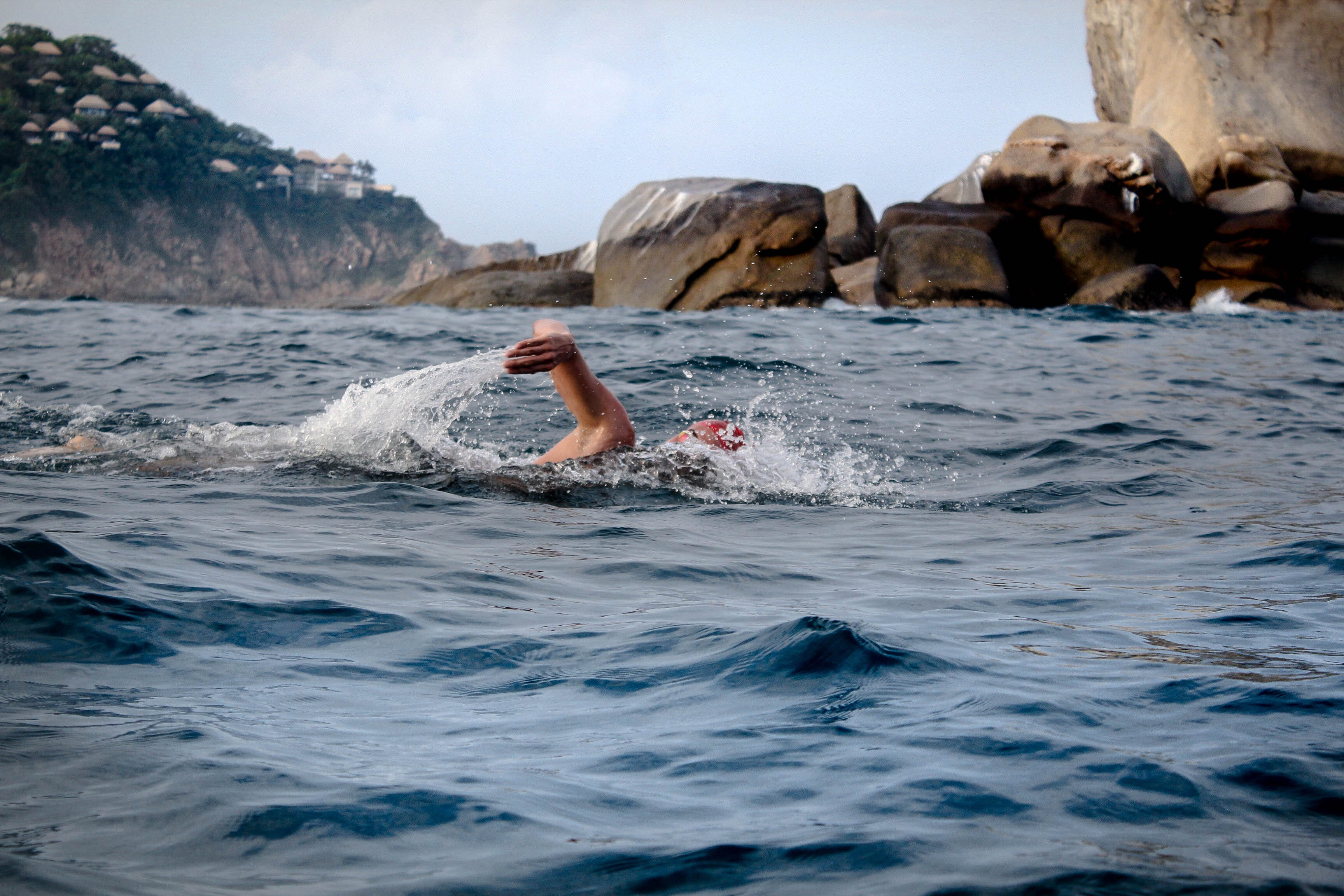
- 10 mins read
Dive in: how to start open water swimming
From sea swimming to an ice bath in your garden, cold water is having a moment. Diving into open water swimming helps you feel healthier and happier - we've got everything you need to get started.
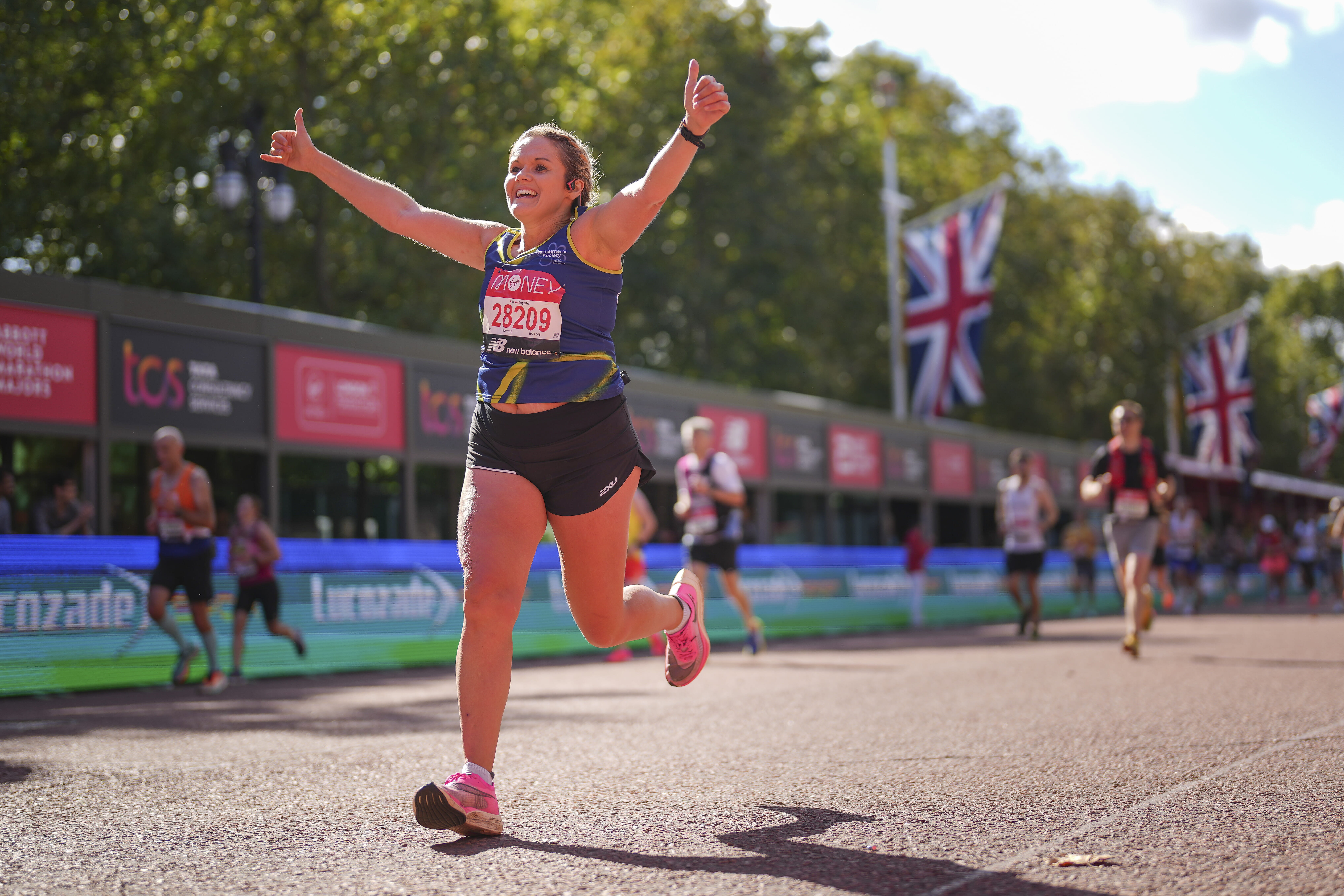
- 10 mins read
Running your first marathon
Signing up to run 26.2 miles for the first time will be one the most rewarding decisions you ever make! This guide has everything you need to get started, from training tips to a basic kit list.
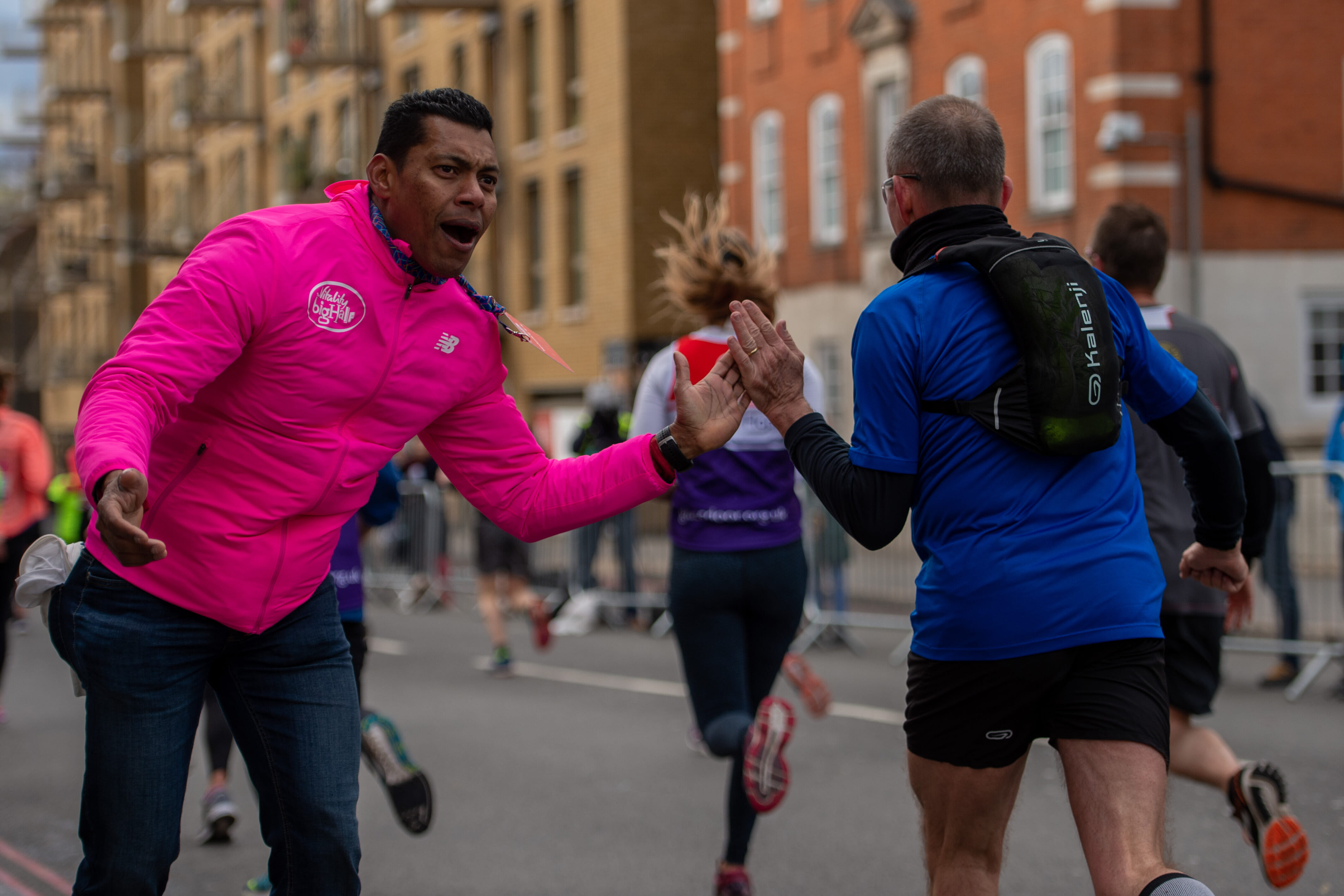
- 5 mins read
Run a half marathon for charity
Taking on a half marathon on behalf of a good cause could be exactly the challenge you need! This is all the information you need to get started.
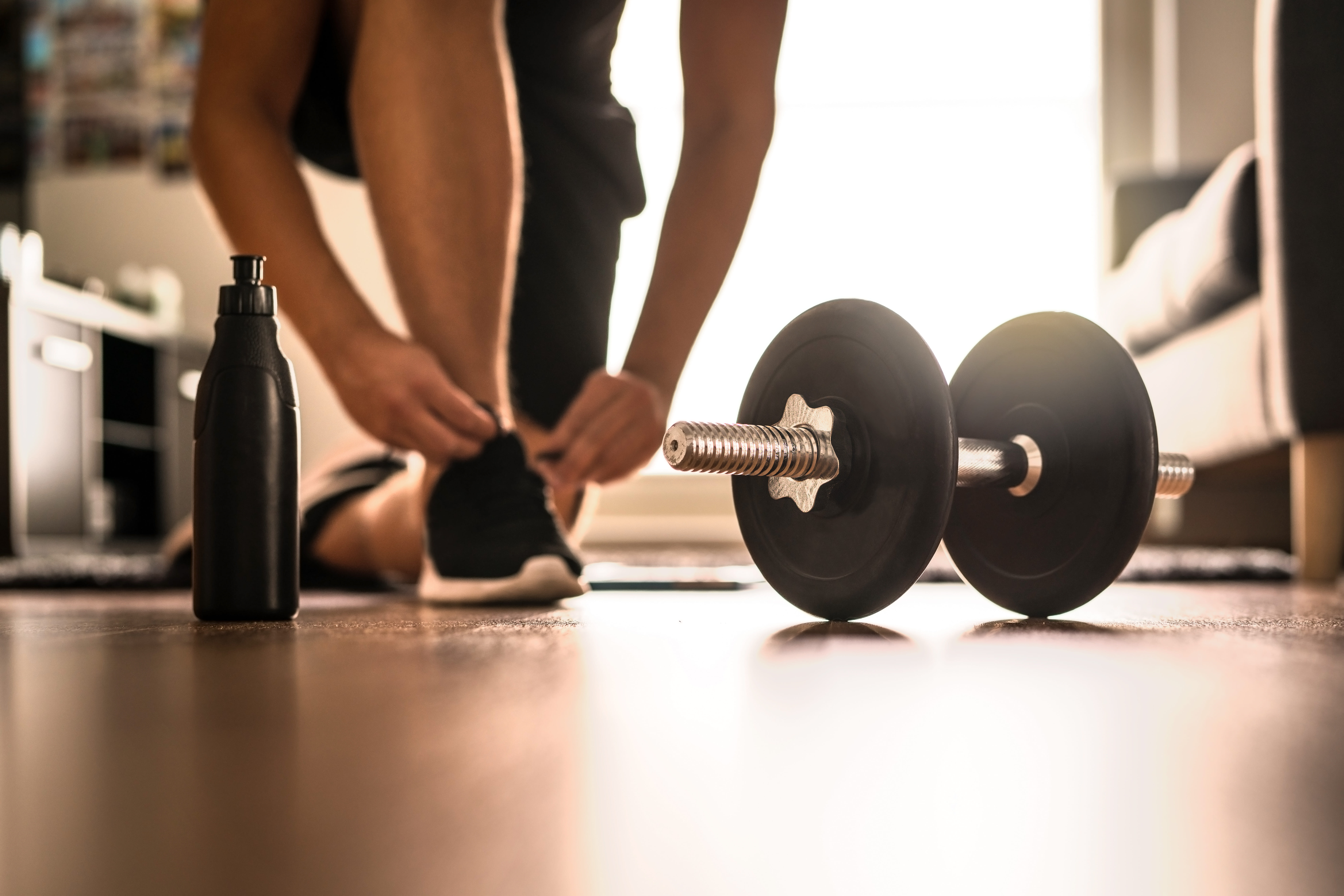
- 10 mins read
Cross-training for runners
Weightlifting, bodyweight exercises and yoga all have a place in improving your running form and staving off injury. This is your complete guide to cross training for runners.
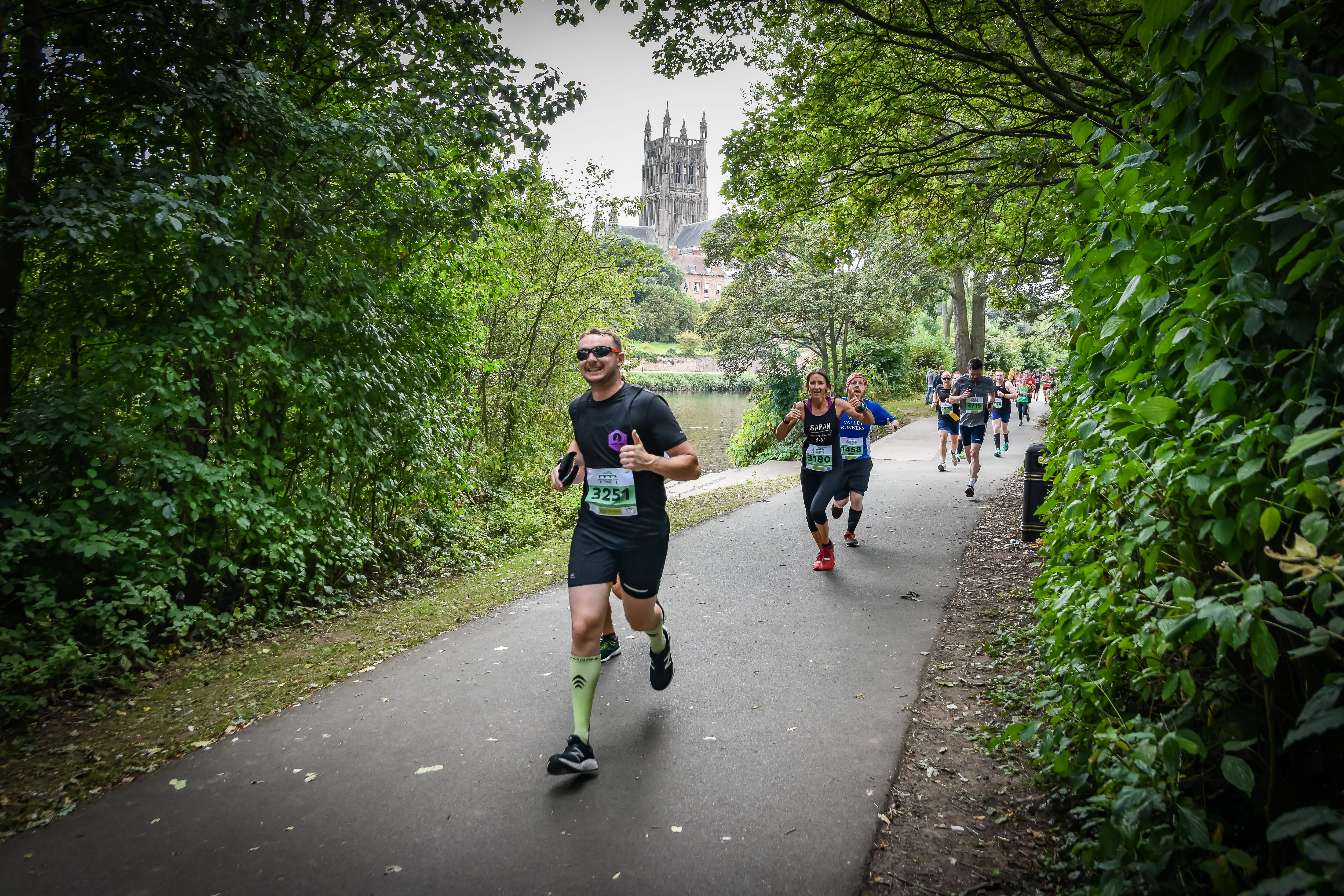
- 10 mins read
Running your first half marathon
Signing up to a half marathon for the first time can be both exciting and daunting in equal measure! This guide will run you through how to train for it and what to expect on the day.
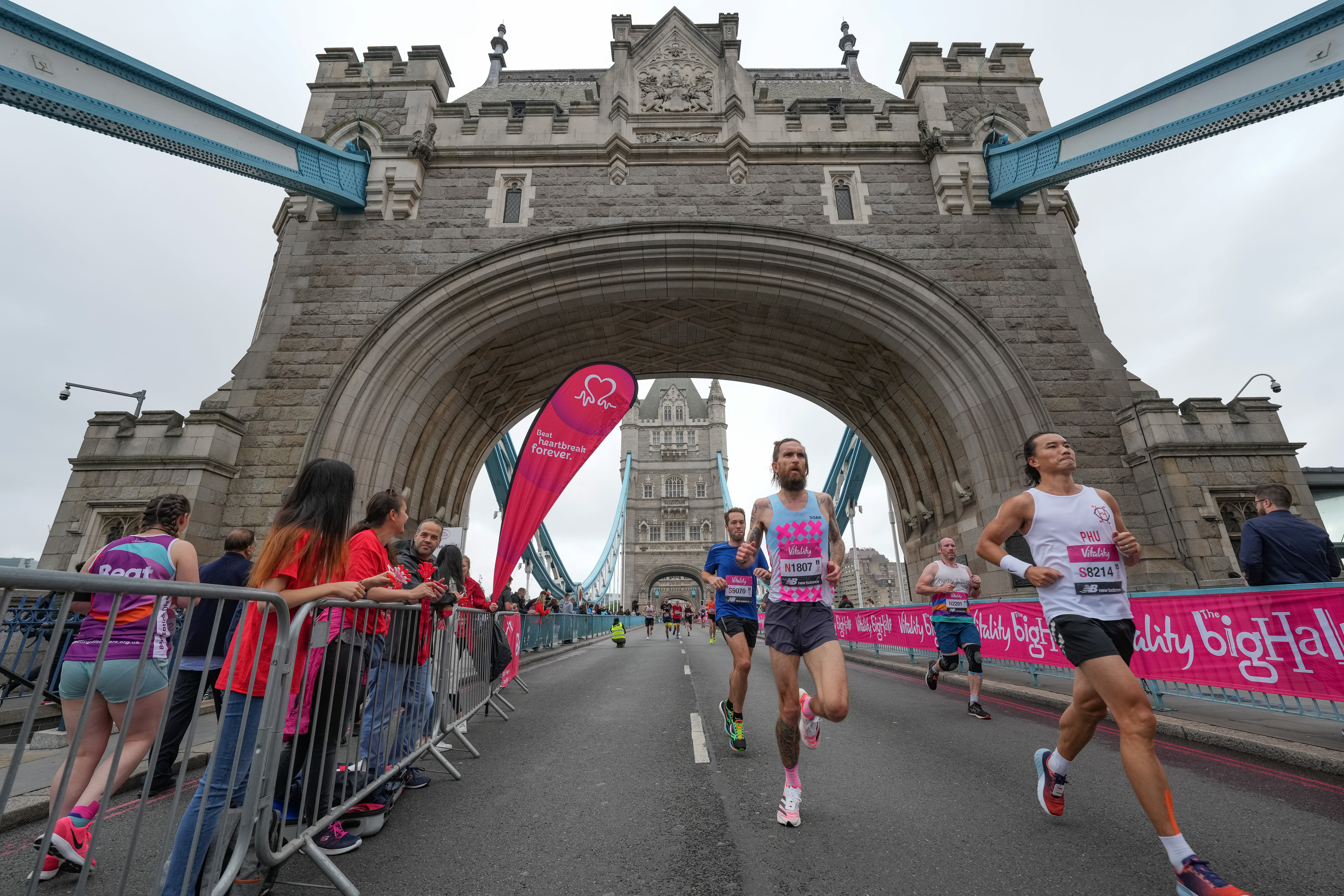
- 5 mins read
How long is a half marathon anyway?
The short answer: 13.1 miles. Understanding what that looks and feels like isn't that simple, though, so we've set out what it's like to run a half marathon bit by bit!
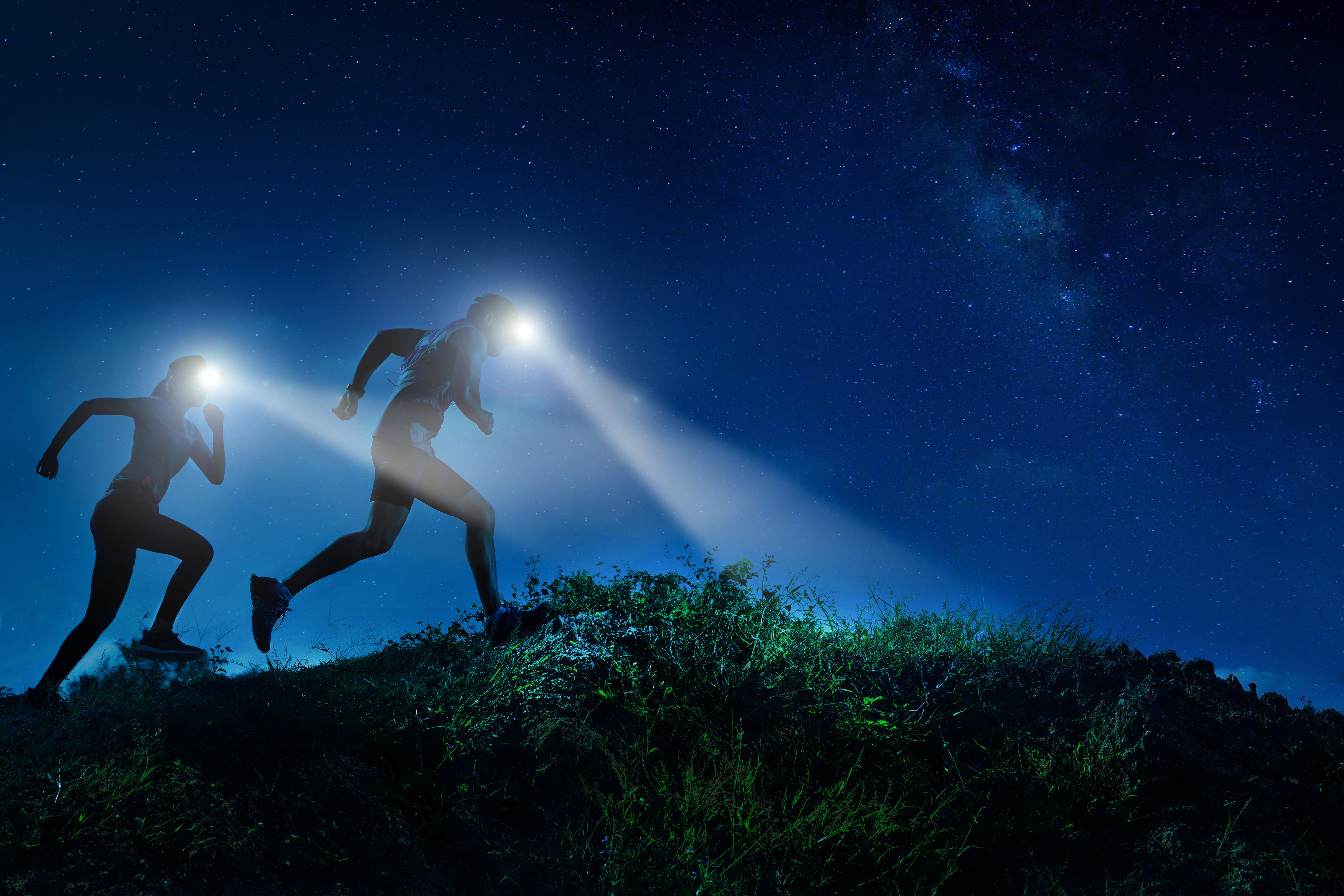
- 5 mins read
Running kit to wear in the dark
Just because the nights draw in doesn't mean you need to head indoors - with the right clothing and equipment, you can keep running through the winter!
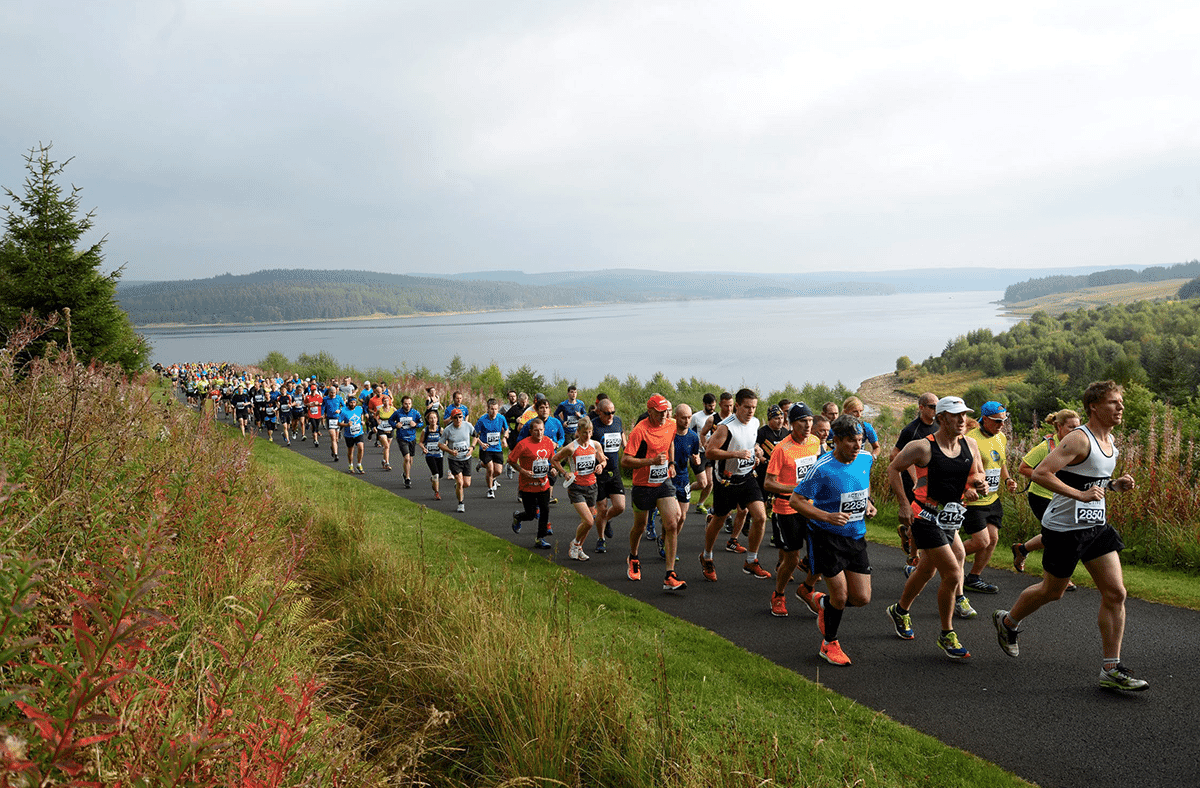
- 10 mins read
What is the best half marathon near me?
Looking for a half marathon this year? This is your guide to the best half marathons in the UK, organised into regions so you can find a race near you!
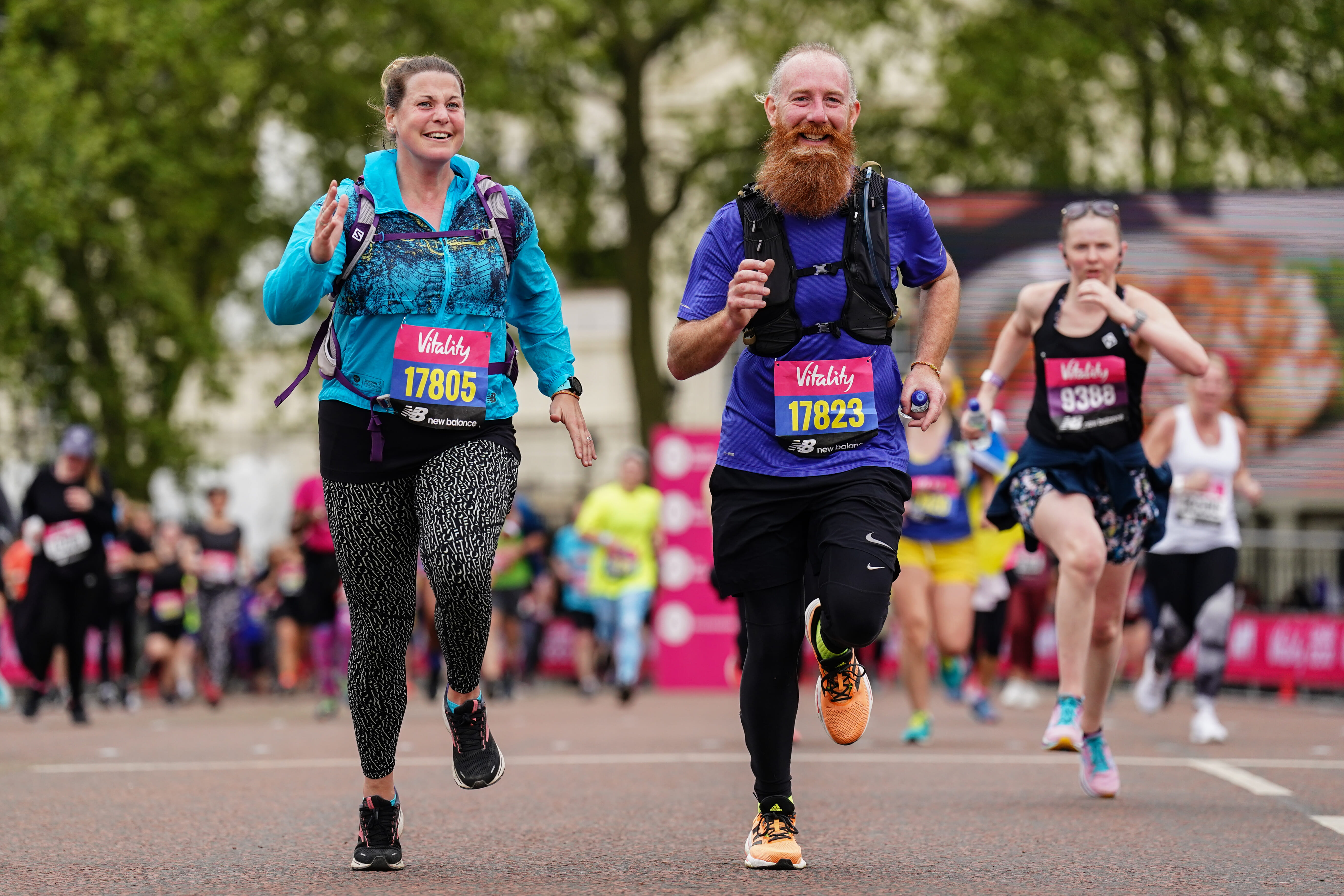
- 10 mins read
10K tips for beginner runners
This popular distance is great for both racing and exploring local trails, but where do you get started? Well, right here.
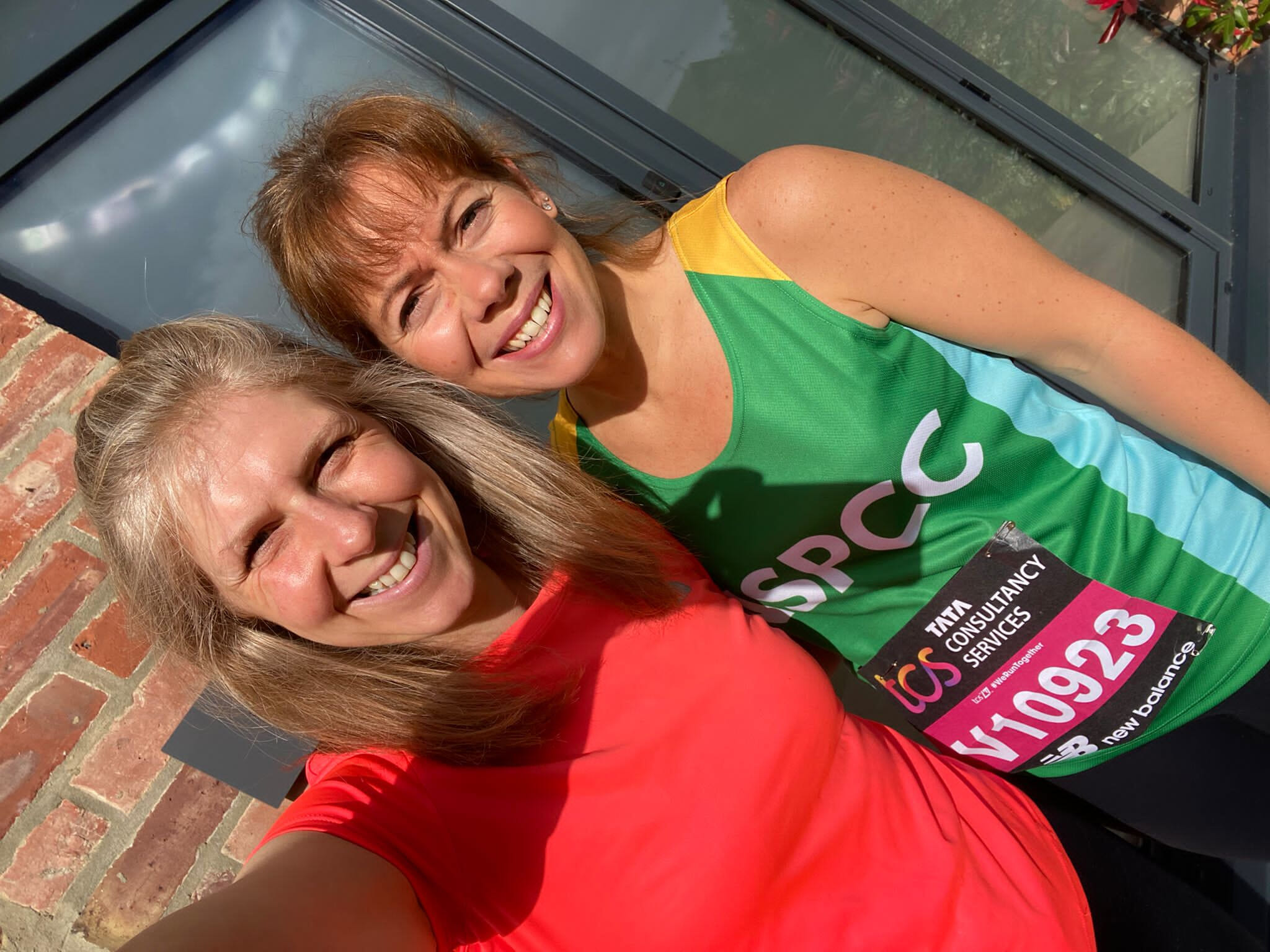
- 3 mins read
5 reasons to run the Virtual TCS London Marathon
Whether or not you entered the ballot for the TCS London Marathon, the virtual edition is a fantastic event with plenty to offer. Here's what we learned!
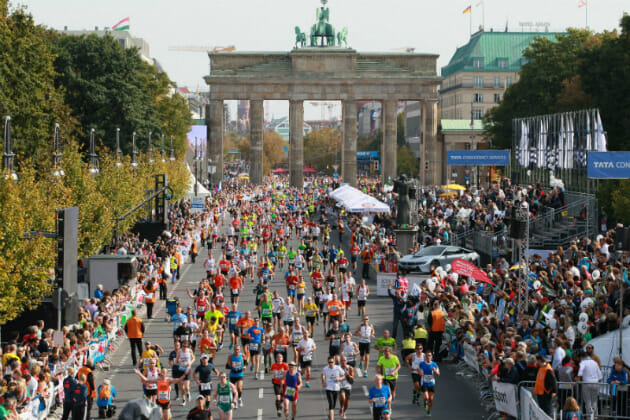
- 5 mins read
Your guide to the BMW Berlin Marathon
Considered to be the fastest marathon in the world, Berlin is a brilliant choice for any runner, whether it's your first 26.2-mile race or you're looking for a PB!
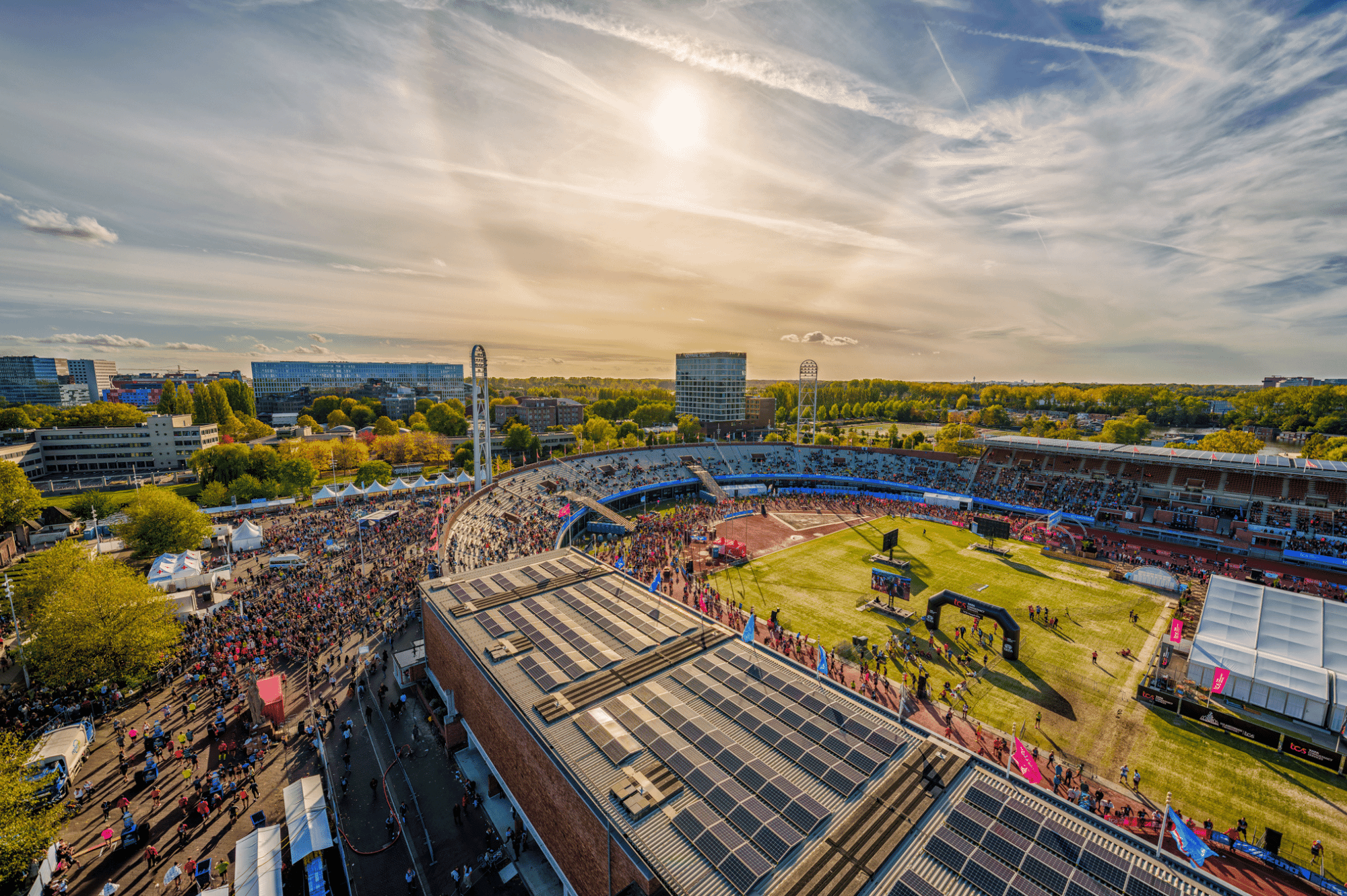
- 5 mins read
Your guide to the TCS Amsterdam Marathon
One of the fastest marathons in the world, Amsterdam is a brilliant fusion of a great running experience and a superb cultural immersion. This is everything you need to know!
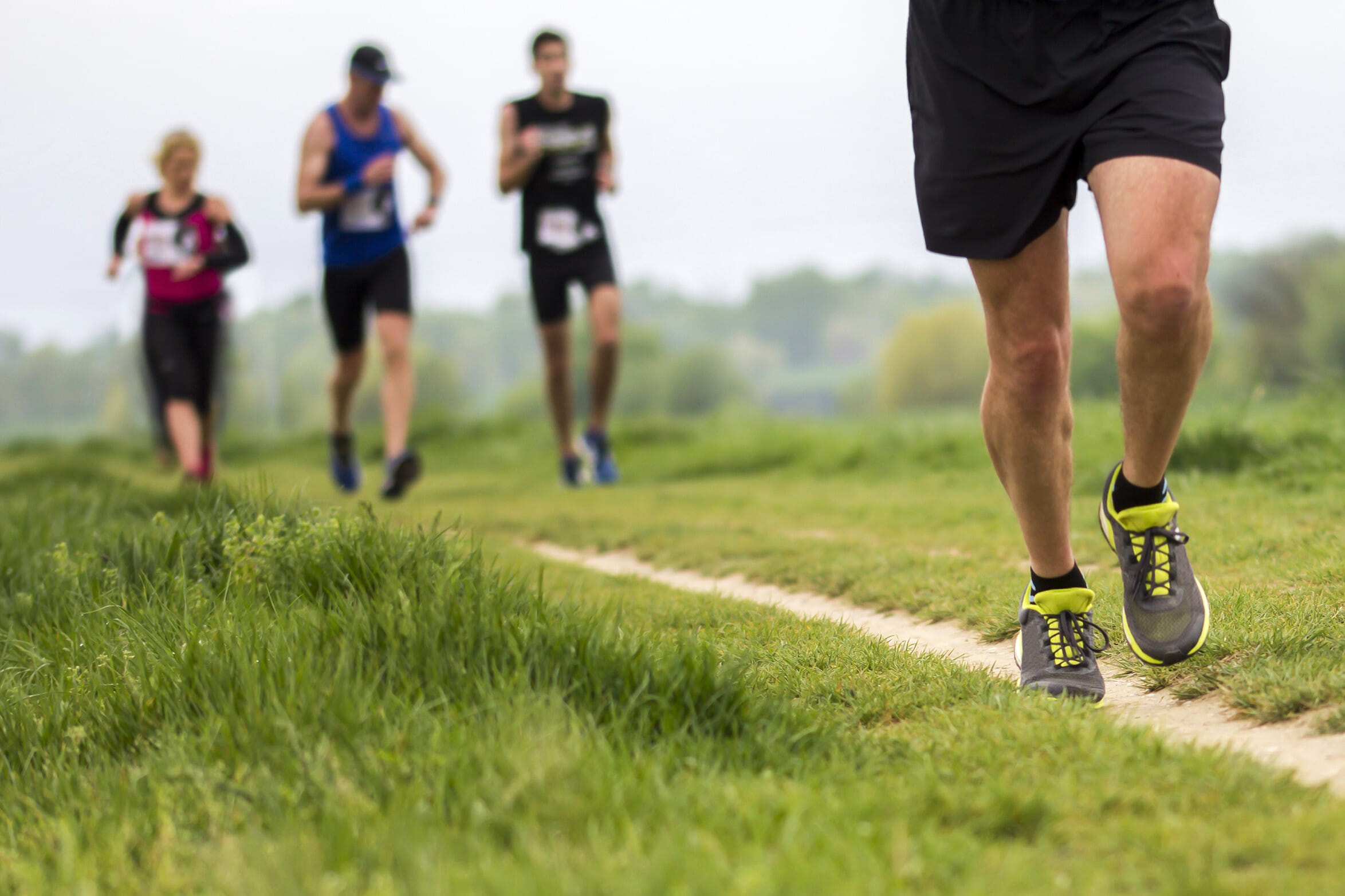
- 10 mins read
The beginner's guide to duathlons
Run-bike-runs aren't just for triathletes in the winter - they're a serious multi-sport discipline in their own right, getting people active outdoors on road and trails alike.
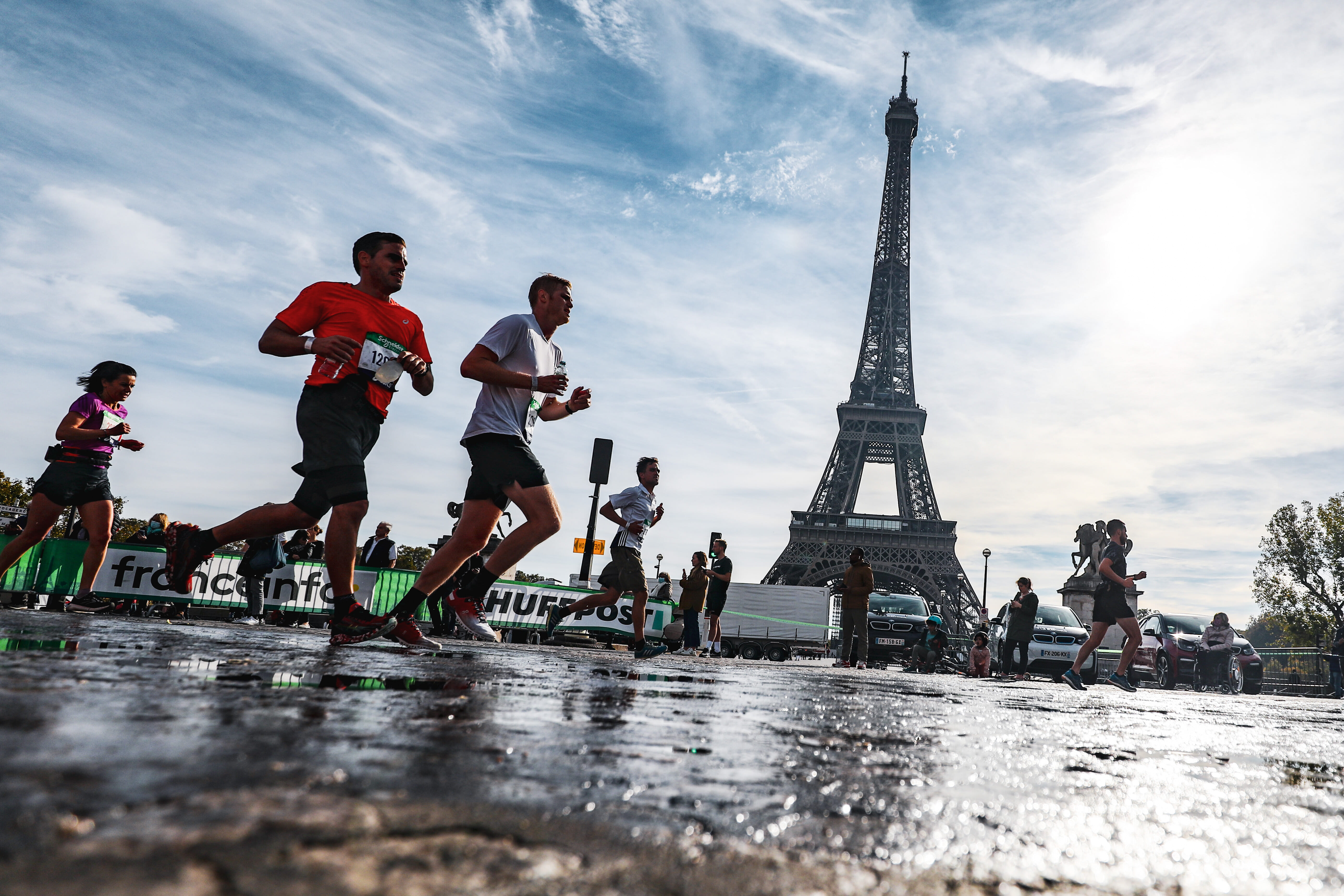
- 5 mins read
Your guide to the Paris Marathon
The second largest marathon in the world, the Schneider Electric Paris Marathon attracts 65,000 runners to the French capital for an incredible route and an international EXPO.
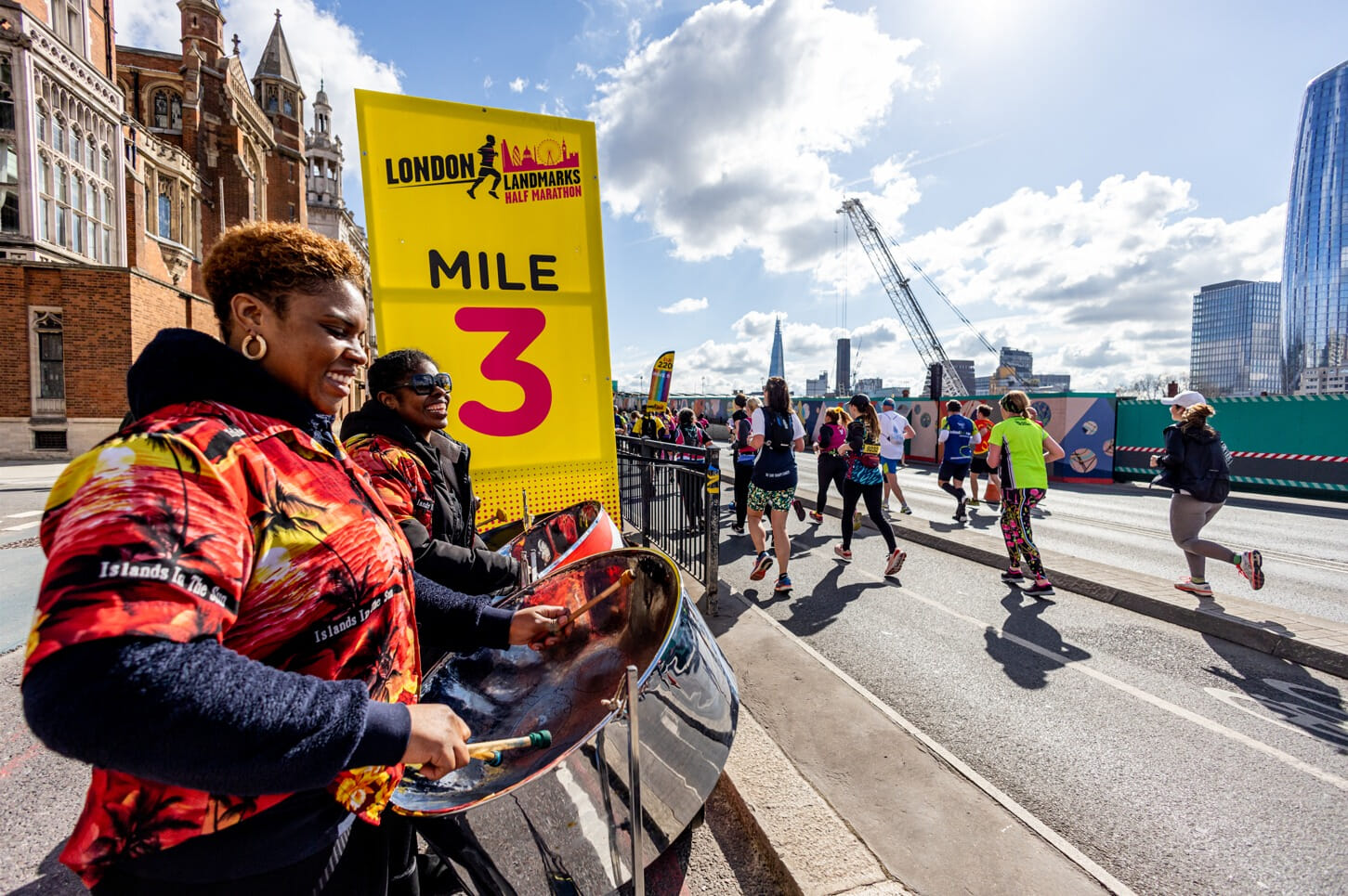
- 5 mins read
Your guide to the London Landmarks Half Marathon
The only half marathon to run through Westminster and the City of London, this is a fantastic race touring the capital's most iconic landmarks. This is everything you need to know about the race!
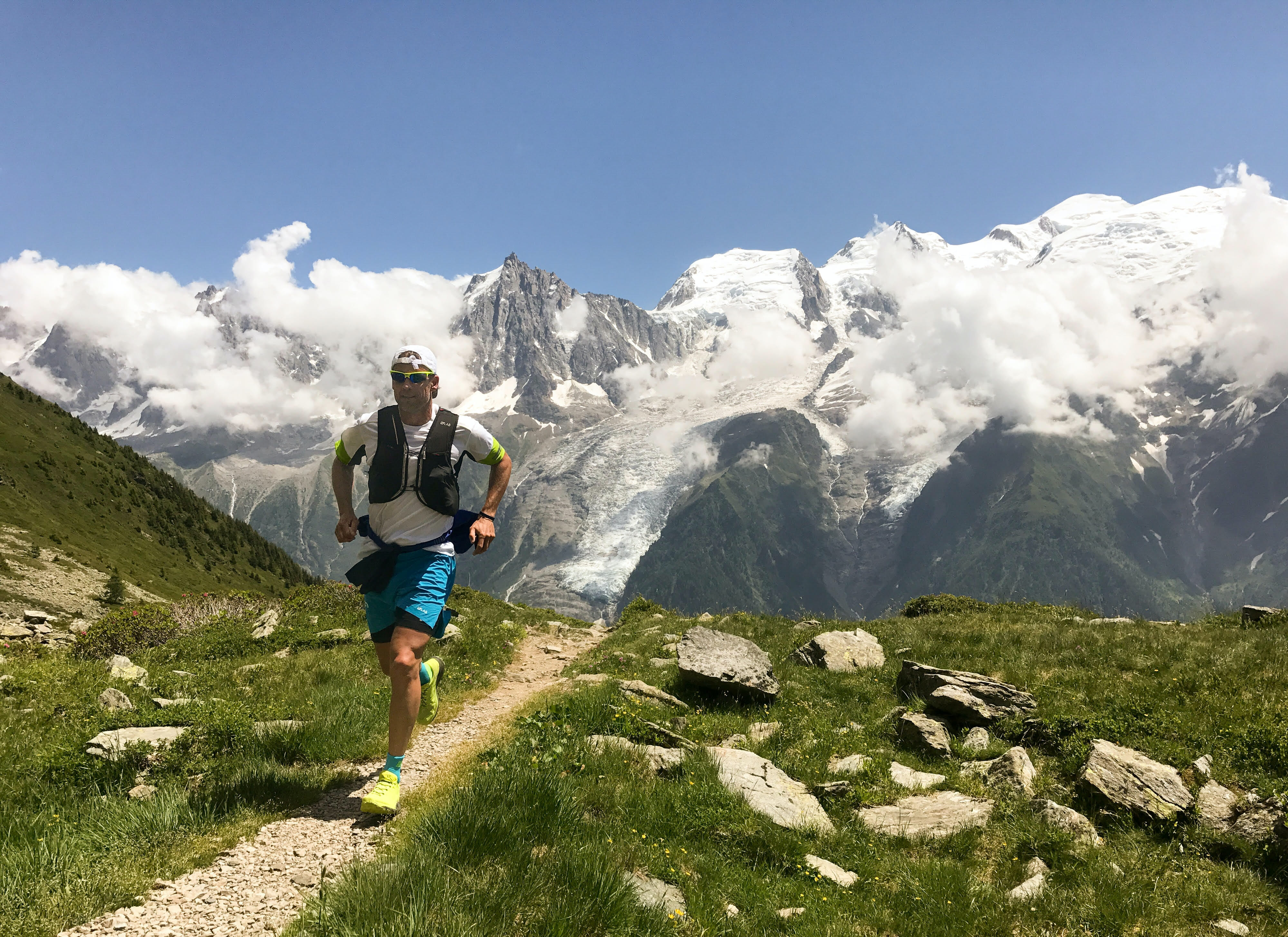
- 5 mins read
What to wear for trail running
Adventure, exploration and freedom are at the heart of what makes trail running so addictive - to make sure you're getting the most from your experience, get kitted up and be trail-ready.
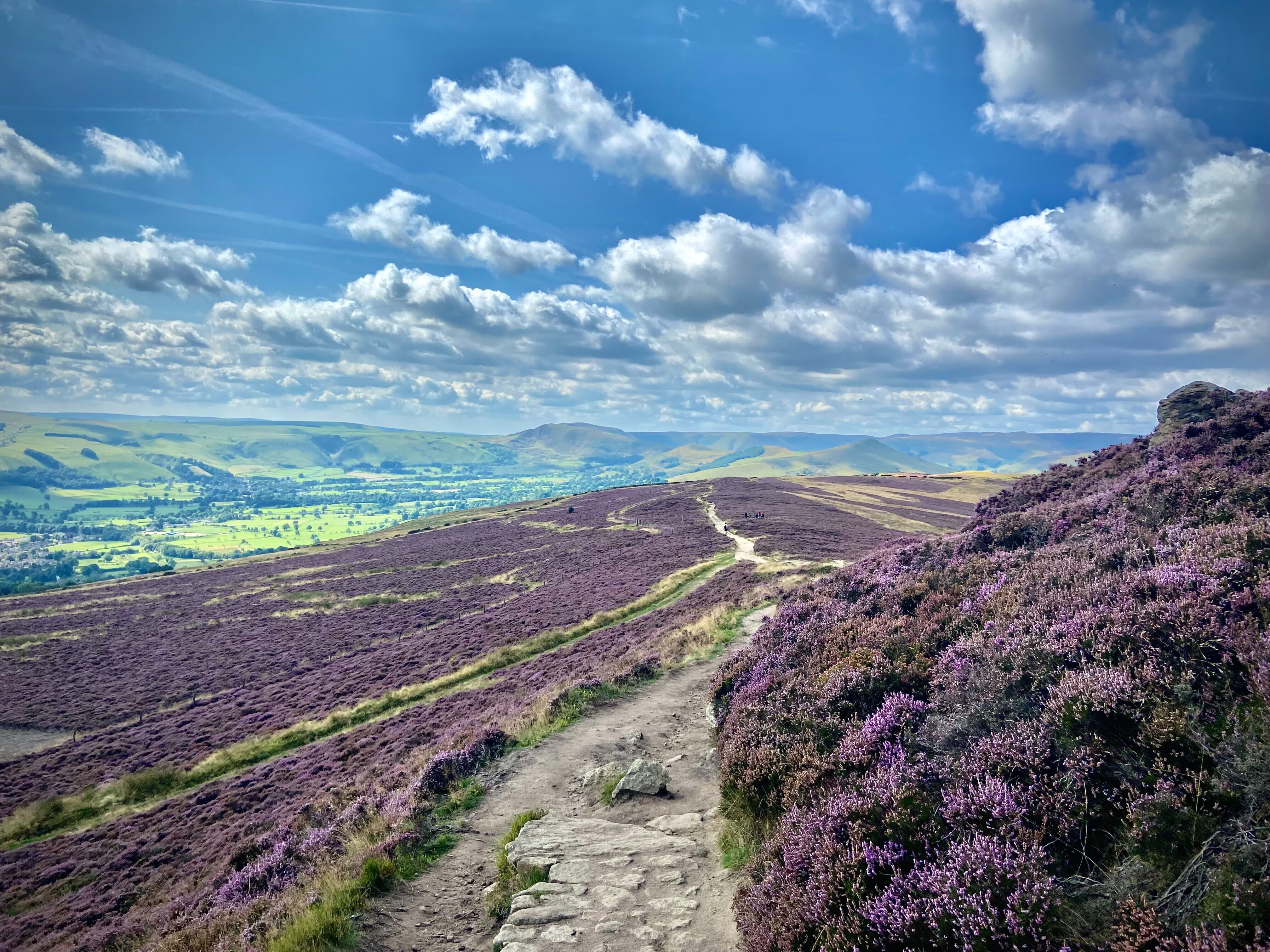
- 5 mins read
The best places in the UK for trail running
We're spoilt for choice when it comes to off-road routes in the UK but if you're looking for some inspiration, this is where you'll find it!
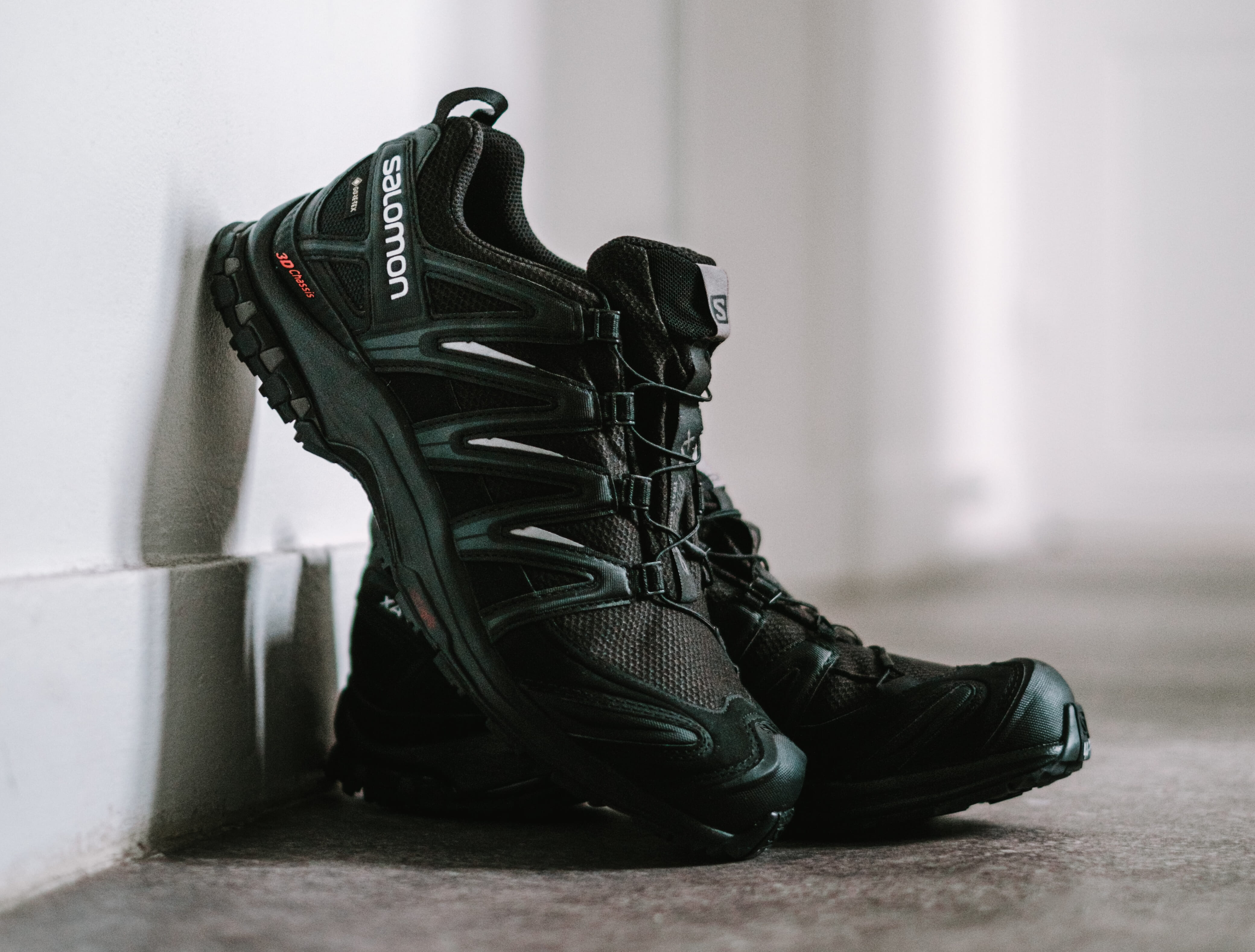
- 5 mins read
Everything you need to know about trail running shoes
Lugs, rock plates and cushioned midsoles - what are they and why do you need them?
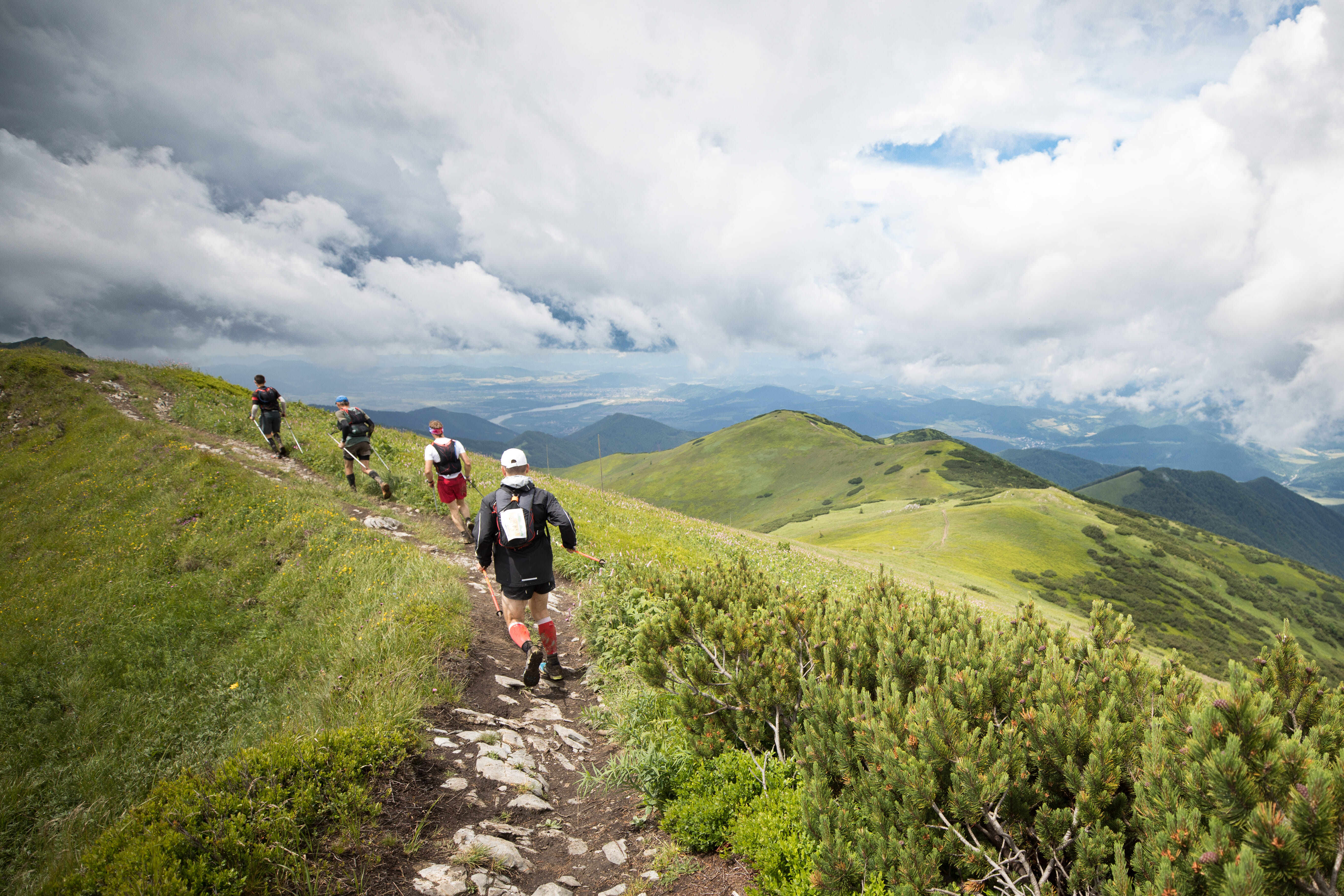
- 10 mins read
The beginner's guide to trail running
Off-road running is on the march, with new races being announced and more people keen to escape the hustle and bustle of modern life. This is everything you need to know to get involved.
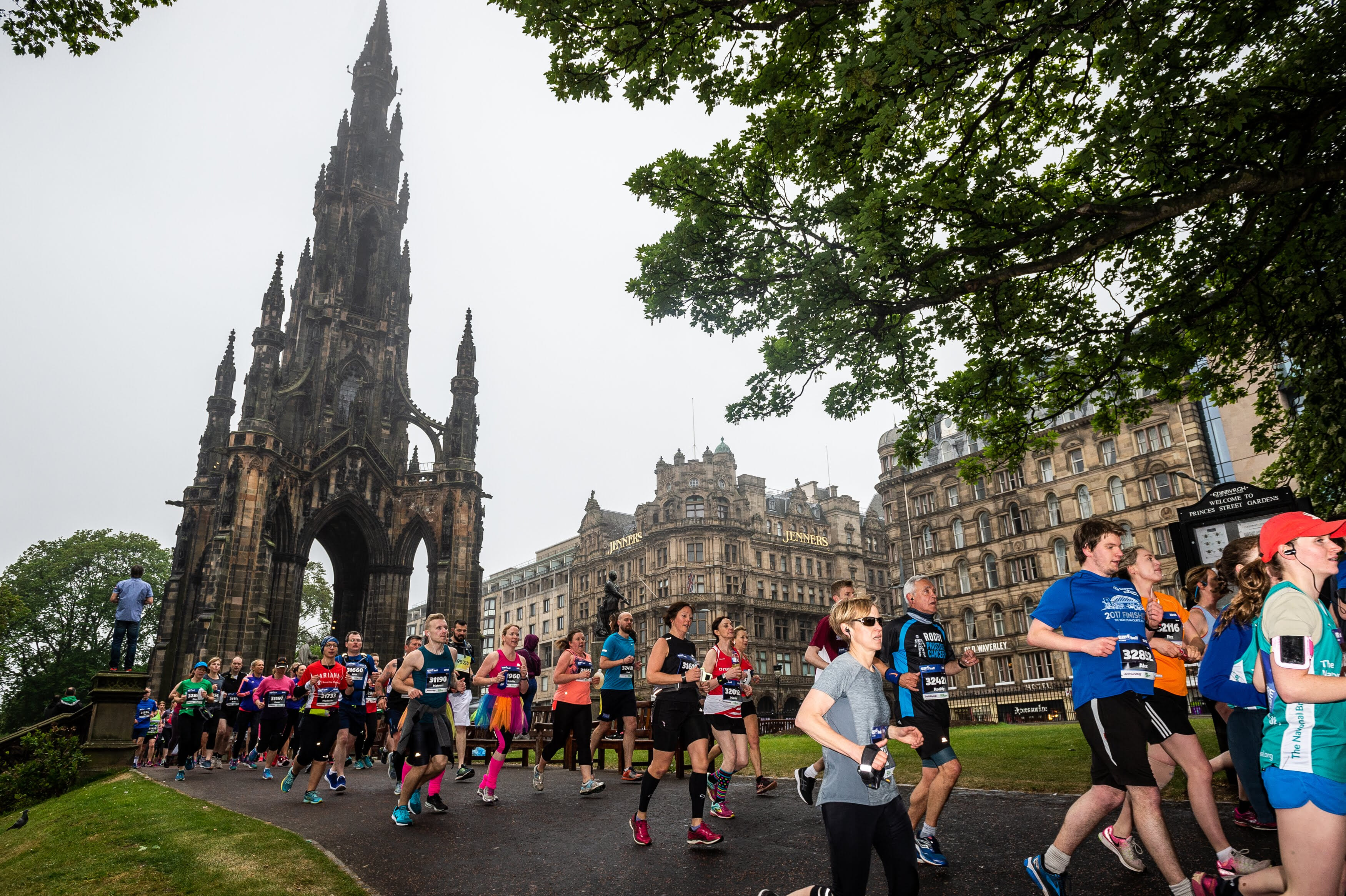
- 10 mins read
Your guide to the Edinburgh Marathon
Alongside the headline 26.2-mile run, there are eight other races to choose from at this vibrant festival in the Scottish capital.

- 5 mins read
Your guide to the adidas Manchester Marathon
Known as one of the UK's fastest, flattest and friendliest marathons, this popular 26.2-mile race attracts thousands of runners each year to the North West's biggest city.
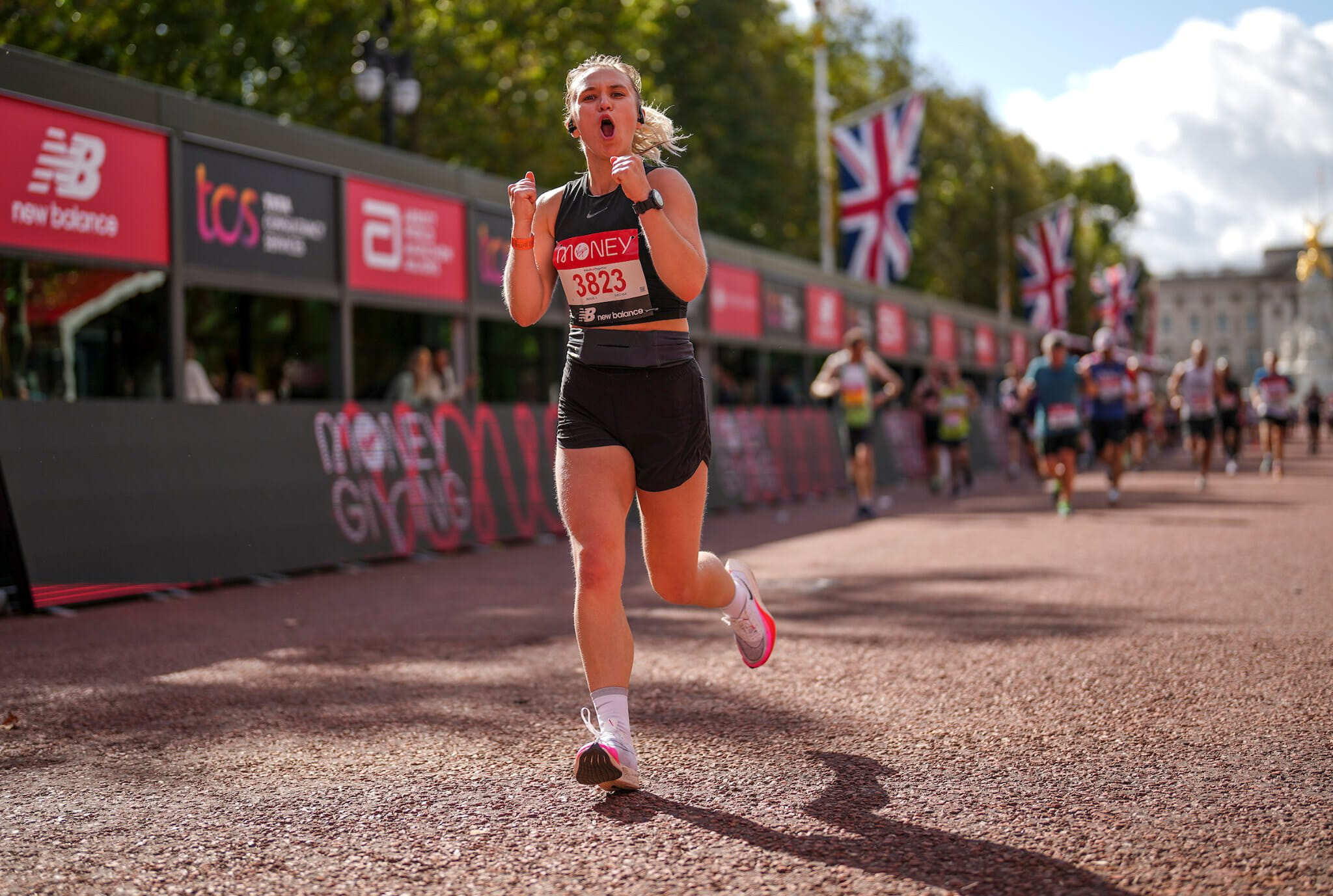
- 5 mins read
Race 101: the TCS London Marathon
The biggest marathon in the UK - and one of the biggest in the world - is an event that every runner wants to tick off their bucket list. Here, we deal with the most-asked questions on the web!
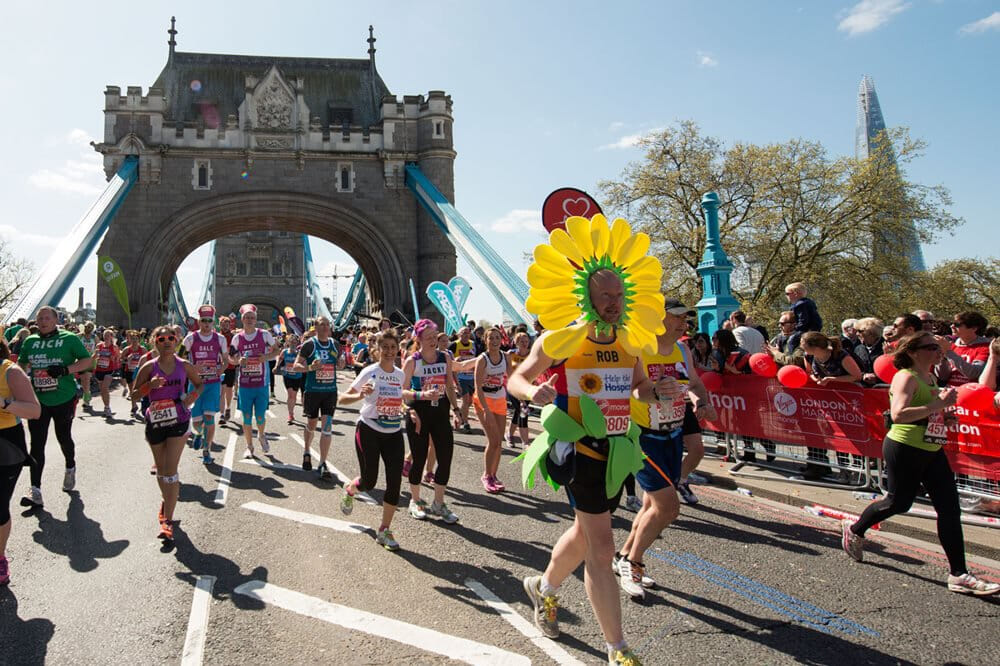
- 5 mins read
Run for charity in the TCS London Marathon
This iconic event is always oversubscribed at the ballot but there are plenty of charities to run for and plenty more reasons to do so.
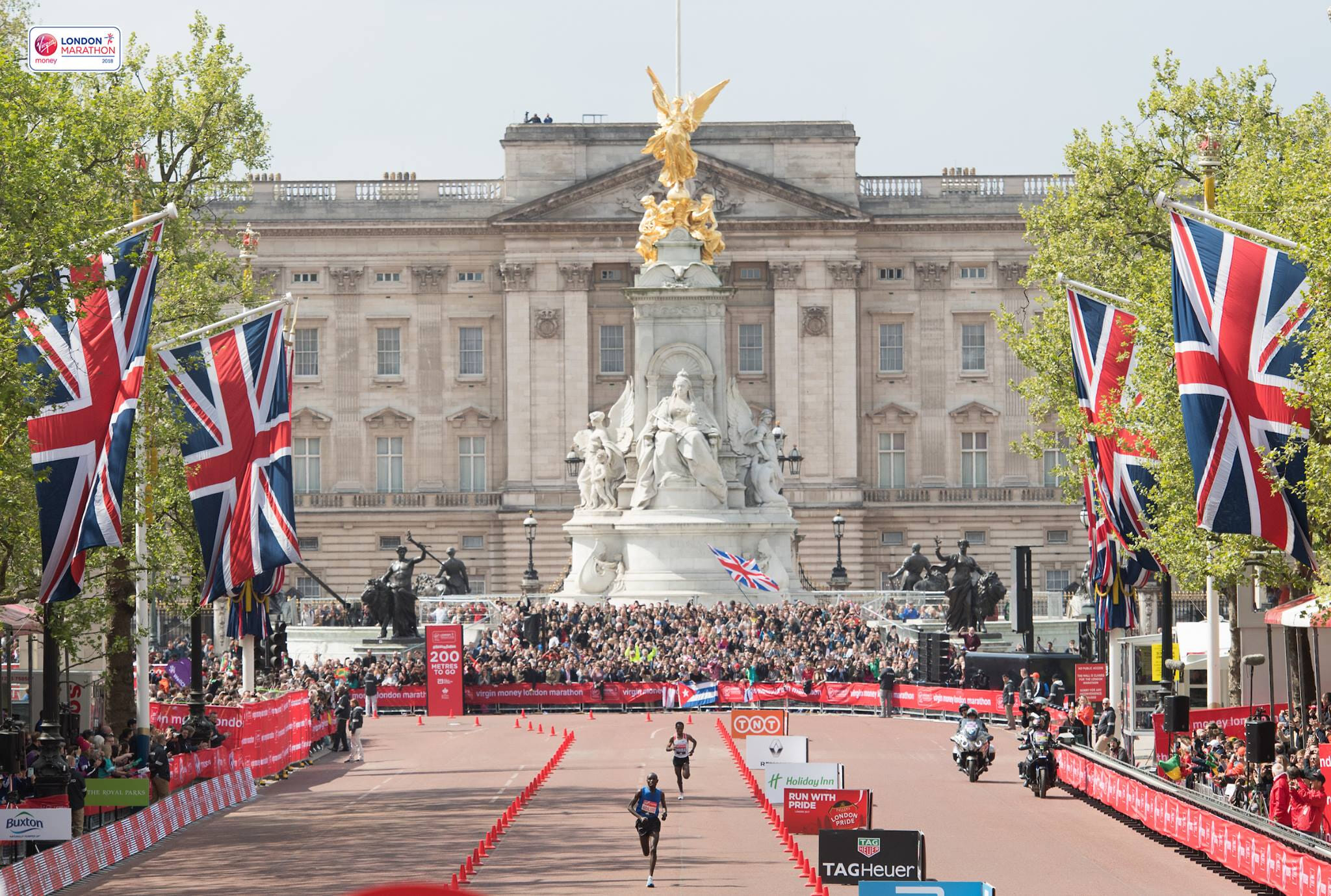
- 5 mins read
Your guide to the TCS London Marathon
This is the UK's biggest marathon and one of the greatest in the world - here's what you need to know!
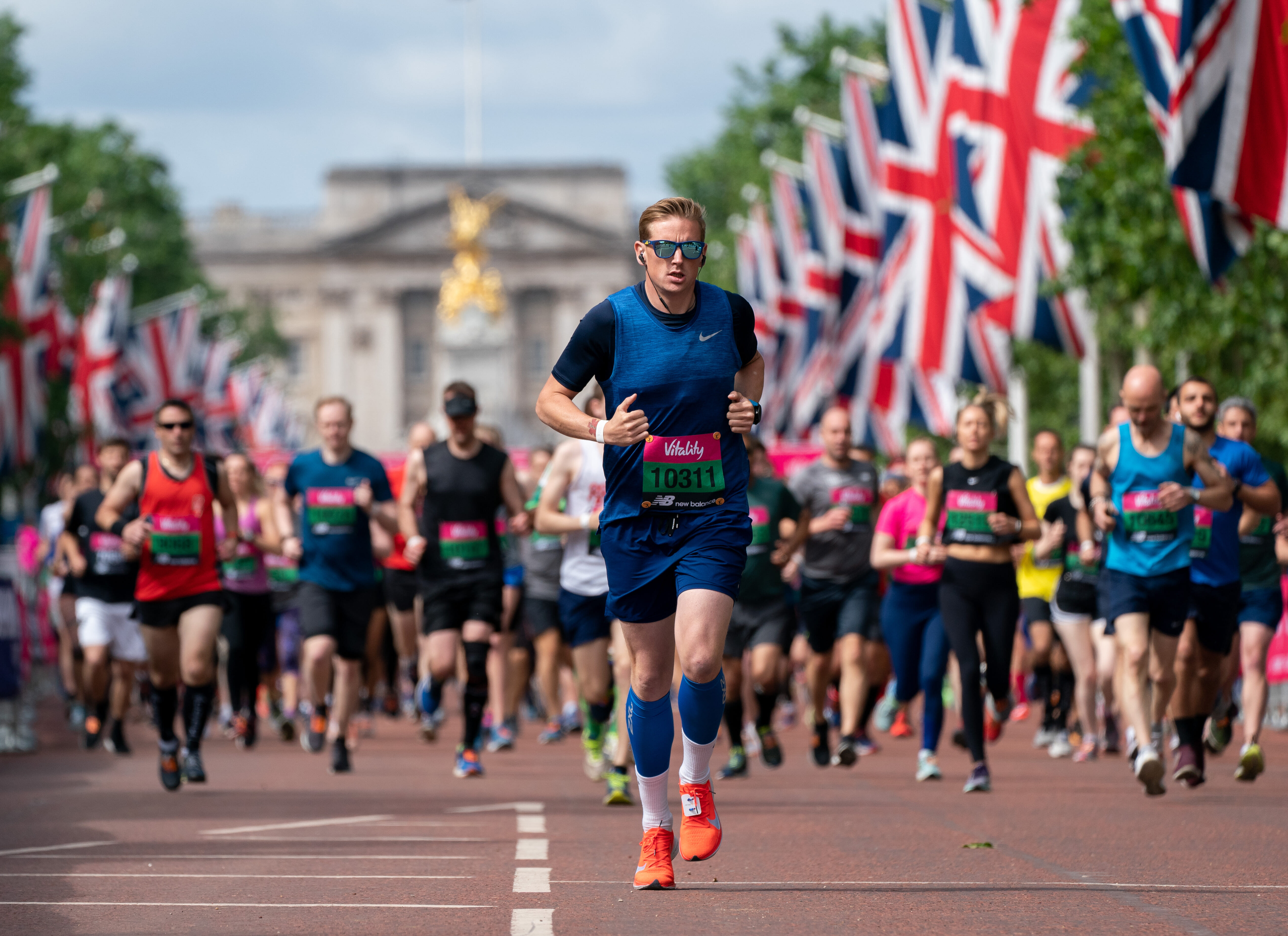
- 5 mins read
The top 25 events in the UK
These mass participation runs, bike rides and triathlons are the most popular outdoor events for a reason!
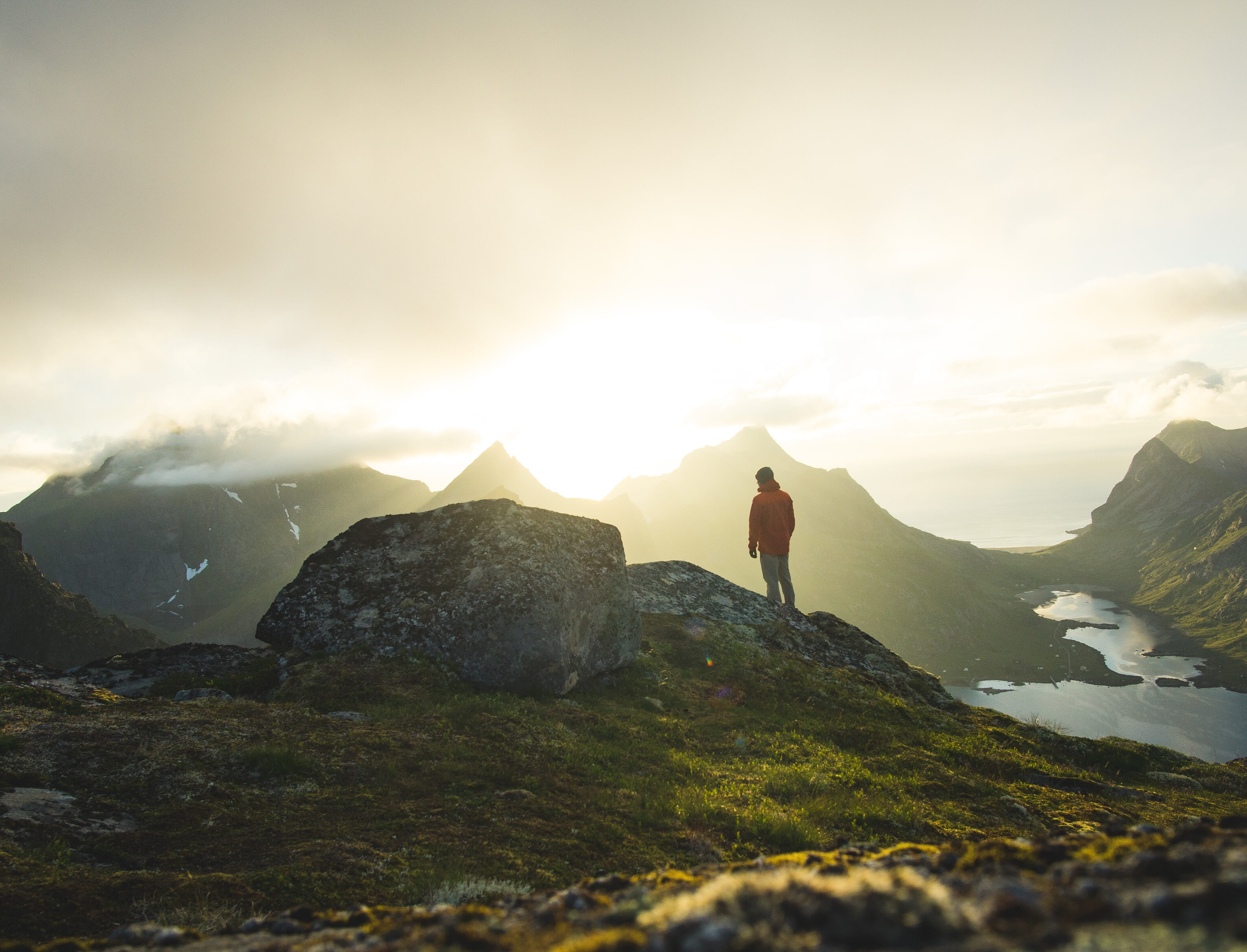
- 5 mins read
Why spending time outdoors is essential
Whether it's a grand adventure or a humble walk in the woods, being active outdoors is the best thing for your health and happiness - here's why.
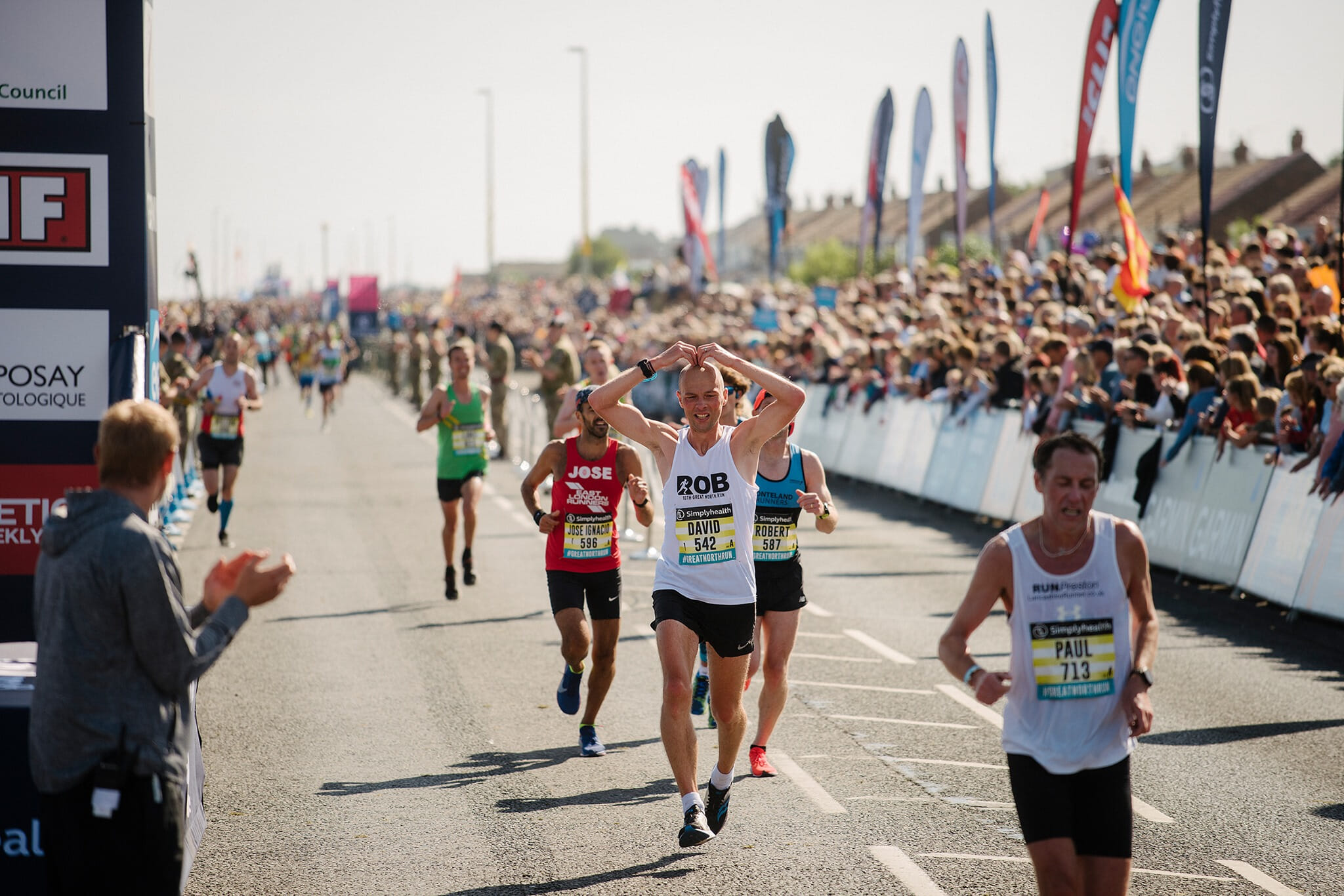
- 5 mins read
Race 101: the Great North Run
All your questions about the Great North Run answered in one place, helping you to take the plunge and get involved!
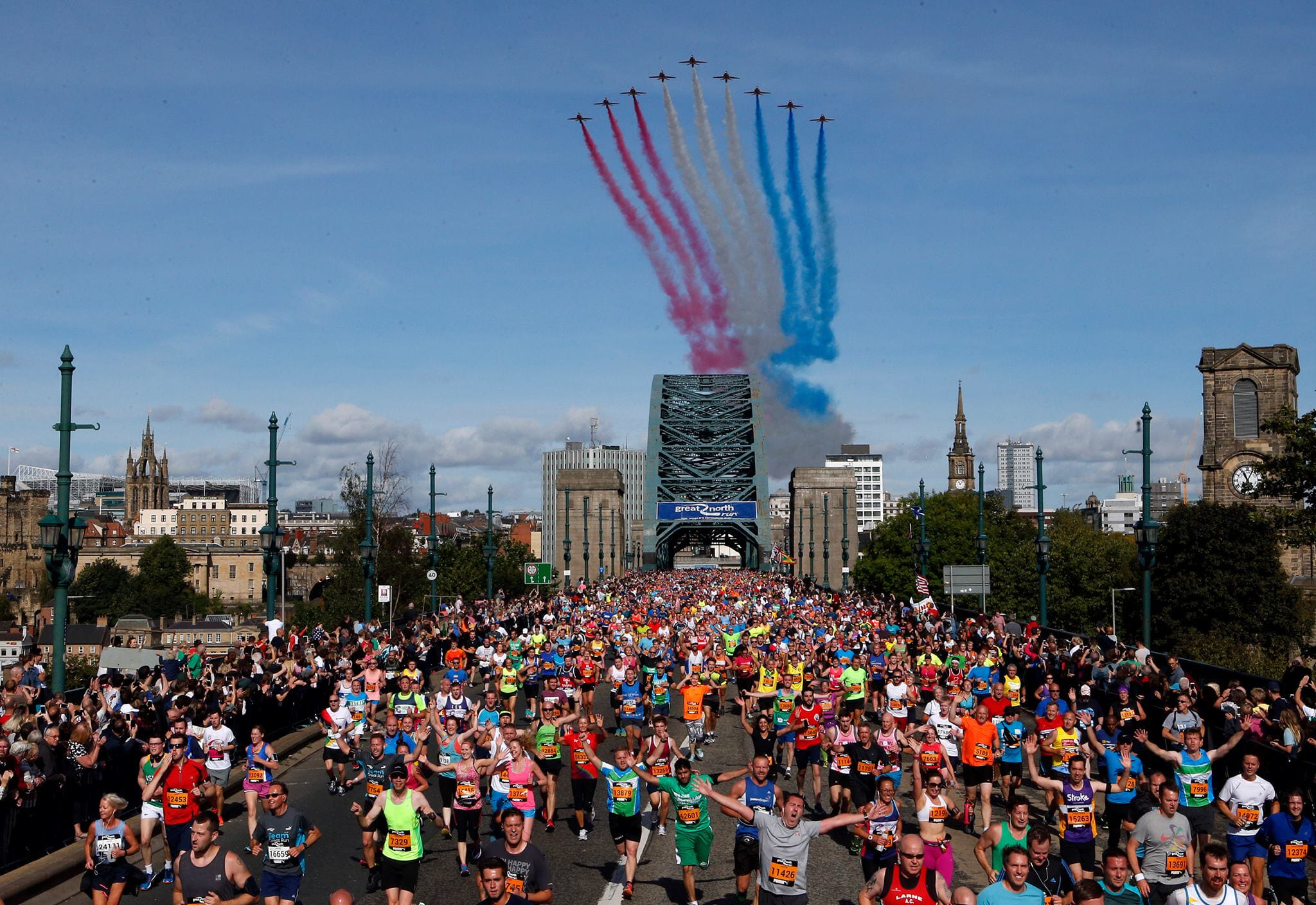
- 10 mins read
13 reasons to enter the biggest half marathon in the world
The Great North Run attracts 57,000 runners each year to the North East, all keen to enjoy its world-famous atmosphere!
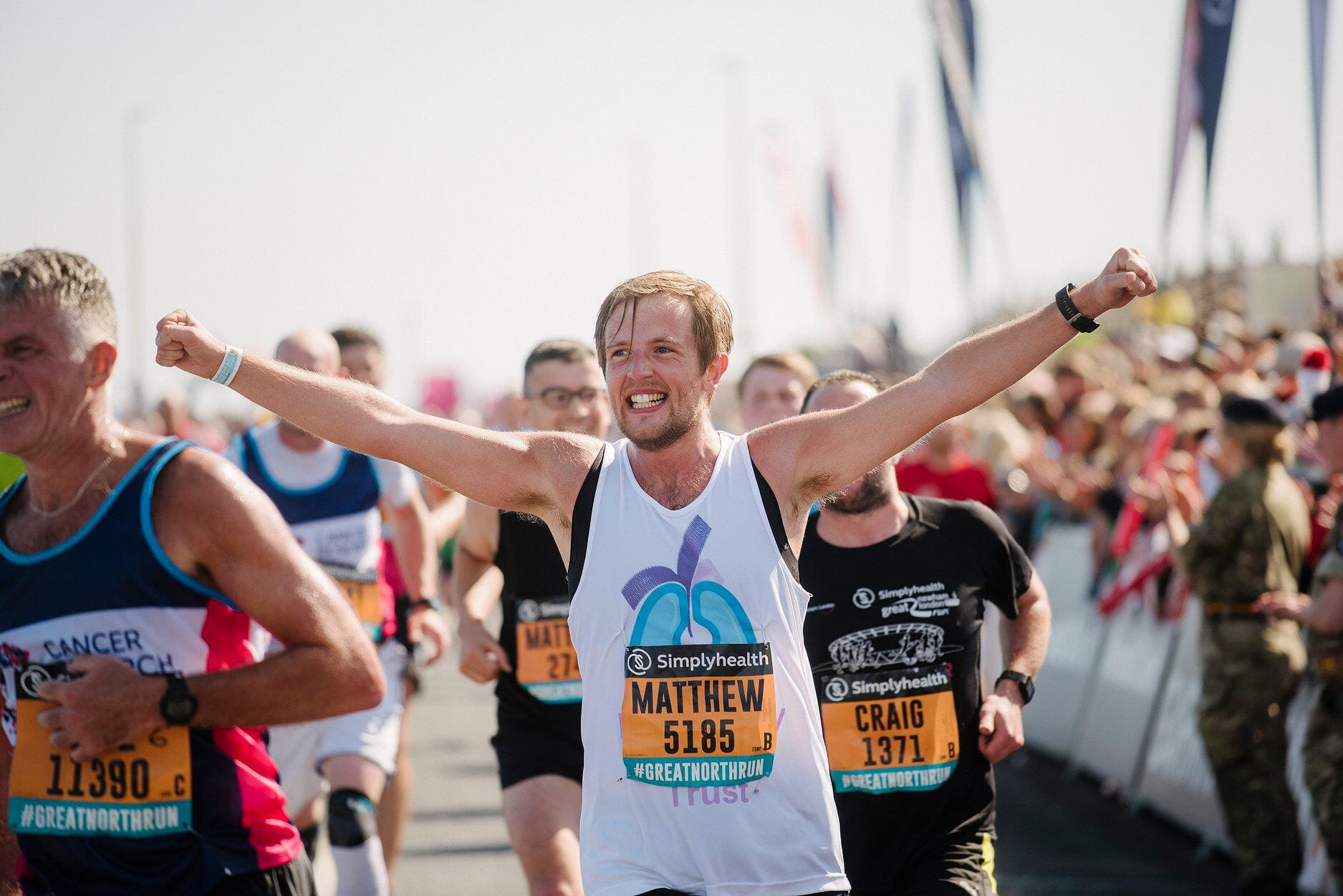
- 5 mins read
Run for charity in the Great North Run
There are a huge range of fantastic charities with places available for this popular half marathon every year - and this is how you can get involved.